francis
C.O.G.
Posts: 2,475
My main instrument is: Whatever I'm building...
|
Post by francis on Aug 4, 2018 15:42:45 GMT
Superb craftsmanship Gary and simple clean lines - magic 
|
|
|
Post by bleatoid on Aug 4, 2018 22:54:32 GMT
I just marvel at these build threads from all of you luthiers - the quality of your craft is astonishing, the artefacts you produce, quite beautiful.
For those of you interested in such things, look out for my own forthcoming build thread "how I assembled my IKEA Billy bookcase and then re-assembled it with screws after it fell apart when I forgot to put the back panel thingy in".
Peter
|
|
foz
Strummer

Posts: 20
|
Post by foz on Aug 21, 2018 11:37:55 GMT
Gary,
I have just seen your latest video on YouTube regarding setting the neck;it has provided me with a little encouragement when you state that in your early years it could have taken you days to get the neck angle correct. I am battling those frustrations on my first build at the moment, a 00.
Can i ask regarding your use of epoxy to glue; i certainly can understand the benefits of not swelling the joint compared with titebond, but how easy is it to debond epoxy in the future, if ever needed?
Many thanks in advance
Andy
|
|
garynava
Luthier / Guitar Maker
Posts: 460
My main instrument is: Stanley No.5
|
Post by garynava on Aug 21, 2018 15:14:28 GMT
Gary, I have just seen your latest video on YouTube regarding setting the neck;it has provided me with a little encouragement when you state that in your early years it could have taken you days to get the neck angle correct. I am battling those frustrations on my first build at the moment, a 00. Can i ask regarding your use of epoxy to glue; i certainly can understand the benefits of not swelling the joint compared with titebond, but how easy is it to debond epoxy in the future, if ever needed? Many thanks in advance Andy Hello Andy ( foz) Glad that you found the video encouraging. I’m publishing part two later today and I’ll then share them here. What you’ll see in part two is that the neck should never move and therefore never need resetting- so no worries using epoxy. Epoxy can be broken down with heat, but I doubt whether you could heat the joint itself to a sufficient temperature without causing damage to the surrounding areas. I’ve never had to re-set a neck on any of my instruments and to be frank, if there was such a problem, I’d probably saw it off and make a new neck. If this is your first build I’d concentrate on building the best instrument you can and not worry about any future problems at this stage. Hope that helps. Cheers Gary
|
|
foz
Strummer

Posts: 20
|
Post by foz on Aug 22, 2018 7:26:12 GMT
Hi Gary, looking forward to part 2 later today.
Thanks for your insight on epoxy and aiming to make the best you can for your first. I have already set the neck once, but had to remove it as the angle was incorrect. I used titebond and a little thankful for it really as i managed to break the glue down without too much trouble to get it off.
I'll certainly have epoxy in mind for the future, given its benefits!
Andy
|
|
garynava
Luthier / Guitar Maker
Posts: 460
My main instrument is: Stanley No.5
|
Post by garynava on Aug 22, 2018 15:16:19 GMT
I’ve always believed that the neck joint, on a fretted instrument, should be as rigid as possible. The aim of the game is to ensure that the kinetic energy, from the movement of the player’s hand, is converted as efficiently as possible into sound. Making the neck joint rigid, is one step to ensure that energy is not absorbed into the instrument itself. I’m sure there are many who will disagree with me, but those are my views. The walnut archtop’s neck has now been affixed to the body and in these two videos (parts 1 & 2) you’ll see the lengths that I go to ensure the neck and body are as one (or as close to that as possible).
Cheers Gary
|
|
leoroberts
C.O.G.
Posts: 26,135
My main instrument is: probably needing new strings
|
Post by leoroberts on Aug 22, 2018 16:57:10 GMT
Fascinating... absolutely fascinating. I love the build threads on this 'ere place 
|
|
davewhite
Luthier / Guitar Maker
Luthier
Aemulor et ambitiosior
Posts: 3,548
|
Post by davewhite on Aug 22, 2018 17:25:13 GMT
Gripping viewing Gary - very elegant design and execution 
|
|
|
Post by lars on Aug 24, 2018 17:31:35 GMT
Superb craftsmanship as always from Mr Nava!
|
|
garynava
Luthier / Guitar Maker
Posts: 460
My main instrument is: Stanley No.5
|
Post by garynava on Aug 25, 2018 15:09:11 GMT
Sincere thanks for all the positive remarks Guys- much appreciated! The fretboard is now on, neck shaped etc. and it's had a good ol' clean-up, as you'll see in the photos below. Next step will be to make the bridge and get it playing in the white. Cheers Gary 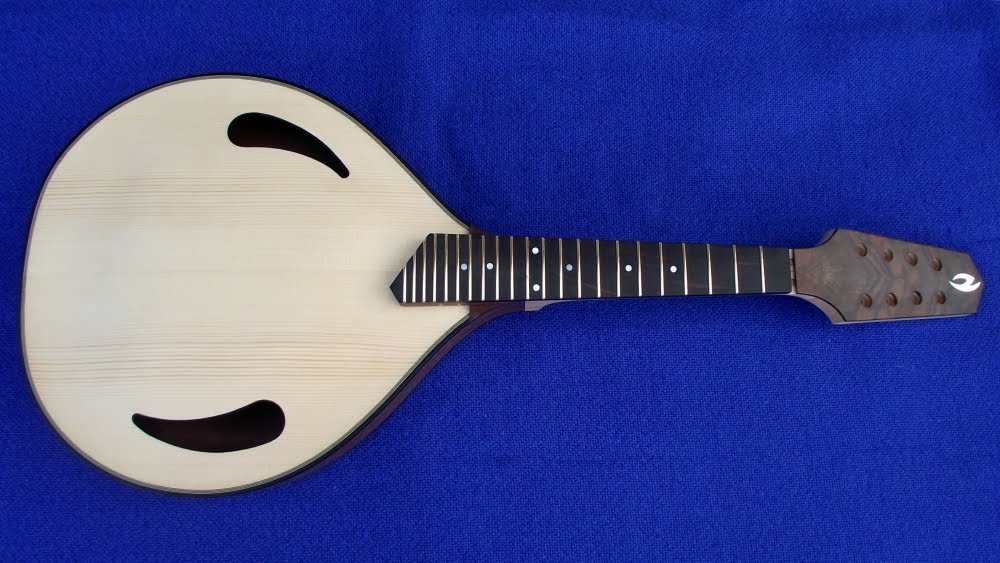 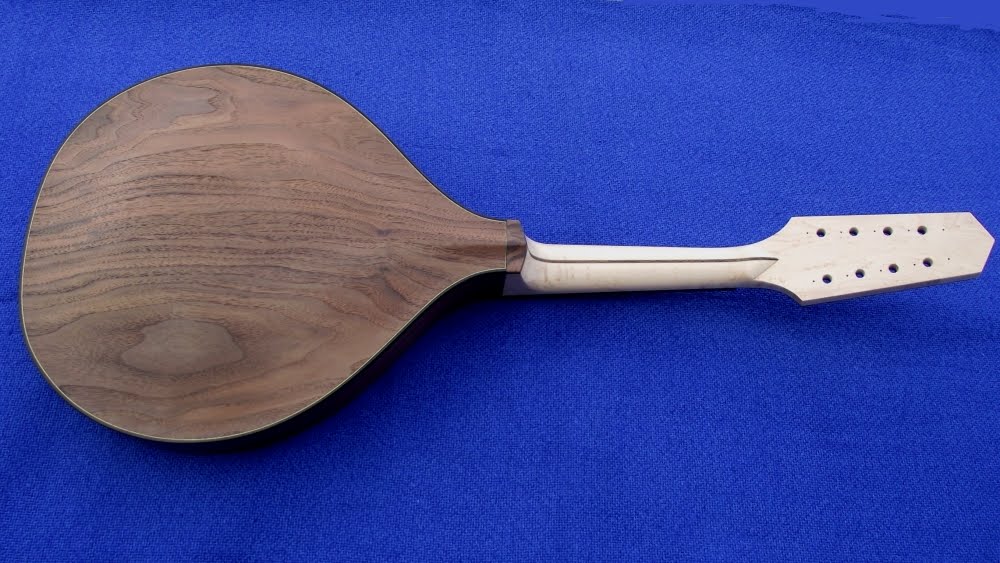 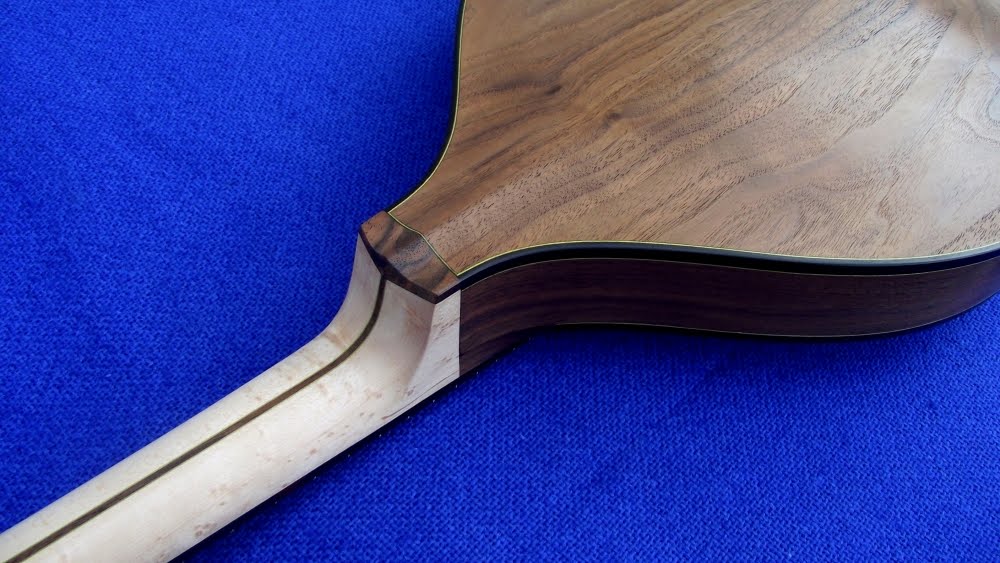
|
|
|
Post by Deleted on Aug 25, 2018 17:07:22 GMT
That is lovely Gary- only wish I had a spare £1500 to buy it, especially as I am mandolinless 😢
|
|
garynava
Luthier / Guitar Maker
Posts: 460
My main instrument is: Stanley No.5
|
Post by garynava on Sept 2, 2018 15:59:42 GMT
Here’s the latest video on the making of my walnut archtop mandolin. The construction of the instrument itself is complete and now is the time for the hardware to be fitted and to make its first sounds!
Cheers Gary
|
|
davewhite
Luthier / Guitar Maker
Luthier
Aemulor et ambitiosior
Posts: 3,548
|
Post by davewhite on Sept 2, 2018 17:05:49 GMT
Looks and sounds fabulous Gary  Cool tip about using four strings for doing the setup - duly noted and nicked 
|
|
ocarolan
Global Moderator
CURMUDGEONLY OLD GIT (leader - to join, just ask!)
Posts: 35,719
Mini-Profile Background: {"image":"","color":"c0cfe1"}
Mini-Profile Name Color: 182a3f
Mini-Profile Text Color: 733a1c
Member is Online
|
Post by ocarolan on Sept 2, 2018 22:05:41 GMT
Another fab vid Gary, thanks for taking the time!
Keith
|
|
leoroberts
C.O.G.
Posts: 26,135
My main instrument is: probably needing new strings
|
Post by leoroberts on Sept 3, 2018 7:22:52 GMT
Excellent video, again, Gary
|
|