|
Post by mel on Aug 23, 2015 20:35:25 GMT
Just got this one strung up, it's an SJ in EIR and Sitka Spruce, 46mm nut with extra chunky neck. The final steps always seem to go so quick compared to all the whittling and gluing that goes before. Always a pleasant surprise when one unexpectedly magics itself into existence.   
|
|
|
New SJ
Aug 23, 2015 21:01:15 GMT
Post by earwighoney on Aug 23, 2015 21:01:15 GMT
Nice work.
What finish did you go for?
|
|
Martin
Administrator
Posts: 11,881
Mini-Profile Background: {"image":"http://mandocello.org/lytebox/images/adirondack.jpg","color":""}
Mini-Profile Name Color: 0a530b
Mini-Profile Text Color: 4f3517
|
New SJ
Aug 23, 2015 21:05:48 GMT
Post by Martin on Aug 23, 2015 21:05:48 GMT
Lovely guitar, Mel. I'd love to know more about it and your build process.
|
|
ocarolan
Global Moderator
CURMUDGEONLY OLD GIT (leader - to join, just ask!)
Posts: 33,963
Mini-Profile Background: {"image":"","color":"c0cfe1"}
Mini-Profile Name Color: 182a3f
Mini-Profile Text Color: 733a1c
|
New SJ
Aug 24, 2015 8:11:27 GMT
Post by ocarolan on Aug 24, 2015 8:11:27 GMT
Fine looking guitar there mel. Do you have any recordings of it? Keith
|
|
|
Post by mel on Aug 24, 2015 14:47:36 GMT
Hi, Thanks!
I French polished this one. It's sister was destined for nitro, although plans have changed on that. No recordings at the mo, the sound changes a lot in the first few weeks so I may make some then.
This guitar is number 5 in a run of 6 intended for developing one of my SJ designs and experimenting with my build methods. Tonally I'm looking for 'a fingerstyle-OM with a bit of extra bottom end'.
|
|
|
Post by mel on Aug 24, 2015 15:21:18 GMT
I spend a lot of 'building' time doing critical listening. I have some reference guitars of my own, and I get to play some of my friends also. I do A/B comparative listening, just playing one on it's own it's not easy to hear what's what. I think the ear-training is very important.
After I select the wood I join the tops and backs in a pretty standard way, then they're cut to shape. I use a small amount of CNC on the actual guitar. All the jig holes are CNC cut, as well as the outlines of the top, back, bridge, fretboard, headstock and soundhole reinforcement.
Rosette is inlaid and the top and backs are thicknesses against a stiffness reference plate on a drum sander. The plates are exactly the same size which helps recording the density, which I suppose might be useful later on.

I set the soundhole reinforcement plate with a guide. This plate goes a long way to locating the position of the X brace and the upper transverse brace so it's really key in laying the top out. I used to use a template to mark the brace positions, but now I don't. Once the X brace is in position it's quite straightforward to mark out the other braces using a steel rule and a square. Wood is a little flexible so some care is needed but nothing a little measurement can't take care of.
After this I dremel the soundhole. The Bishop Cochran router base makes the job much more pleasant.

|
|
|
Post by mel on Aug 24, 2015 15:35:07 GMT
Headblock is based on the Martin design. Sorry for the marks on the side in this pic, the final finishing and rounding hasn't been done at this point.
I drill the jig holes using CNC, but hand cut the rest of the block with hand tools now. I attach a template to the top to mark the outline then saw and plane it then sand it to finish. I used to use a belt sander, but it's just as easy, and much less messy to do with edge tools.
I make the block with tapered sides so that the edge doesn't line up with grain lines in a bid to reduce the probability of cracking. The upper transverse brace butts up against it.

This was during the making of the outside mould.

|
|
|
Post by mel on Aug 24, 2015 15:43:18 GMT
Kerfed lining is bandsawn with a little jig that slides back and forth on the track. The piece of ply at the back stops it cutting all the way through. At this time I lined up each kerf by eye, but it wasn't easy to keep a consistent spacing.

There were a lot of fancy solutions on the internet but the simplest one seemed OK. It a one way ratchet that indexes the previous kerf. This set is a bit fuzzy as it was cut using a coarse rip blade. After this they get a bevel planed onto them.
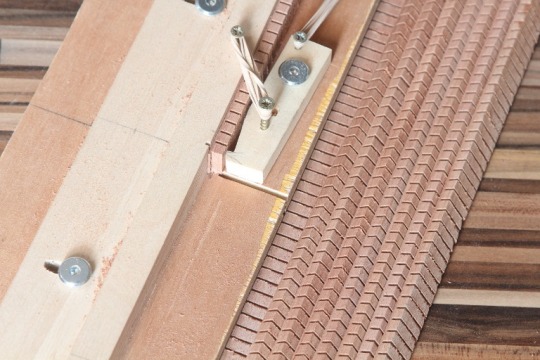
Yeah I'll be increasing the size of my tail block. I've been noticing a lot of people's ones are much stockier.

|
|
|
Post by mel on Aug 24, 2015 15:54:54 GMT
In a bid to ensure once and for all my back braces went on easily and exactly in position I made some jig plates to set them. The templates attach and locate with bolts into the jig holes in the back.
The centre strip is exactly 1 steel rule wide.

This template is for notching the centre strip. A little care is needed here, as the marking knife is on the good side for one of the cuts as well as being long grain.
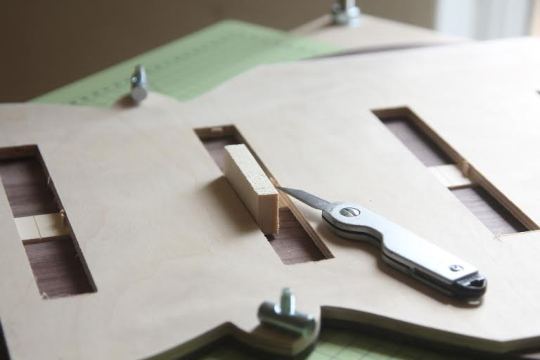
And yet another template sets the ends of the braces. I think it's safe to say that these back braces are exactly where they should be!
This whole thing is sat in a profiled solera to give the back curvature.
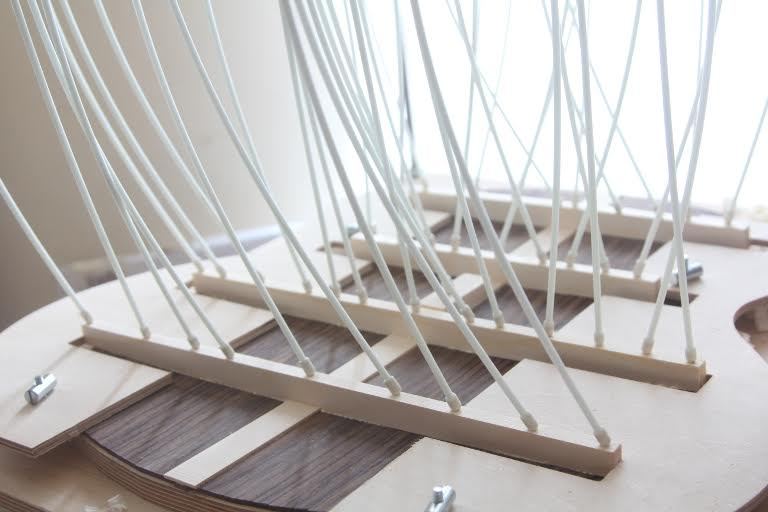
|
|
|
Post by mel on Aug 24, 2015 16:01:55 GMT
This is setting the height of the brace ends. I know there are some fancy jigs to do this, but this method works well enough. I go one mm oversize to rough it then switch to the next key size down to finish it. At this point I wasn't letting the braces into the sides, only the lining, but I may change that.

I made this little plane for shaving braces.

|
|
|
Post by mel on Aug 24, 2015 16:09:49 GMT
Brace positions are marked out by measurement. The braces bottoms are pre shaped before being glued on then the whole lot is glued up in the profiled solera at controlled humidity.

The the sides glued on. The braces are final shaped at this point. This guitar is an earlier vintage, the first of this set.
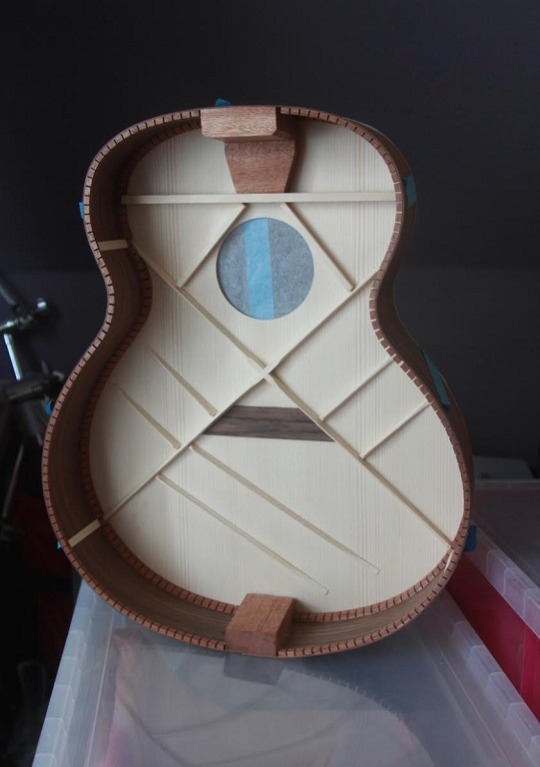
|
|
|
New SJ
Aug 24, 2015 16:17:50 GMT
Post by earwighoney on Aug 24, 2015 16:17:50 GMT
Hi, Thanks! I French polished this one. It's sister was destined for nitro, although plans have changed on that. Thanks for the info. I took delivery of new guitars one with FP and one with nitro, I expected the nitro to be more robust than the FP but it doesn't seem to be the case. Great work on your FP, it looks smooth, shiny and even. Excellent build threads too. Are you a pro or a hobby luthier? Fine wood working.
|
|
|
New SJ
Aug 24, 2015 17:20:57 GMT
Post by mel on Aug 24, 2015 17:20:57 GMT
Hi, Thanks! I French polished this one. It's sister was destined for nitro, although plans have changed on that. Thanks for the info. I took delivery of new guitars one with FP and one with nitro, I expected the nitro to be more robust than the FP but it doesn't seem to be the case. Great work on your FP, it looks smooth, shiny and even. Excellent build threads too. Are you a pro or a hobby luthier? Fine wood working. Oh that's interesting. Did you find that there are any tonal differences that might be due to the type of finish? Thank you for your kind words. I'm not a pro builder... at the moment. I'm very devoted to this though, I suppose you could say I'm a student. For most of my life I made consumer electronics which have life spans of 5, 10, 15 years. Now that I'm older I feel like making use of my time building something more lasting. Mel.
|
|
|
Post by mel on Aug 24, 2015 17:44:11 GMT
I'm using V-joints for my necks. It's all hand cut, I approach it like a mortice and tenon, just with different angles. 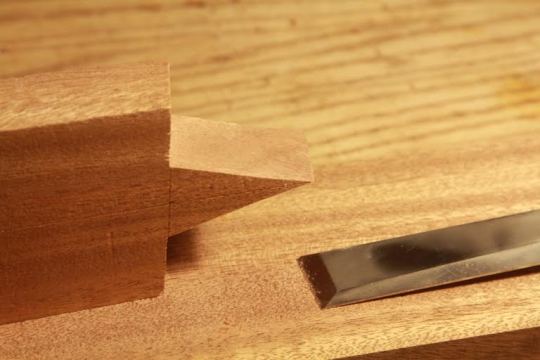  I have been spending a bit of time trying to get the headstock nicely proportioned. I don't know if Martin upsize the headstock on the larger bodies, but I know if I put an OM sized Martin headstock on a SJ it looks a bit out of proportion to my eye. Initially I tried a long headstock, about as long as the Guild headstock which is very oversized. I also spaced out the tuners more to take advantage of the extra length. It had interesting effect on the bendability of the strings. The string to string difference in nut to tuner length made some strings more bendy than normal, and it was quite apparent when playing. So for my latest headstocks I take care to choose the tuner distance and spacing depending on what I want to achieve. 
|
|
|
New SJ
Aug 24, 2015 17:54:59 GMT
Post by earwighoney on Aug 24, 2015 17:54:59 GMT
I took delivery of new guitars one with FP and one with nitro, I expected the nitro to be more robust than the FP but it doesn't seem to be the case. Oh that's interesting. Did you find that there are any tonal differences that might be due to the type of finish? Thank you for your kind words. I'm not a pro builder... at the moment. I'm very devoted to this though, I suppose you could say I'm a student. For most of my life I made consumer electronics which have life spans of 5, 10, 15 years. Now that I'm older I feel like making use of my time building something more lasting. Mel. The nitro guitar is a Red Spruce/Mahogany 12 fret 00 steel string, and the FP guitar is a Western Red Cedar/African Padauk flamenco guitar and due to the differences I've got no idea whether FP produces a 'better sounding' guitar than nitro/etc but I absolutely love the feel of the FP neck, the smell is wonderful and a FP finish in the flesh to my eyes anyway is more appealing than a nitro/poly finish (like comparing a unwaxed apple to a waxed one if that makes sense). No idea whether a FP guitar is a better sounding instrument but I'd pick it every time if I could. Keep up the great work with the builds and keep posting photographs of the progress. It's always a pleasure to see build threads here. Are you planning to make any other body sizes aside from the SJ?
|
|