|
Post by lars on Nov 12, 2017 21:42:38 GMT
And so I've started another instrument project. Lookwise it will be a copy of the Regal Octofone from the twenties. A lovely looking instrument that according to the advertisements could be played as eight different instruments - hence the name. You could concider it as a small bodied octave mandola och a tenor mandola or a double strung tenor guitar. The original instrument was apparently very fragile and light built. I've never seen one in real life, but I fell in love with the looks and decided to make an instrument inspired by it. Here is a link with good information about the instrument from Jake Wildwood: 1930 Regal OctofoneAs I don't want to violate copyright I can't share any images of the original instrument here. But here is my mould to give you an idea of the body shape; 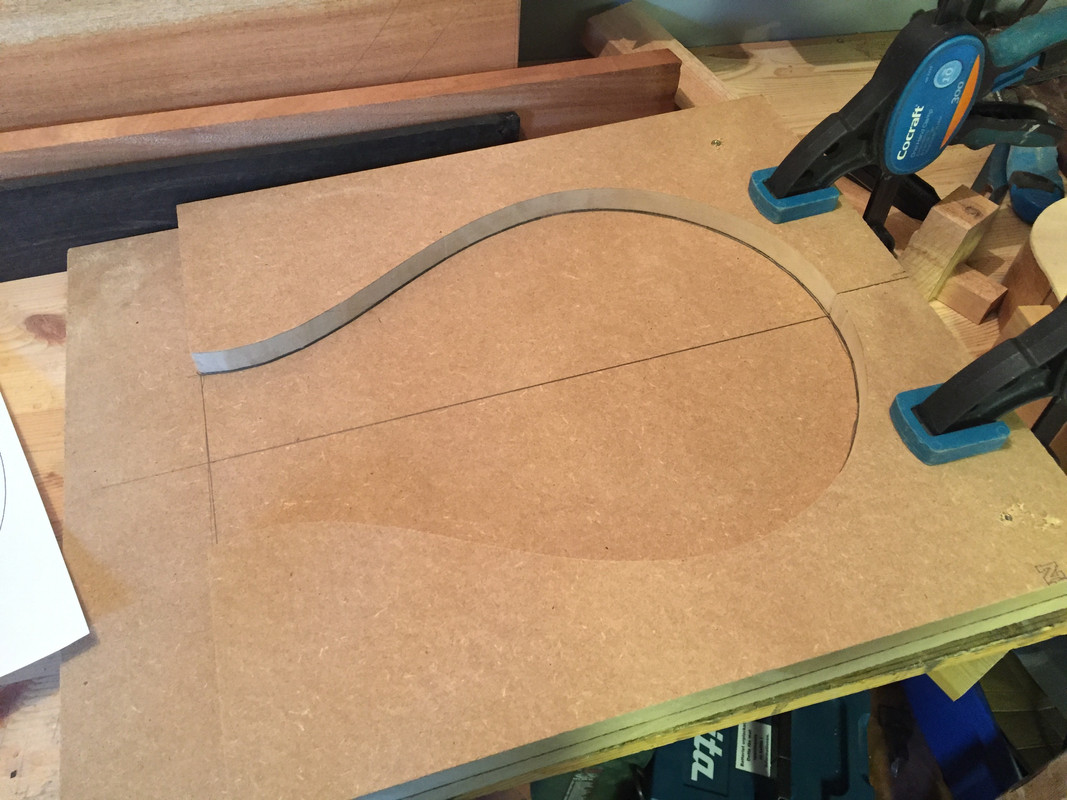 The original design was very simple, and in parts I'll keep it that way. For example I will let the top and back be true flat. And the neck block covers the hole front of the body. So what might seem like a complicated double cutaway with twin- points ( a bit like Gary Navas twinpoint mandolins) is relly just a fancy shaped, very large neck block. So here are the neck and tail blocks: 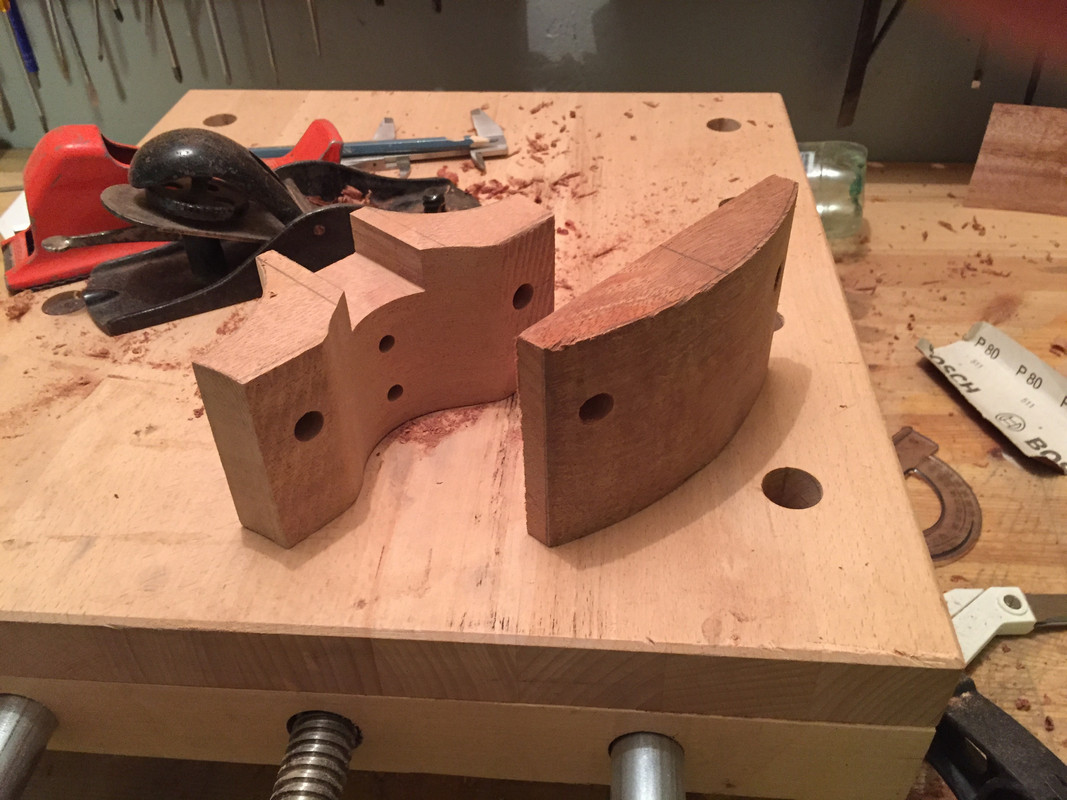 As you can see there are holes for the carbon fibre rods that will go through the body. That is NOT part of the original design! And by the way - specifications. The original octofone was a spruce/birch instrument. I like birch very much and have used it for some previous instruments, but I won't use it this time. Top: European spruce Back, sides, neck- and tail block, neck: African mahogany (Khaya) Fret board: Either ebony or ebonized laburnum. Bindings: I don't know yet. I'd like to have ebony, but I don't have access to that yet. First I glued the sides to the tail block (the original instrument had one long side piece that went all around the instrument without any joint): 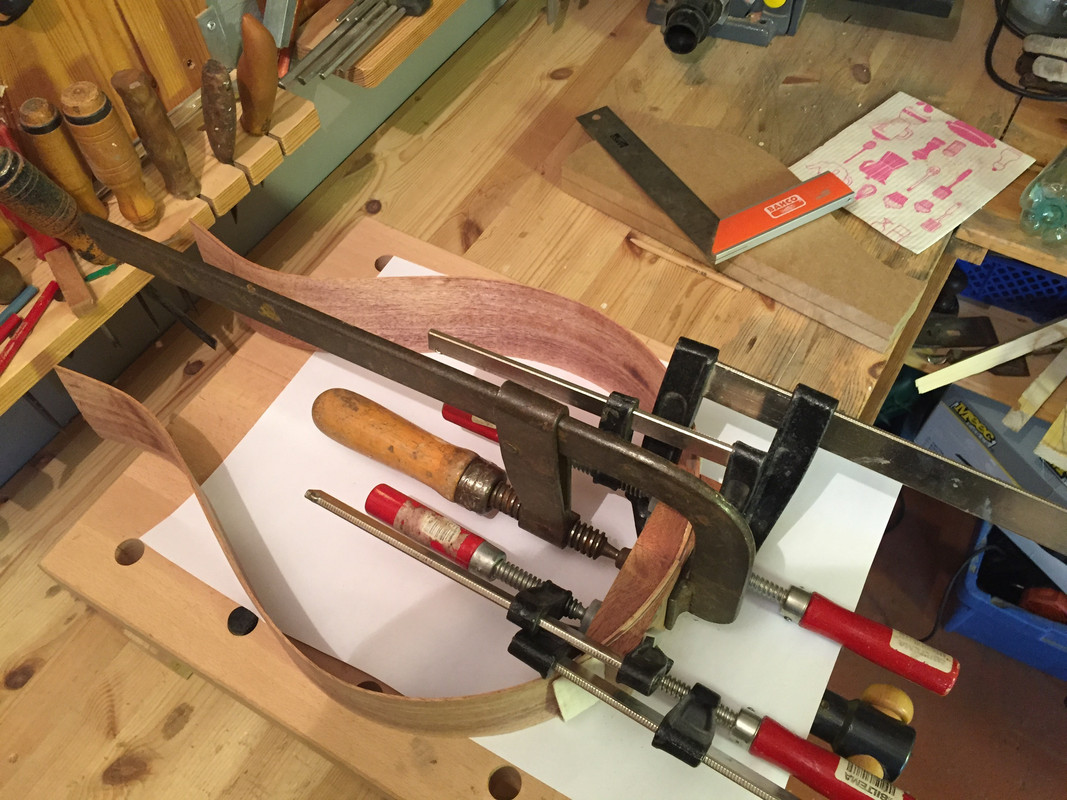 And then I glued the sides to the neck block and inserted the carbon fibre rods: 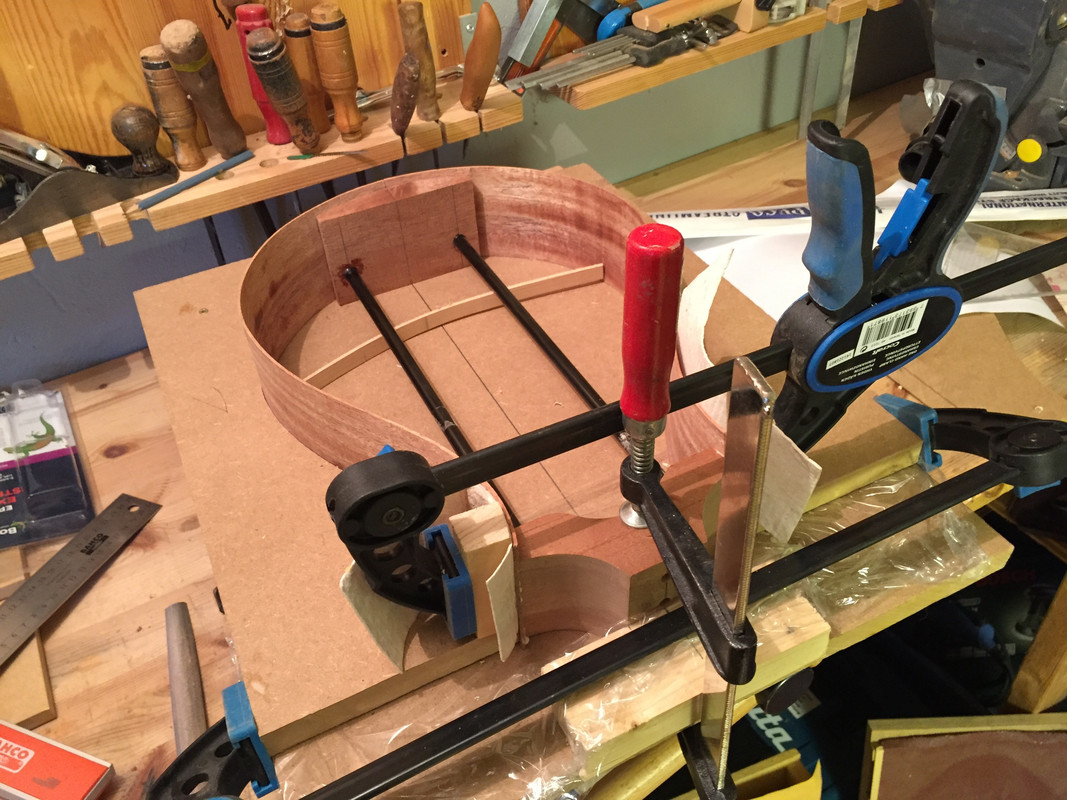 And that's all for now. I end with a mood image of some of the parts (I didn't bother to publish images of me planing the top, planing the back, planing and bending the sides, but obviously I've done all of that):   
|
|
ocarolan
Global Moderator
CURMUDGEONLY OLD GIT (leader - to join, just ask!)
Posts: 35,724
Mini-Profile Background: {"image":"","color":"c0cfe1"}
Mini-Profile Name Color: 182a3f
Mini-Profile Text Color: 733a1c
|
Post by ocarolan on Nov 12, 2017 22:17:23 GMT
Haven't seen one of these before - will follow with interest!
Keith
|
|
francis
C.O.G.
Posts: 2,483
My main instrument is: Whatever I'm building...
|
Post by francis on Nov 13, 2017 7:58:50 GMT
Haven't seen one of these before - will follow with interest! Keith Ditto
|
|
leoroberts
C.O.G.
Posts: 26,146
My main instrument is: probably needing new strings
|
Post by leoroberts on Nov 13, 2017 8:47:51 GMT
Looks like an interesting concept! It'll be really interesting to see how this build thread develops and, of course, what the resulting octofone both looks and sounds like. Best of luck, lars 
|
|
|
Post by lars on Nov 13, 2017 9:02:58 GMT
Thank you all! Octofone is apparently a registered trademark once again (search for octofone.com) so that's why I named my instrument an octochord instead. Noone can disagree that this will be an eight stringed instrument! I really hope it'll be an easier and more straight forward project than the double-s. I have never seen one of the few remaining instruments in real life. I guess that there are not many of them at our side of the pond. I stumbled upon a thread at Mimf.com were Mark Swanson described the making of his Octofone mkII and that was how I found out about the instrument. I fell in love with the looks...
|
|
|
Post by andy3sheds on Nov 13, 2017 9:53:43 GMT
Interesting stuff. Good luck with the build
|
|
|
Post by martinrowe on Nov 13, 2017 17:24:21 GMT
You probably know this but... If you tune a 10 string cittern GDAEB then this gives you an Octave Mandolin (GDAE) on the lower 4 strings. Capo on 5 and you get CGDAE: CGDA (Mandola) on the lower 4 strings and GDAE (Mandolin) on the top 4. (that's right isn't it?)
Three for the price of 1 - I like that.
Martin
|
|
|
Post by lars on Nov 13, 2017 18:03:59 GMT
You probably know this but... If you tune a 10 string cittern GDAEB then this gives you an Octave Mandolin (GDAE) on the lower 4 strings. Capo on 5 and you get CGDAE: CGDA (Mandola) on the lower 4 strings and GDAE (Mandolin) on the top 4. (that's right isn't it?) Three for the price of 1 - I like that. Martin Haha... I just thought this afternoon about a 10 string cittern tuned GDAEB as my next project. Because of the possibilites you mention. I like the idea because I can have many roles at a session or in a band without changing instruments for every song or tune. The only disadvantage is the compromise in body size. No matter what you choose, you will have too much bass or too much treble for one of these tunings. Earlier this summer/fall I made a tenor mandola with the intention to get a combined mandola/mandolin. It turned out to be a much better mandolin than a mandola, which didn't come as a surprise, since I based it on a mandolin body and the same scale length as my octave mandola. So watch out for a new build later this autumn, winter or spring: "10 string cittern - three instruments in one" :-)
|
|
|
Post by lars on Nov 15, 2017 20:25:05 GMT
Now the rim is finished. I first marked every milimeter of tapering in the mould and transfered it to the sides. I cut it roughly with knife and then sanded the rim flush against the sanding board: 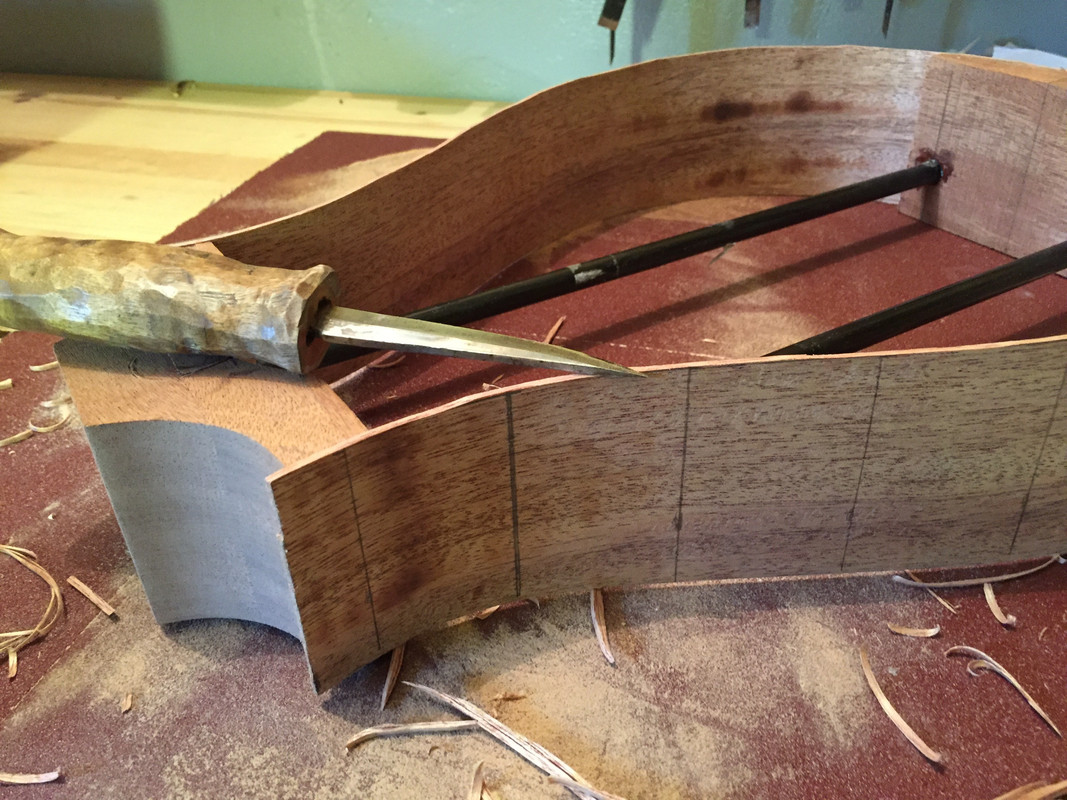 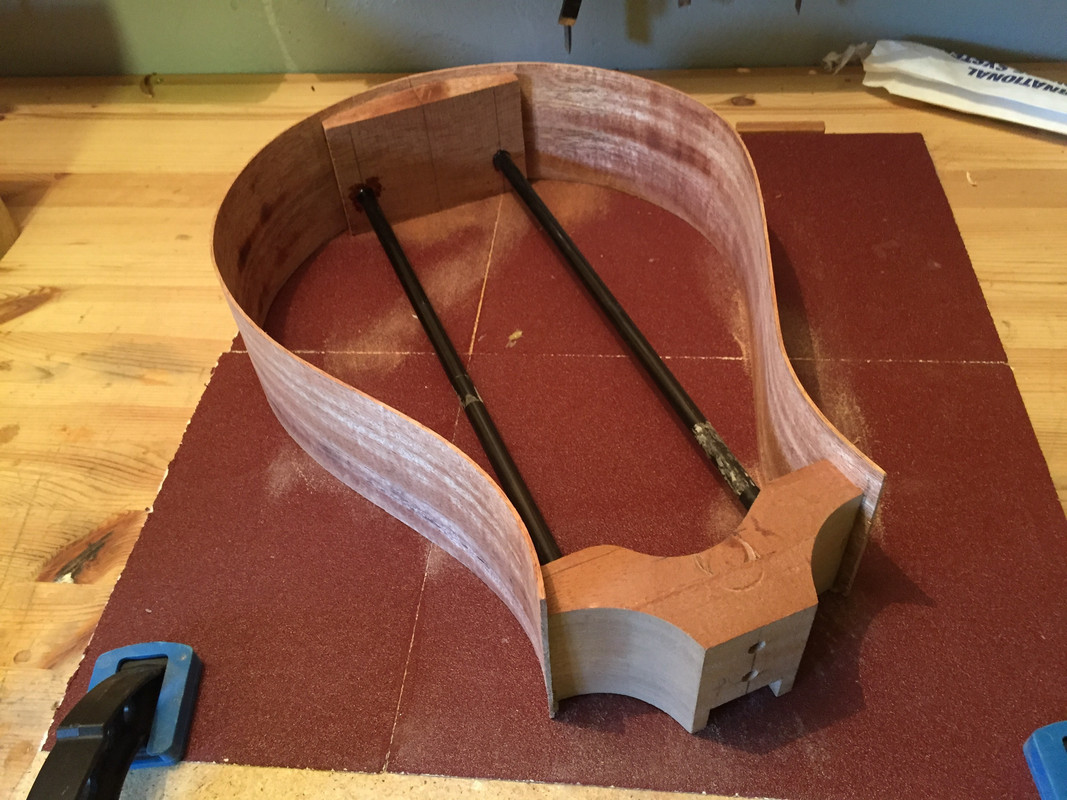 First I planned to use mahogany kerfed linings, but they broke when I tried to bend them. So I made solid linings which I bent on the hot pipe. The wood is Pine, but not any pine. It's an extremely well seasoned very old pine that I had saved for a soundboard - my first two instruments had soundboards from the same wood and I'd say it had properties like douglas fir tonewise. Anyhow that last piece of pine ended up as linings and not a soundboard: 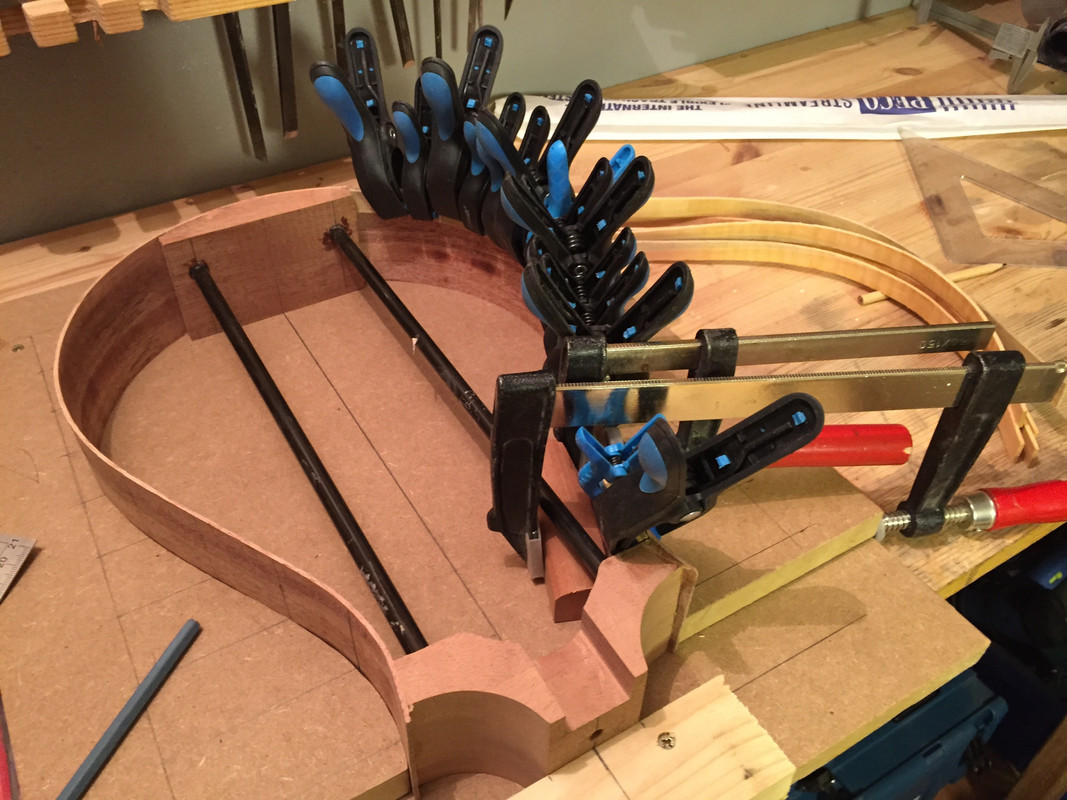 I complemented the linings with braces along the sides and the completed rim-set looks like this: 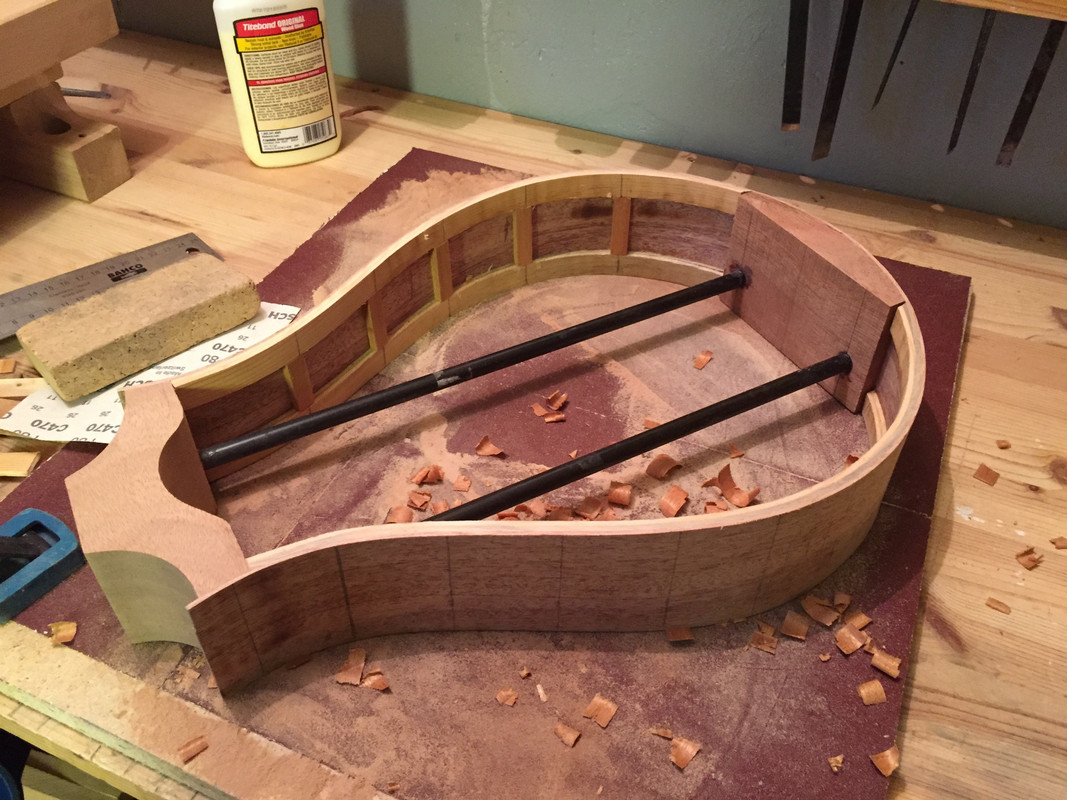 This is very stiff and sturdy construction, far from the light and fragile construction of the original octofone, but I'm pretty shure this is a better way of doing it.
|
|
|
Post by lars on Nov 28, 2017 17:43:29 GMT
The soundboard and back were just preliminary planed before gluing, so now it was time to hand plane them down to almost final thicknesses. In this case it was about 2.2 - 2.3 for the top and 2.8 for the back. I aim for the top to be slightly over 2 mm in the end. 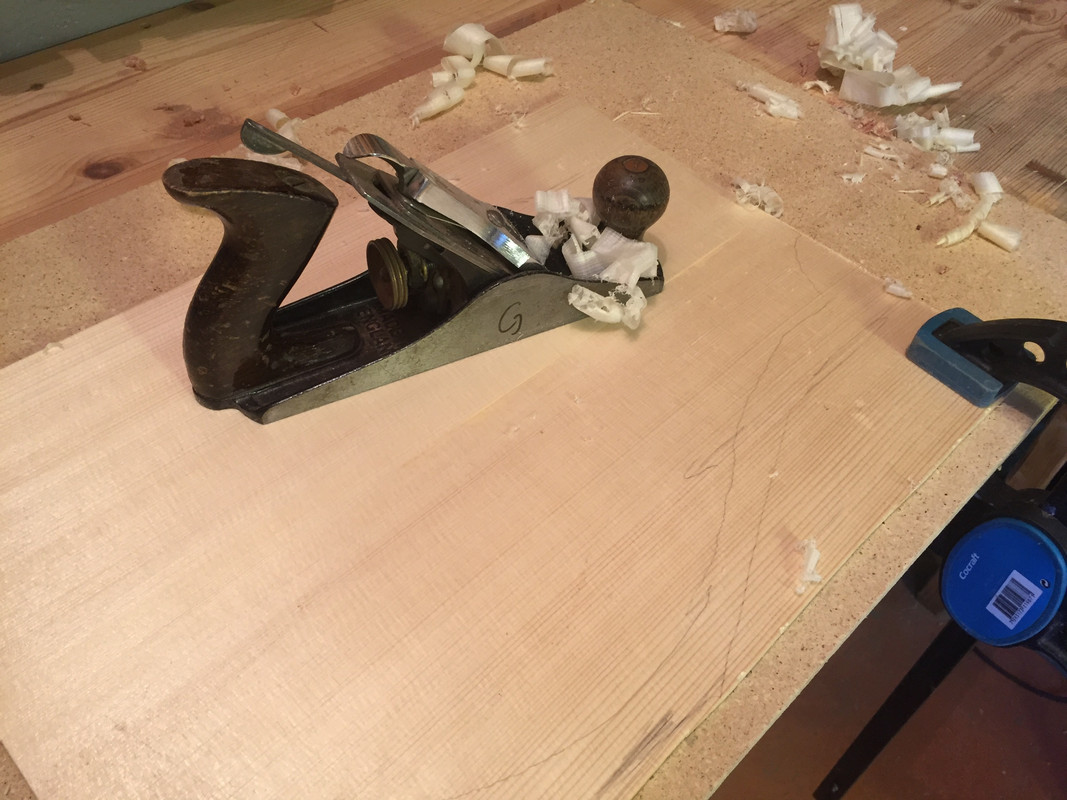 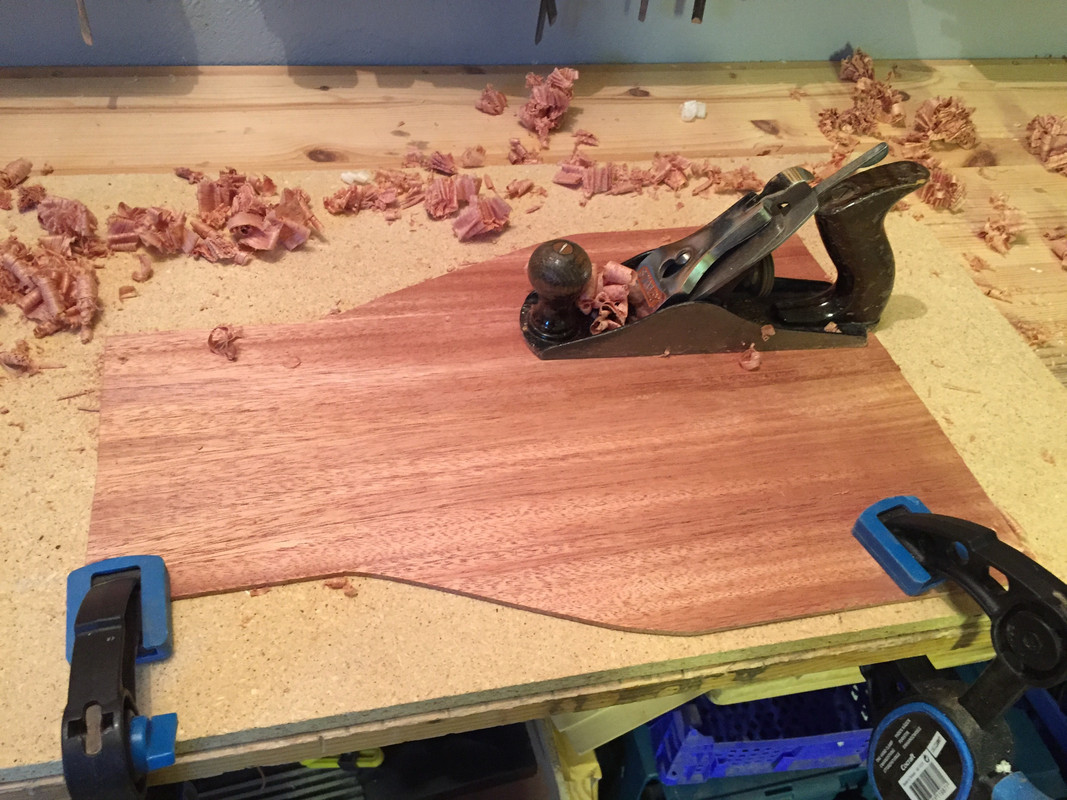 A mood image: 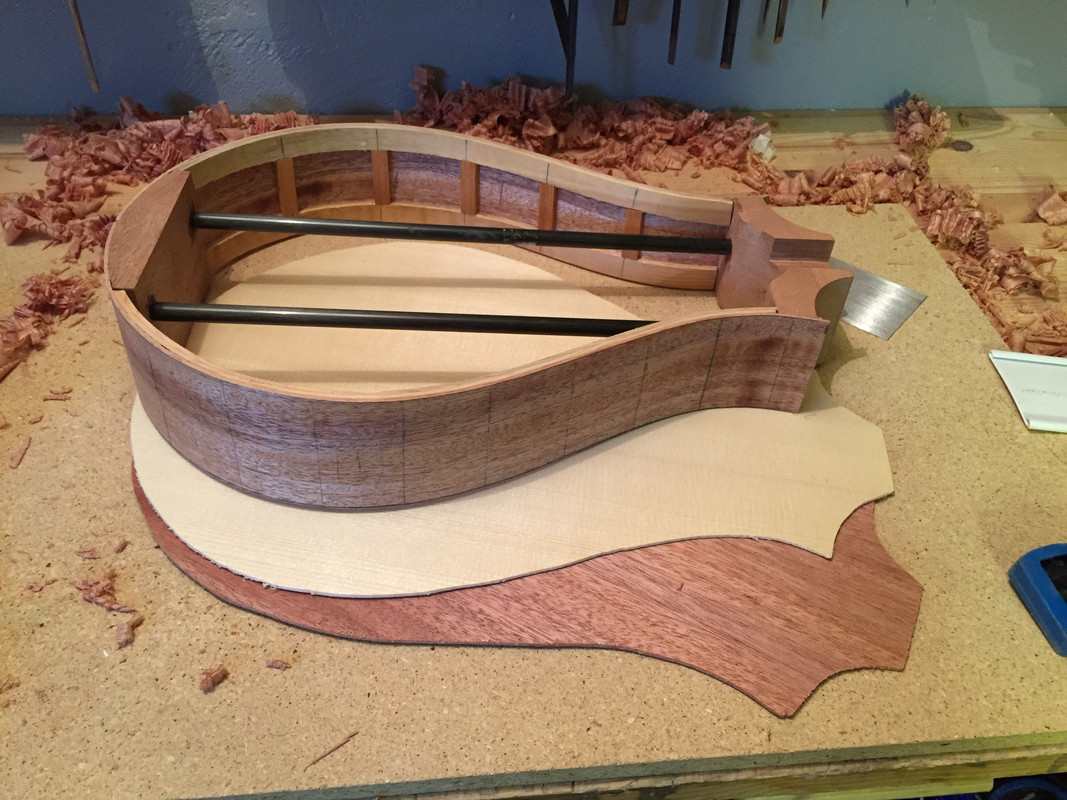 For the first time I've planned for a more "conventional" rosette, though rather minimalistic. My design philosophy is to make things neat but simple, but not to omit things that are structurally necessary or benificial. But first I had to make a circle cutter: ![]() 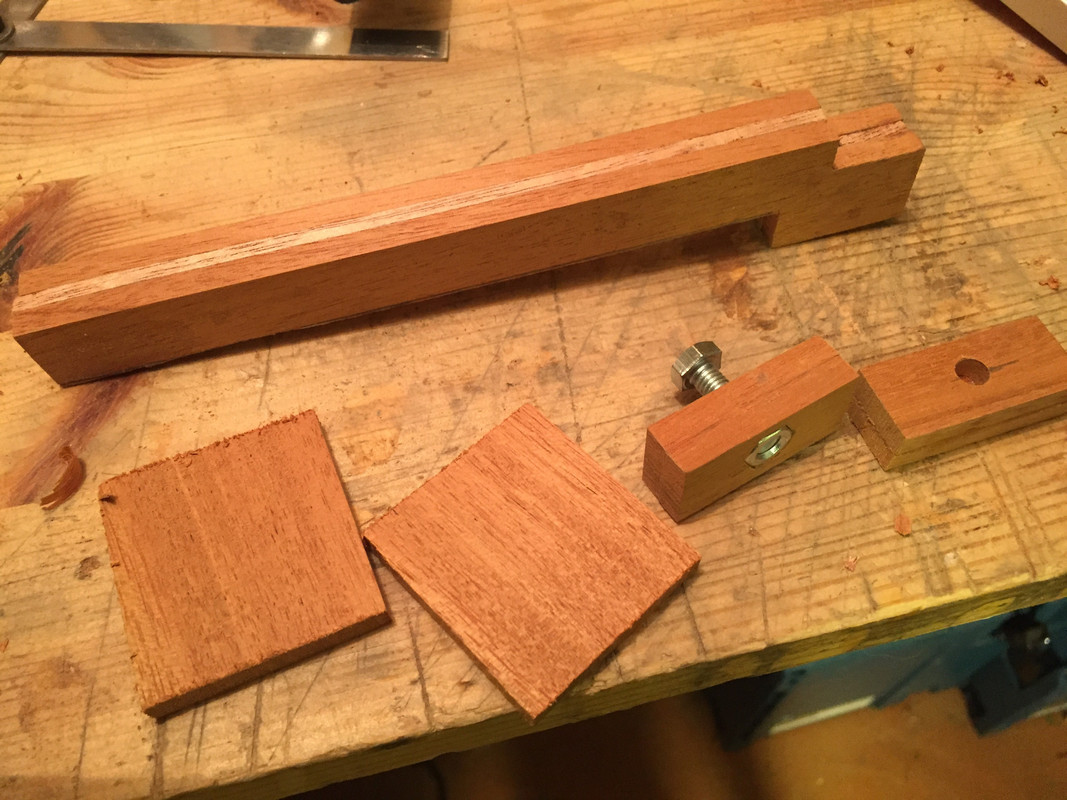 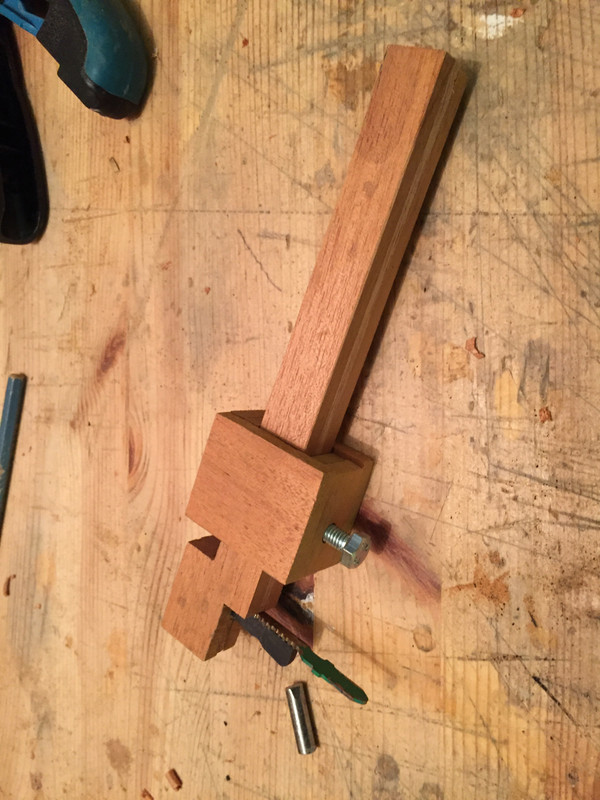 First I cut the rosette from the same mahogany piece as one of the sides. 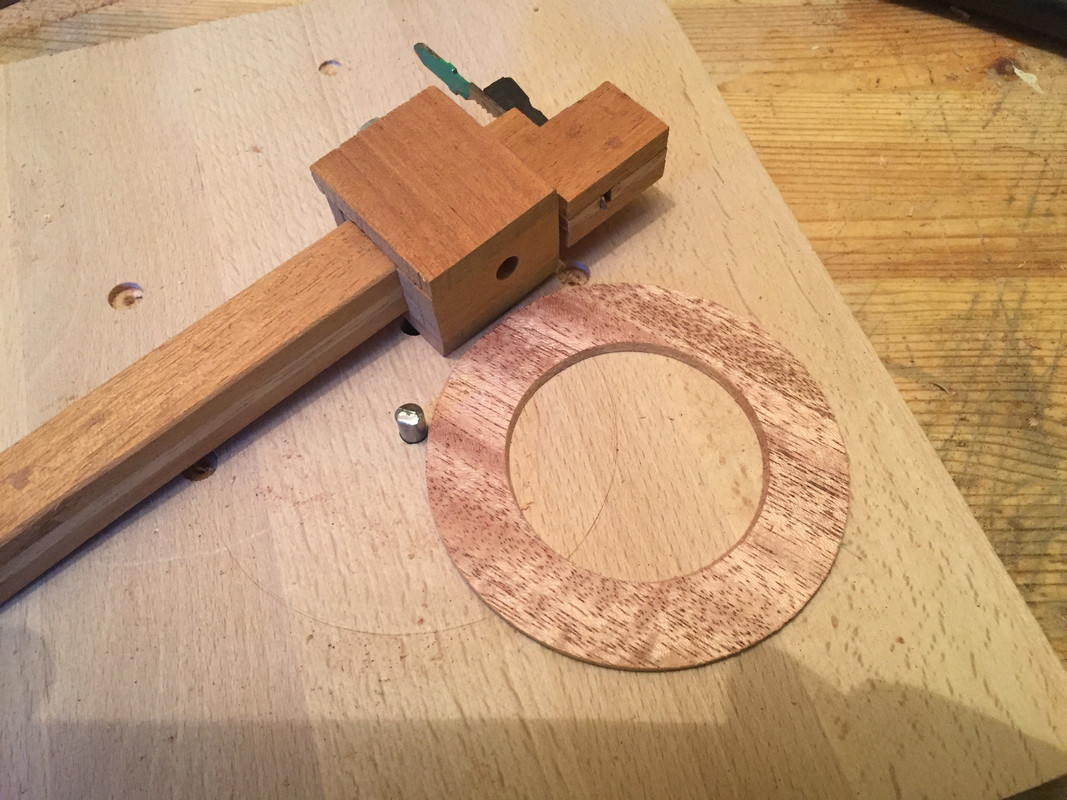 Then I used the cutter and chisels to make a channel for the rosette and glued it: 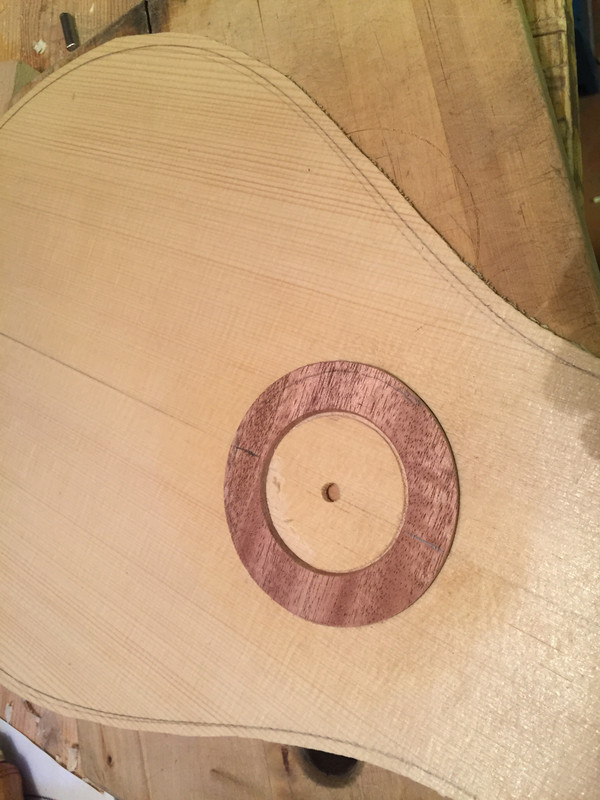 And planed it flush to the top:  And turned to top upside down and glued a thin piece of spruce cross grain to the top. As the rosette also is glued cross grain, it practically gives me a 3-ply to surround and support the sound hole. 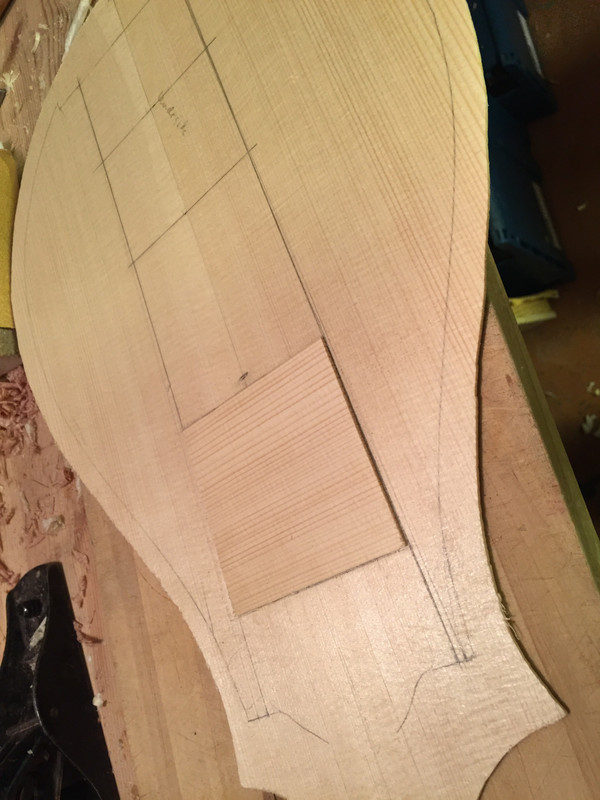 Then I used the cutter again and cut the soundhole: Last step was to add binding. I planned for ebony, but after three bindings that split when trying to bend them on the hotpipe, I decided for my trusty laburnum (which bent like a charm), glued it and cut/sanded flush to the rosette. 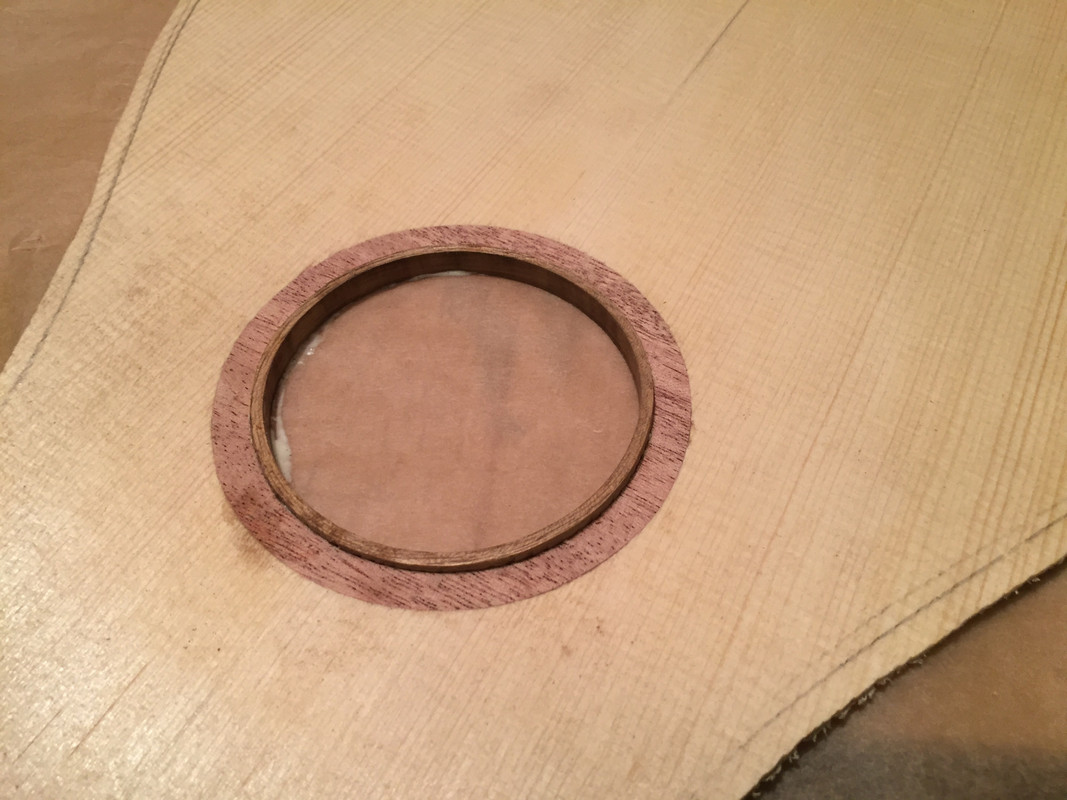 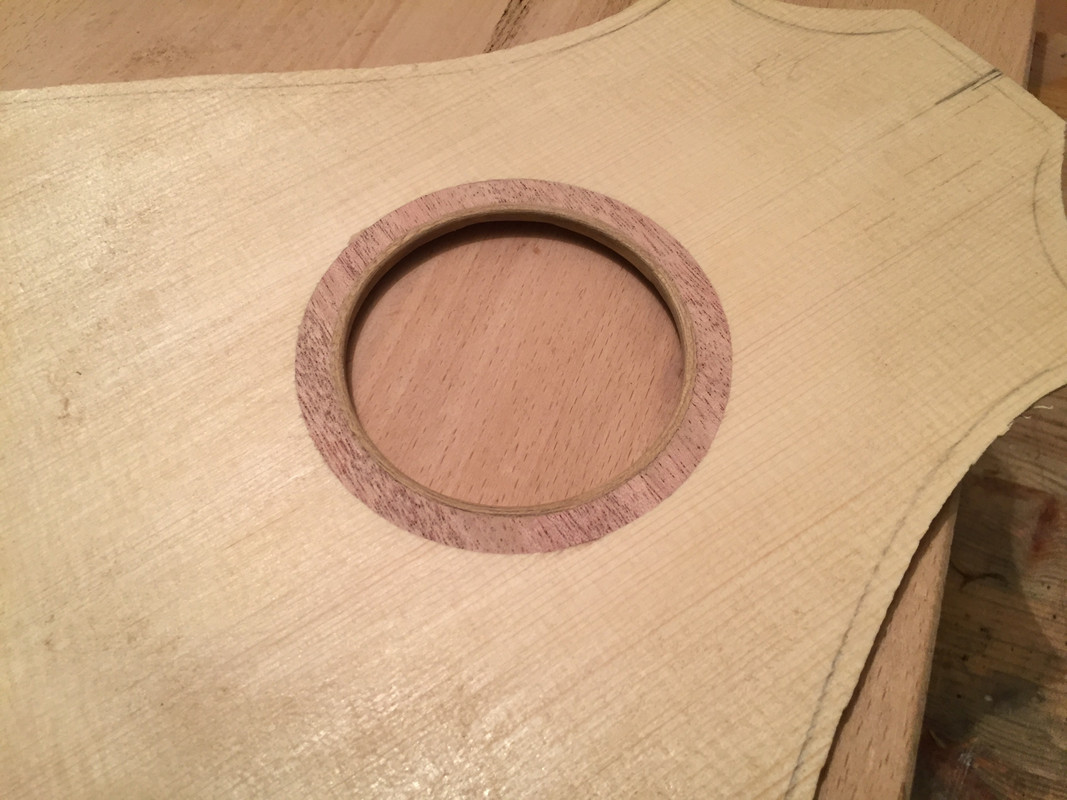 And it actually looks a bit better in real life. There are one or two minor flaws, but not very significantly. I'm quite content. Next post will be about the bracing of top and back.
|
|
|
Post by lars on Nov 28, 2017 19:14:18 GMT
Bracing top and back
Bracing the back was quite straight forward. Like the original octofone I made it ladder braced with four braces rather evenly spread out. I planned to make it absolutely flat (as I think the original was), but in the end I put a tiny arc in the braces. Here is the back with "voiced" braces and a cross-grain strip along the centerline. 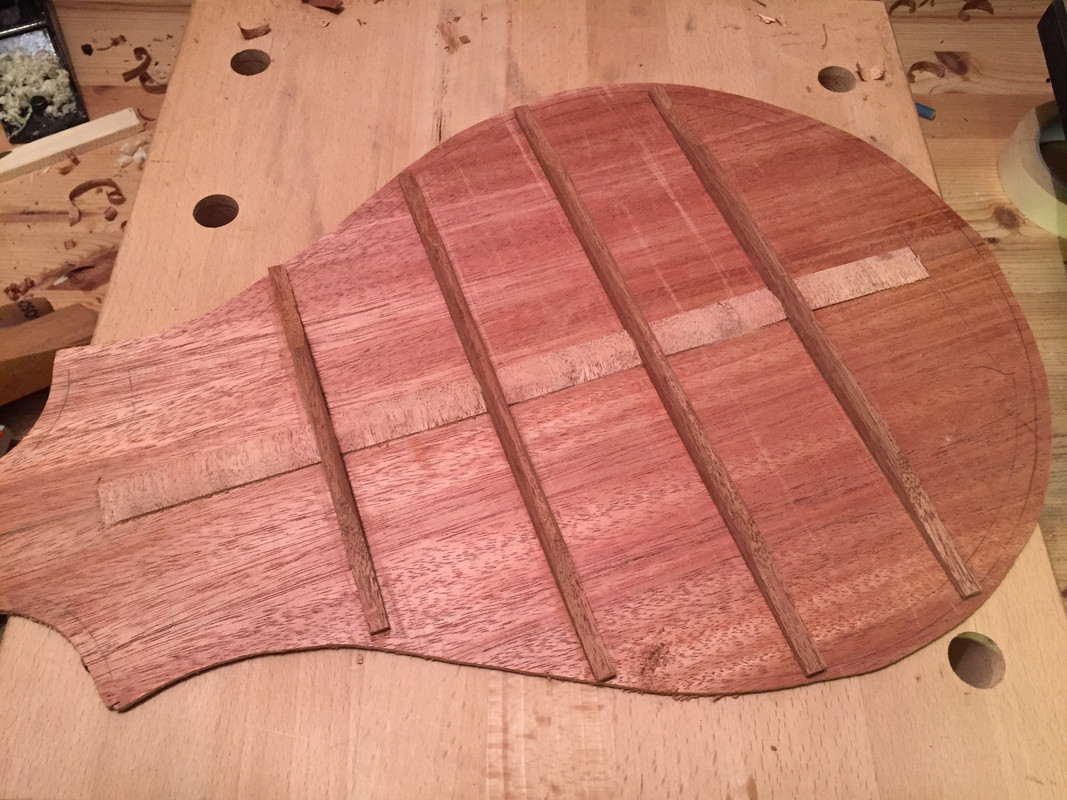 On the original instrument the top was ladder braced, but I've opted for a hybrid ladder-/H-bracing. Furthermore I've reinforced the central brace underneath the bridge with carbon fibre - it's laminated with a cf-strip in the middle. As the top will be "true flat" I hope these measurements will help keep it flat. But as I've never done an absolutely flat top instrument, and have never worked with cf-inforced braces, I'm a bit nervous. I want the top to stay flat - I don't want the top to be too stiff. How do I find the balance? (A swedish saying is that it's like choosing between pestilence and cholera.) Here are some pictures from the work with bracing the top: 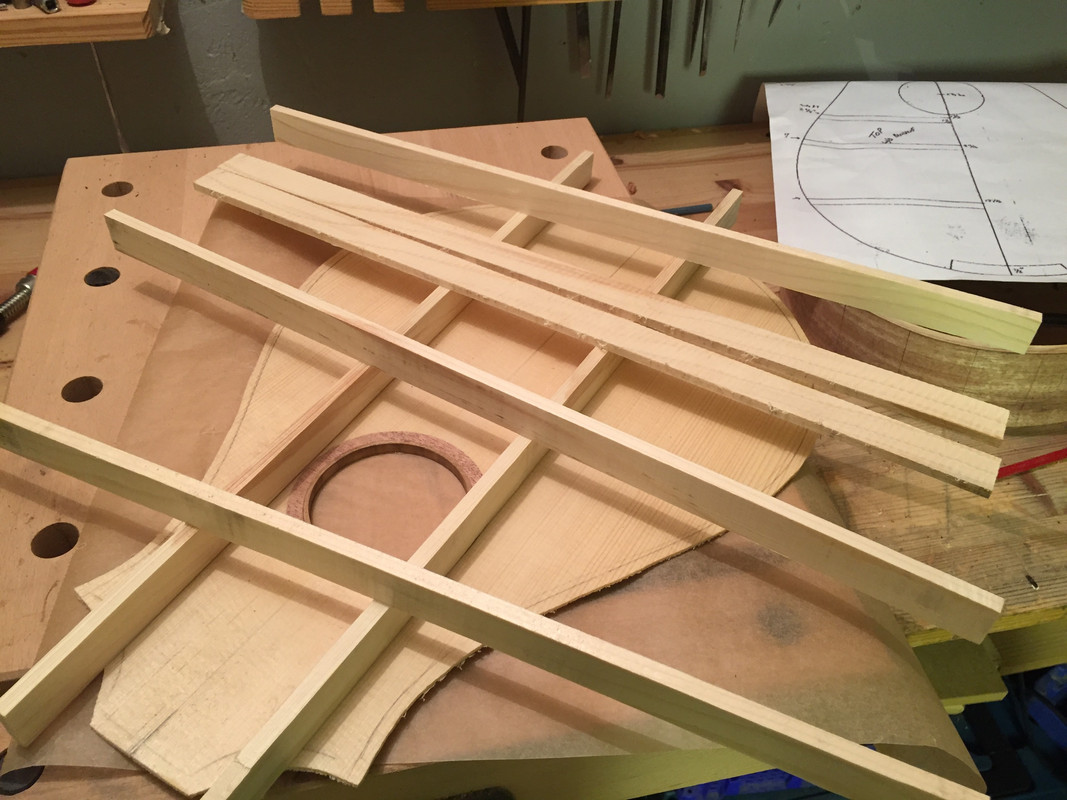 The braces cut. 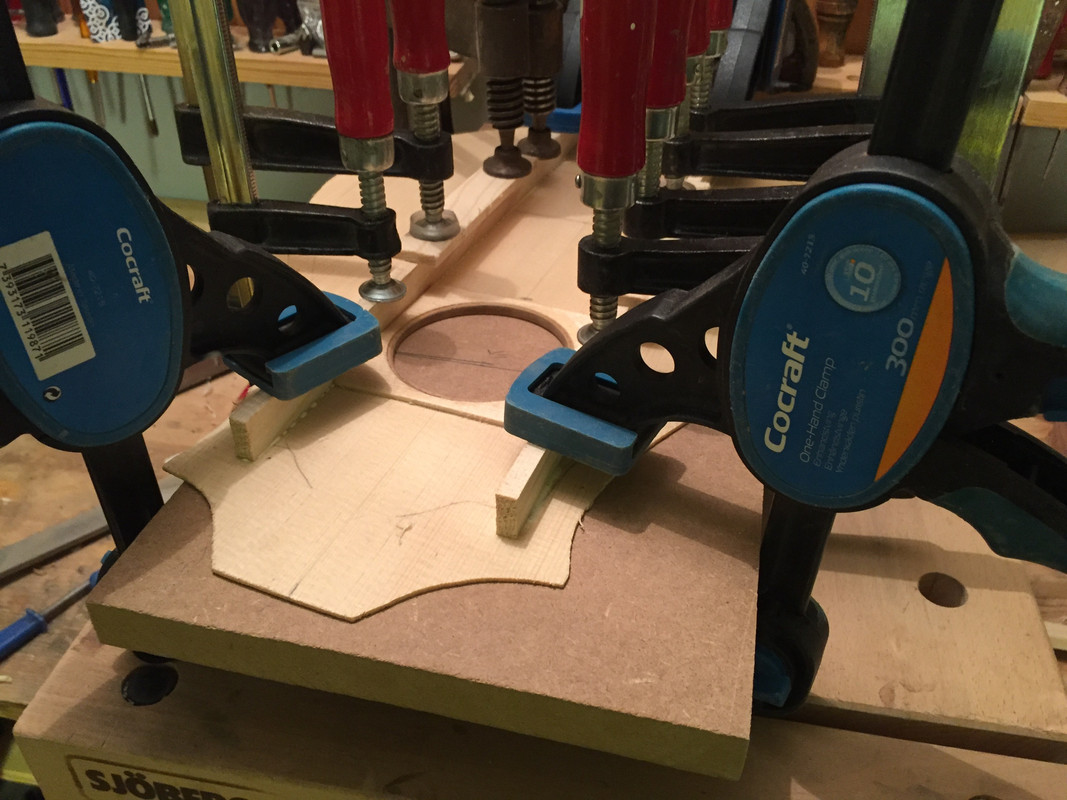 H-braces glued to the top 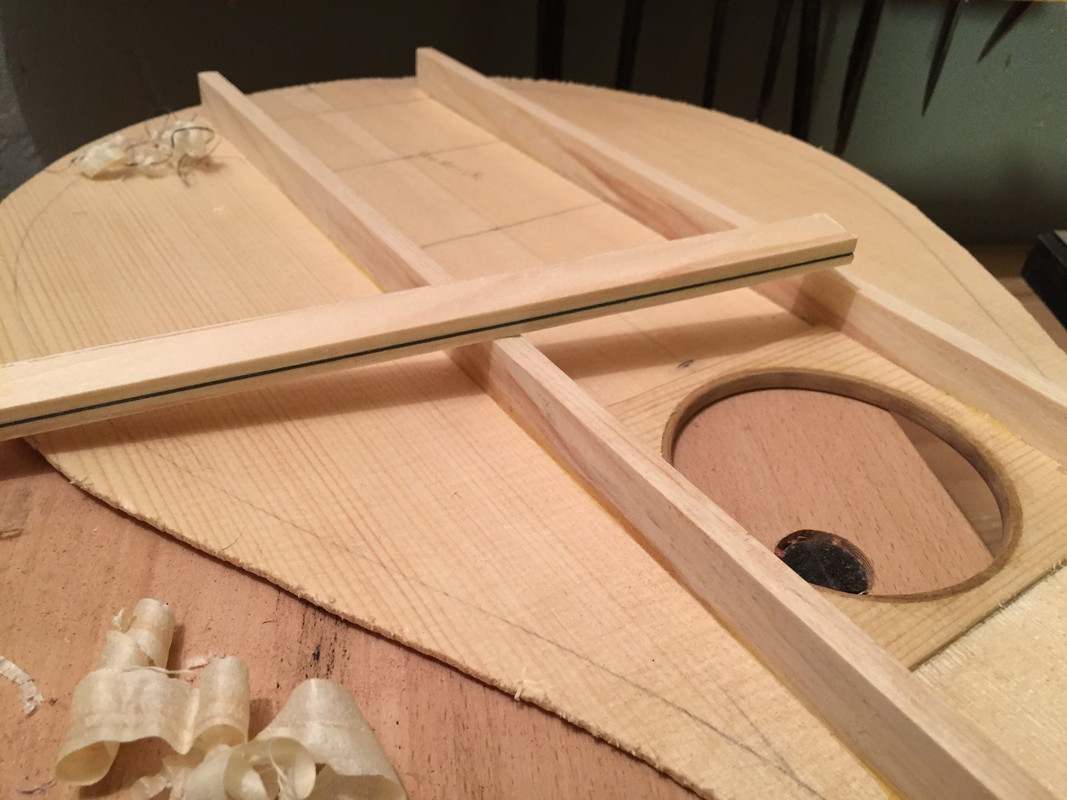 The main ladder brace laminated and ready to have notches cut 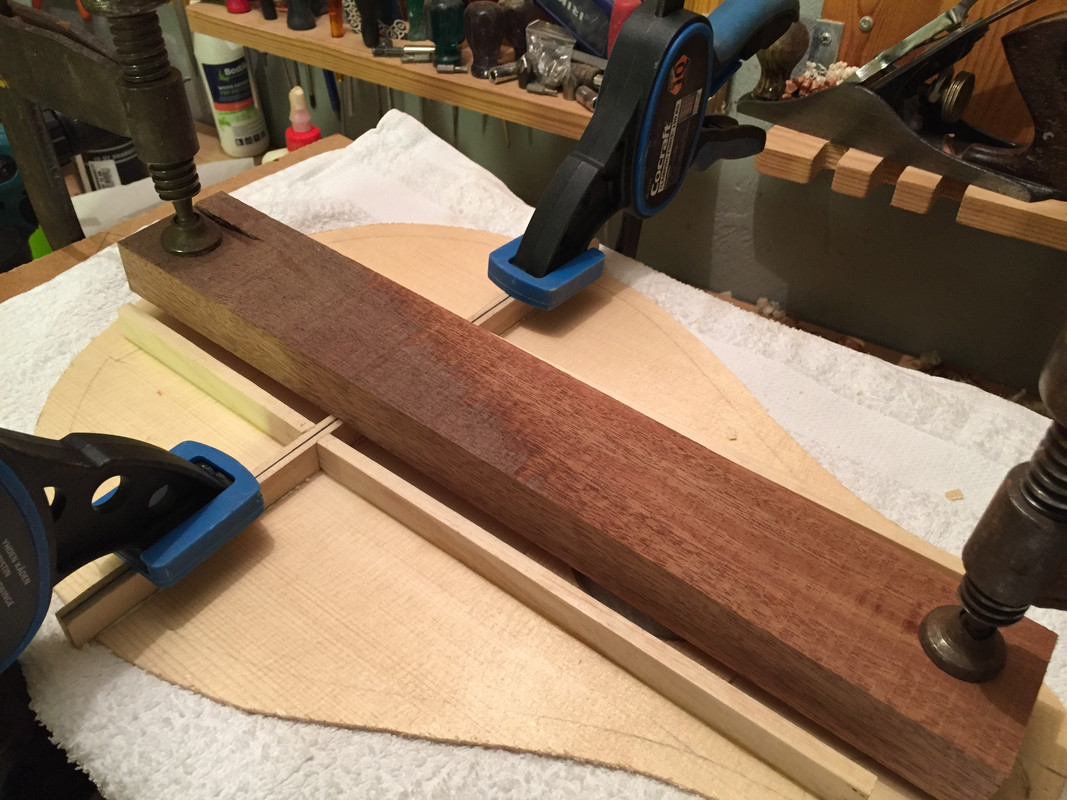 Which is glued here  And looks like this. ![]() 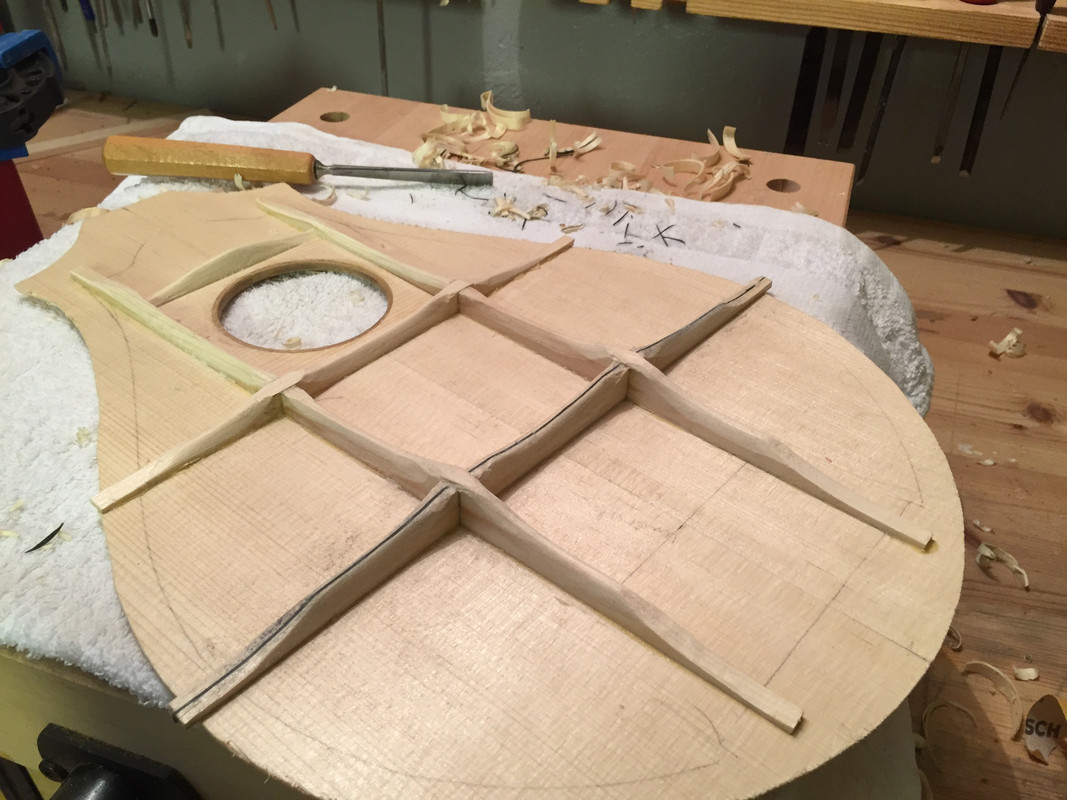 Apparently I forgot to document a lot of steps, but this is the near end result. And then I took a late decision to make a sound port (contrary to the original design): 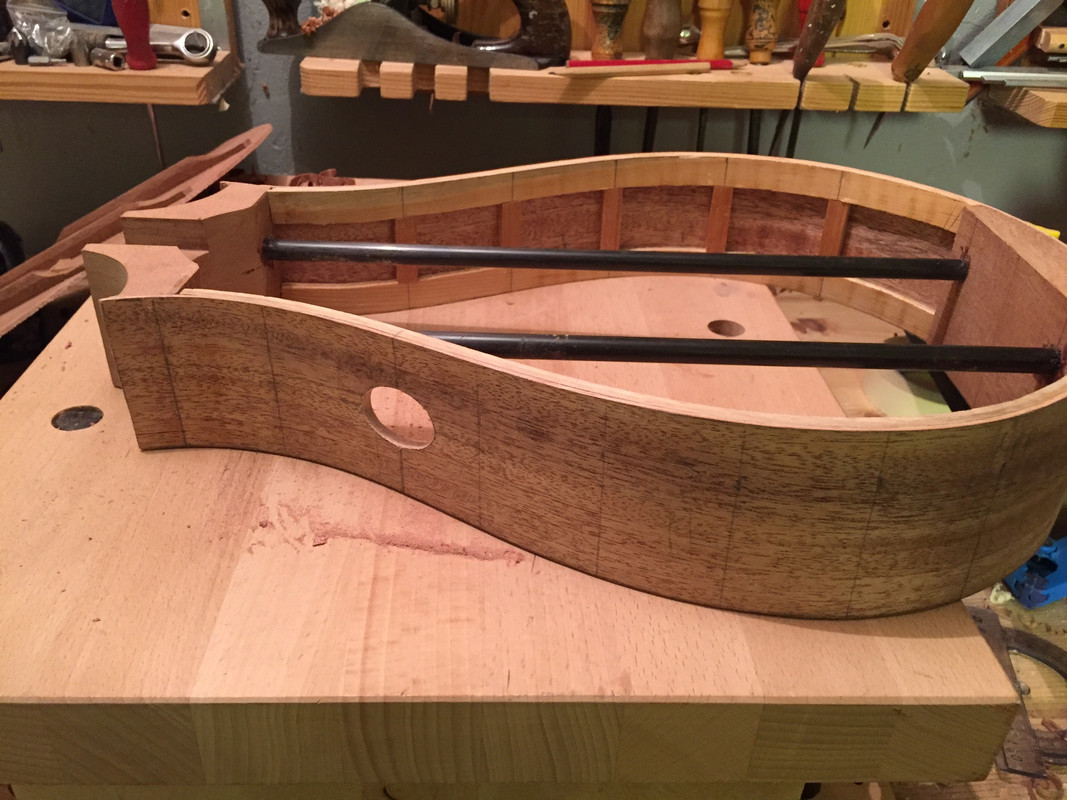
|
|
francis
C.O.G.
Posts: 2,483
My main instrument is: Whatever I'm building...
|
Post by francis on Nov 28, 2017 20:13:21 GMT
This is superb. Can't wait for the next installment 
|
|
davewhite
Luthier / Guitar Maker
Luthier
Aemulor et ambitiosior
Posts: 3,548
|
Post by davewhite on Nov 29, 2017 8:23:49 GMT
Lars, Nice rosette and even more satisfying for you having made the circle cutter - kudos  How did your chisel get on with carving the carbon fibre?
|
|
|
Post by lars on Nov 29, 2017 17:17:42 GMT
Lars, Nice rosette and even more satisfying for you having made the circle cutter - kudos  How did your chisel get on with carving the carbon fibre? Thank you Dave! I was a bit worried that the cf would harm the chisel so I chose one that wasn't so valuable and already a bit dull. But it was much easier to cut than I thought it would be and I guess the chisel got duller, but honestly I didn't notice. What I did notice was that the brace was so much stiffer than a solid wood one.
|
|
|
Post by lars on Dec 10, 2017 21:22:31 GMT
Here's an update. At the same time I did the last details on the Double-S mandolin, I also closed the body of the octofone. Before gluing the top and back I put on a back strip of laburnum. I had planned to make bindings and decorations of ebony, but when it failed at the rosette I decided to stay with laburnum for another instrument. It's a bit pale and bland, but the contrast will increase after a finish is applied. 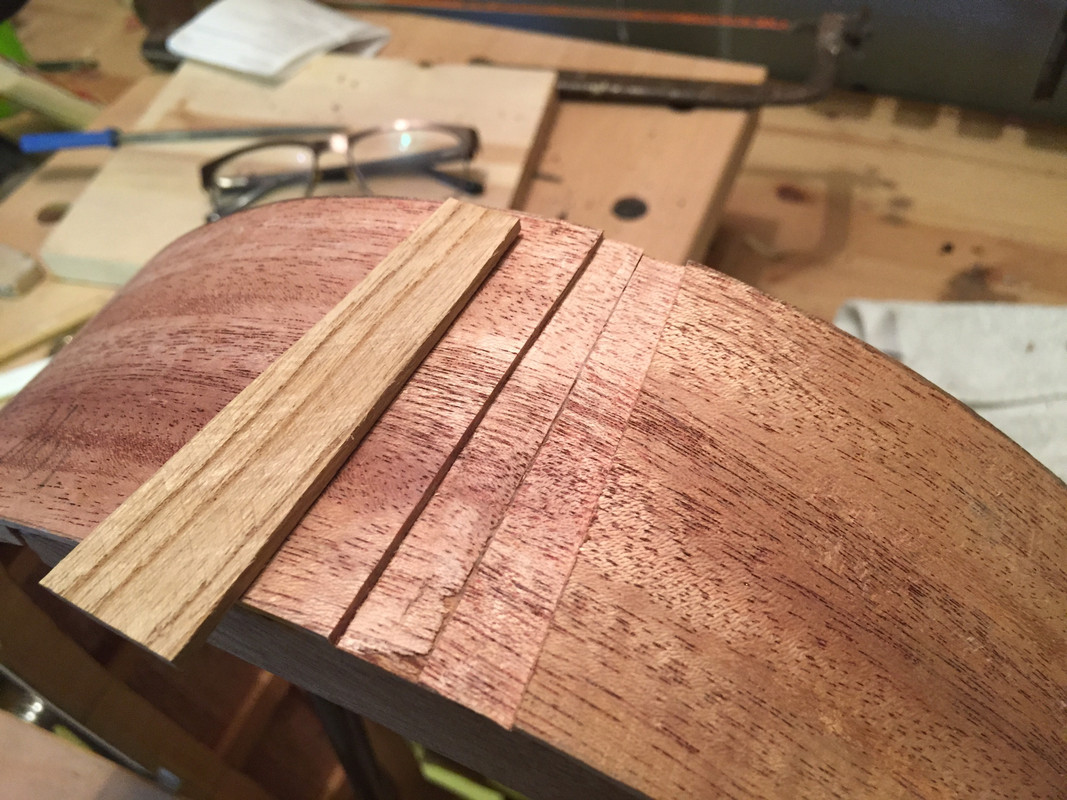 I forgot to take a picture of the result. But I glued the top - as usual using every assorted clamp in my store: 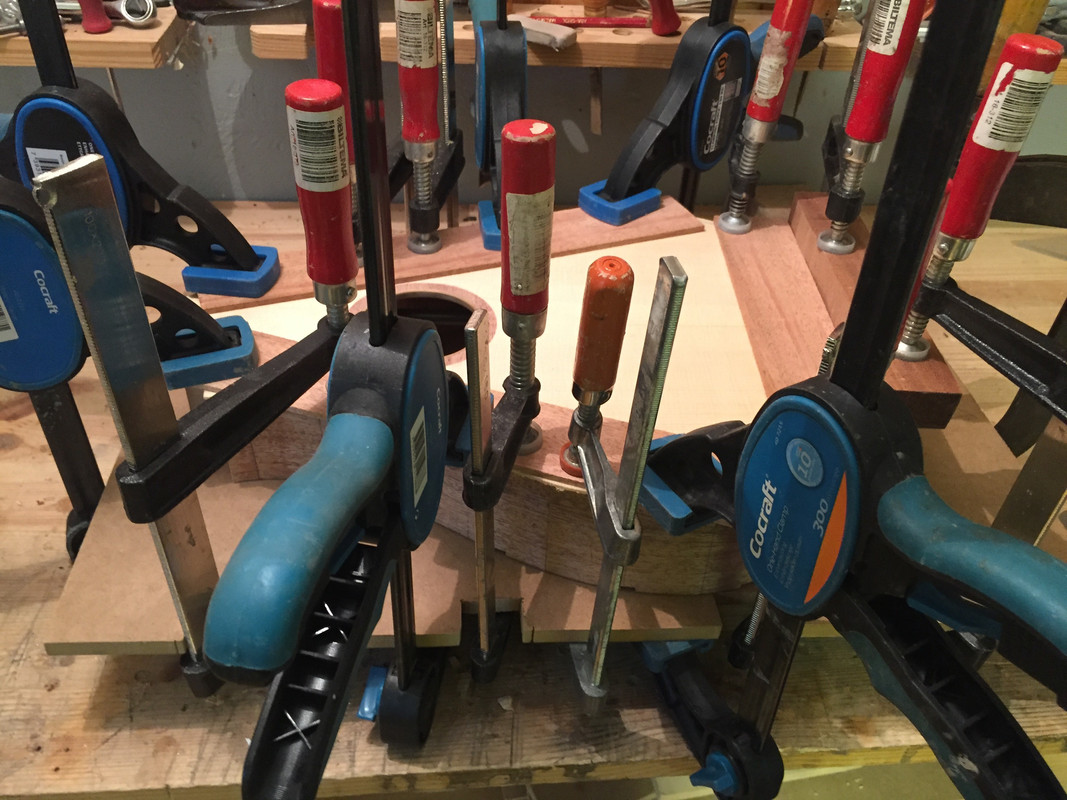 And before trimming the edges it looked like this: 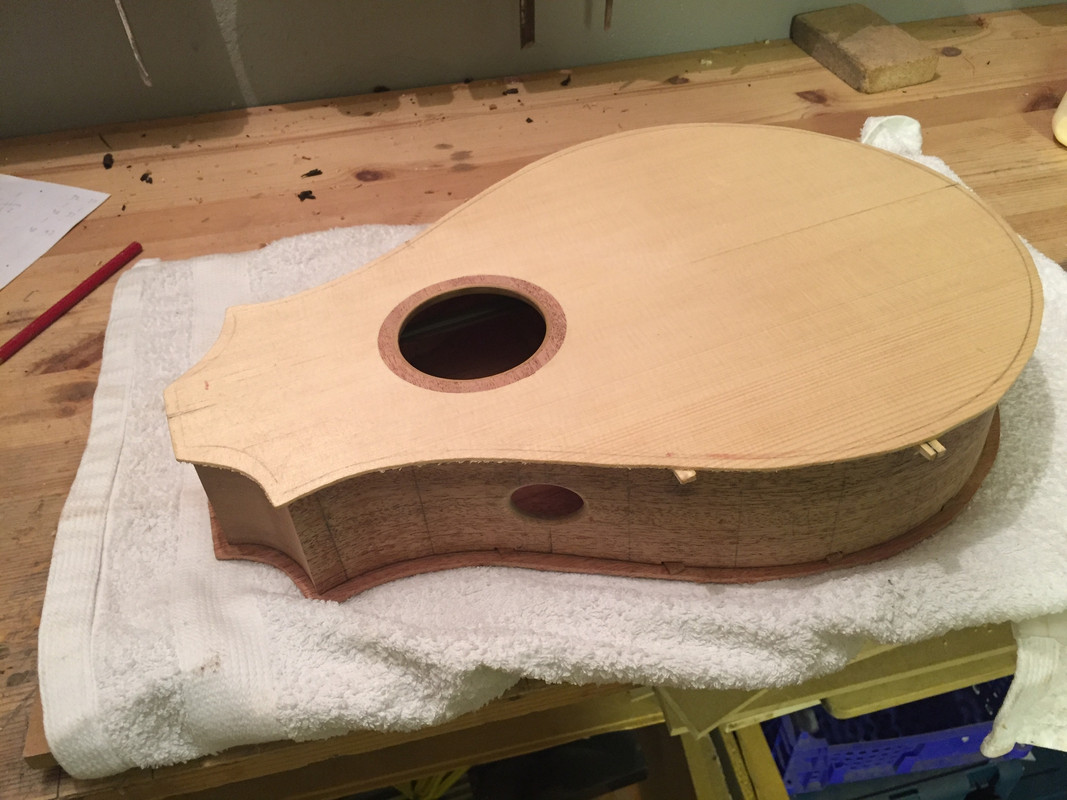 I trimmed the edges with knife, chisels and sand paper. And then it was time to inaugurate my new laminate trimmer to do the binding channels. As this instrument is true flat on both sides I don't need to care about a complicated jig. I just used the trimming jig that followed with the router. I was quite nervous, but it worked out well: 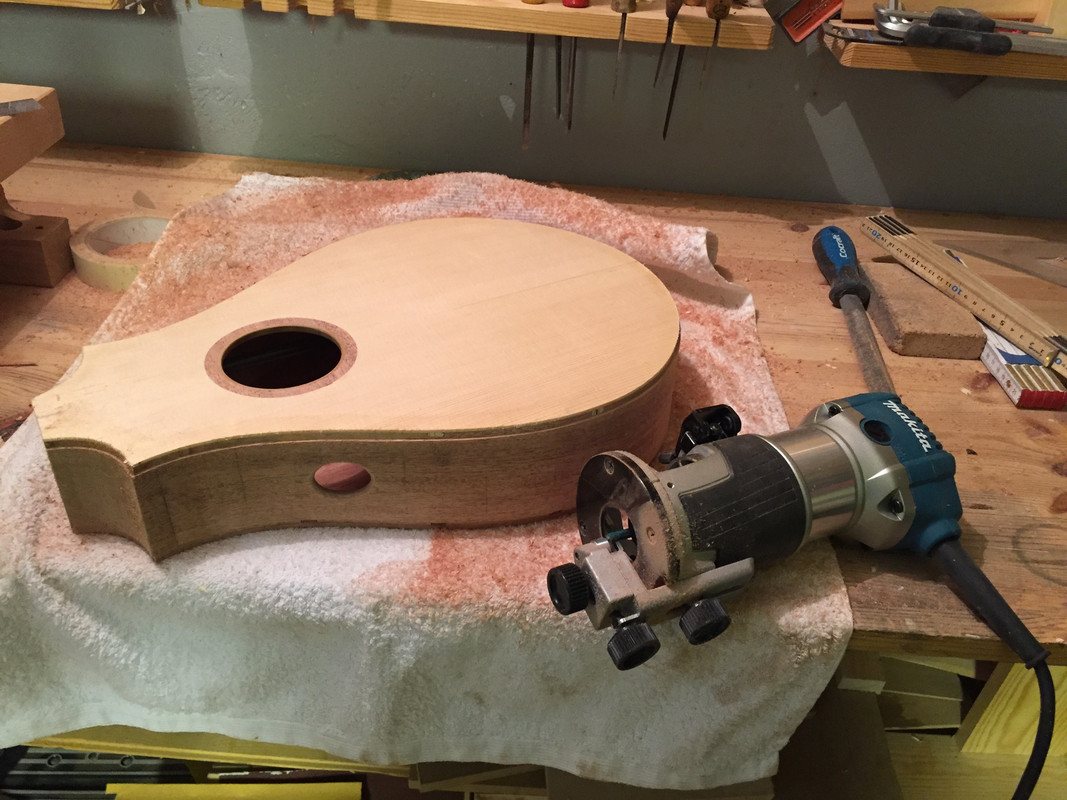 I bent the bindings without taking any pictures. First I glued on the small bindings at the "cutaways": 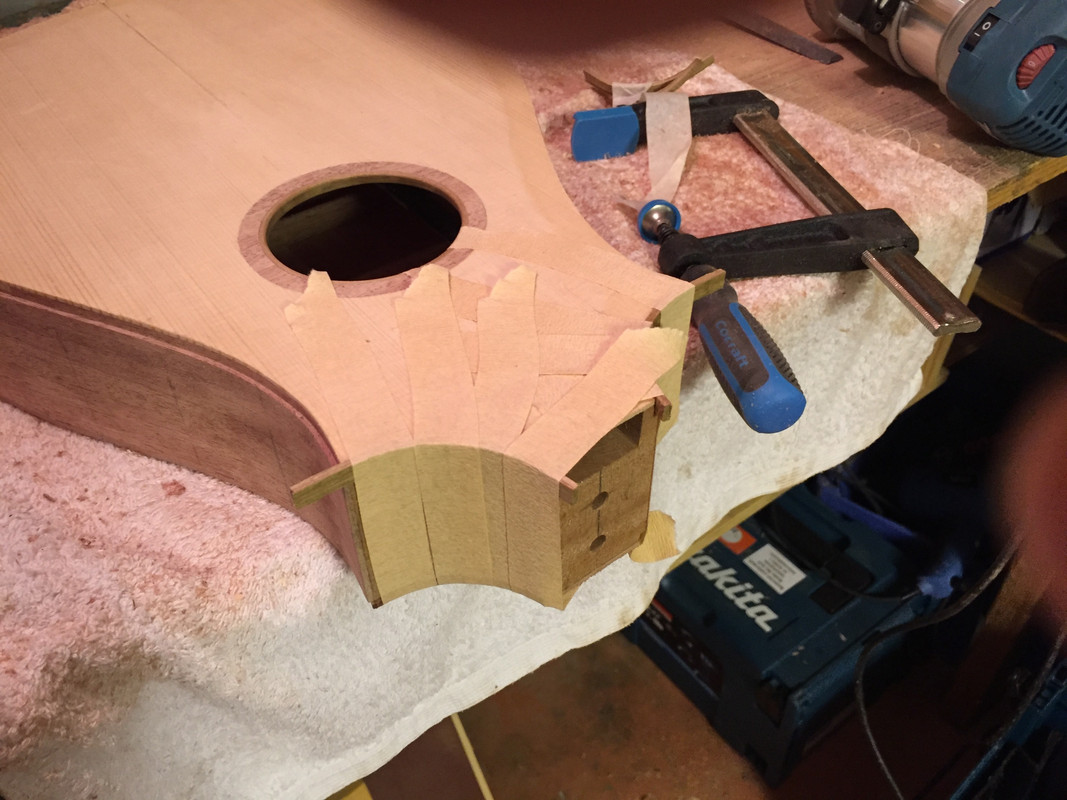 And now I've been gluing the rest of the bindings: 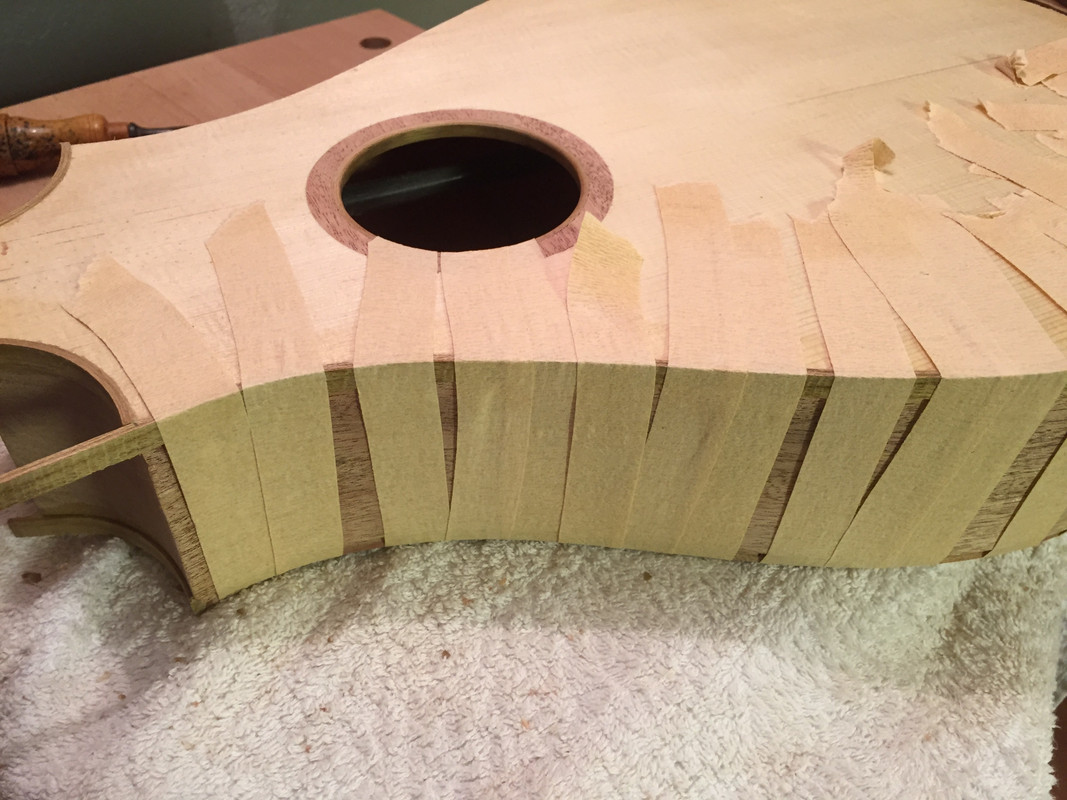 Meanwhile I've started to work on the neck. This time I decided to make the neck to almost finished width from the start. The neck/body width will be 44 mm so I planed and thicknessed the neck piece to 20*48 from the start. After that I cut the neck at 15° and planed the surface: 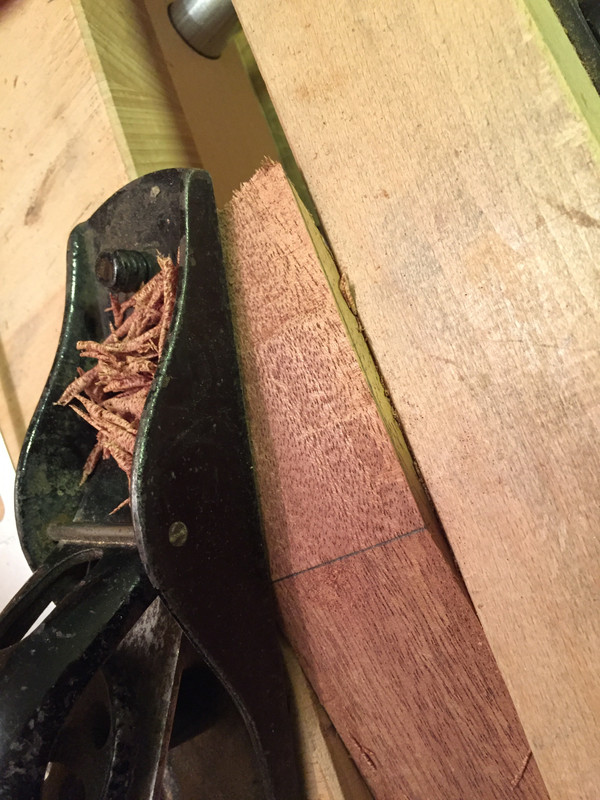 And glued the pieces together so that the headstock would get a 15° angle to the neck (I "know" that I took pictures, but there are none in the camera). Time for the laminate trimmer to be used again. This time for routing the trussrod channel. For the first time I'll use a factory made one. I've always done them myself before. 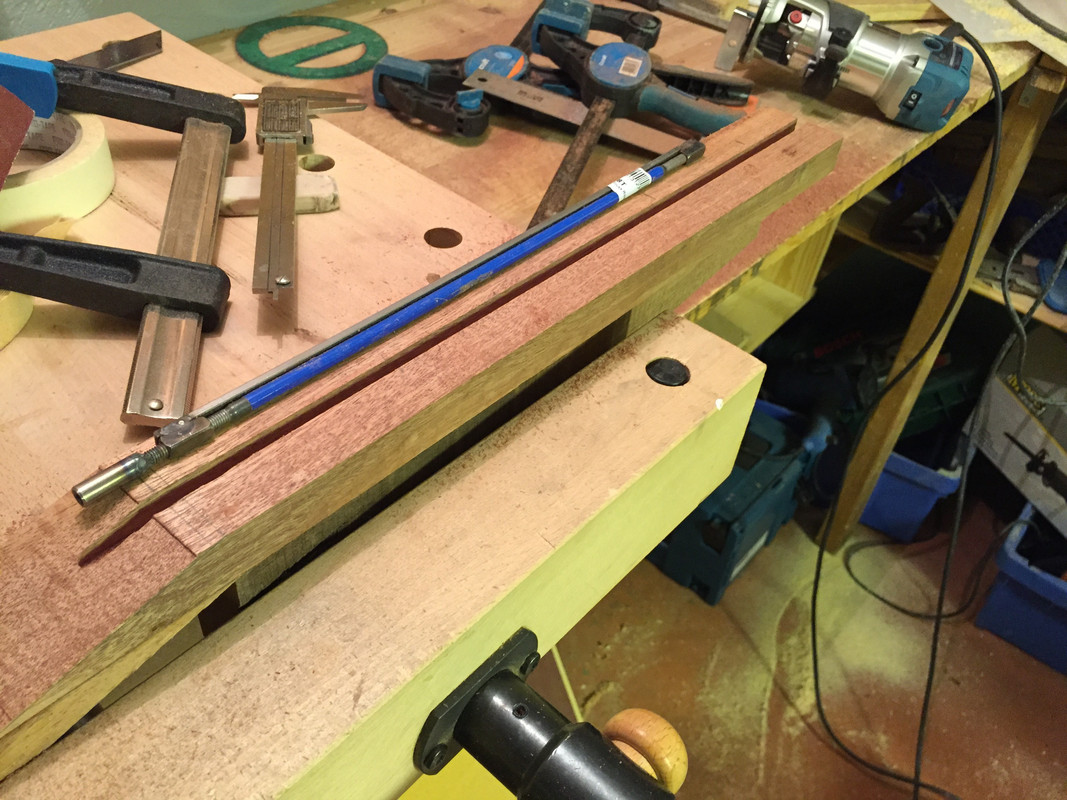 And after that I hand planed the other 15° surface to get a plane top surface for the head. 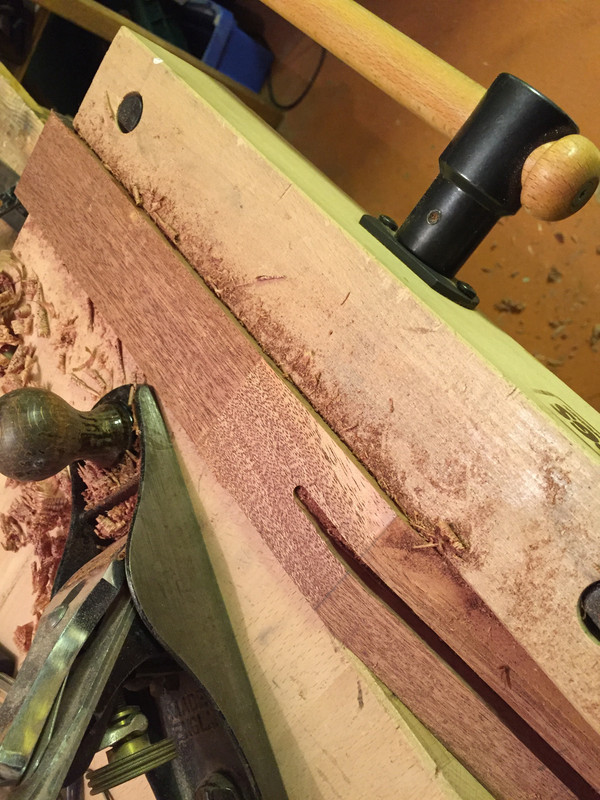 I glued the heel from three pieces, cut and sanded one side to 89° to set the neck/body angle. And then I glued the heel to the neck: 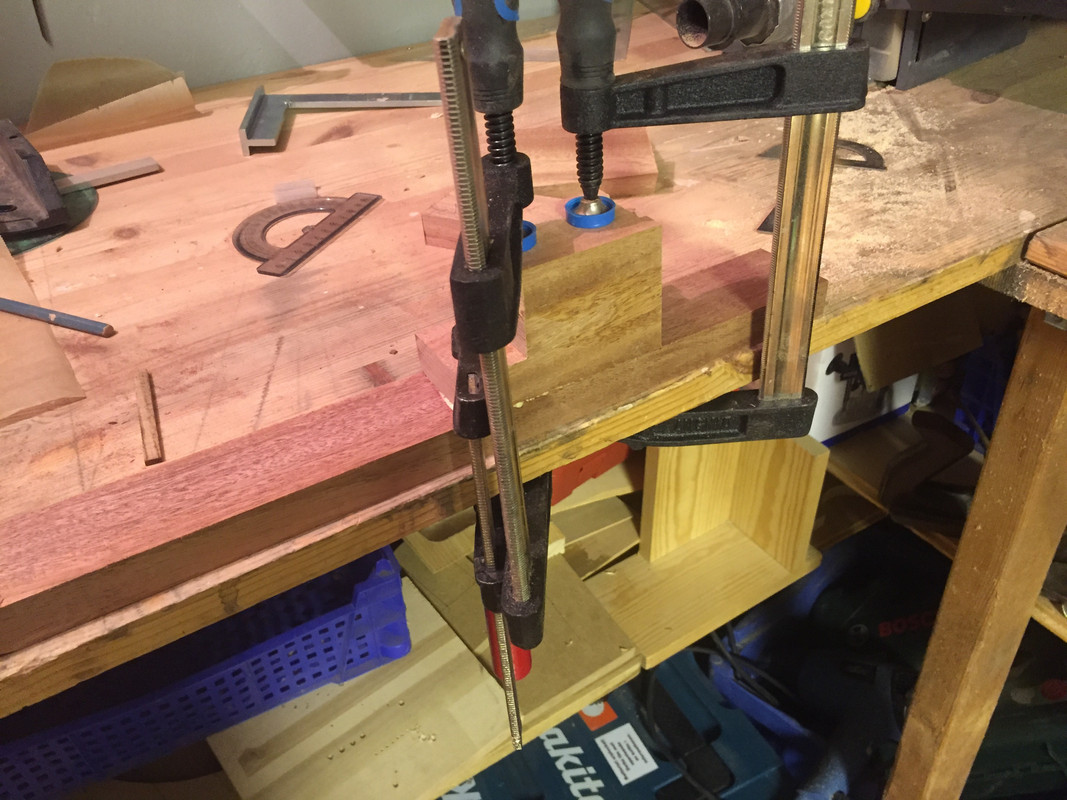 And that's where I am in the work process right now. All bindings are glued and awaiting to be trimmed and after that the body will be finished.
|
|