|
Post by lars on Feb 9, 2020 17:32:27 GMT
Now that I've finished the two mandolins, it's time to go on with the next project. Although I've built thirteen stringed instruments so far (one mountain dulcimer and twelve instruments from the mandolin family), I've never ever built a guitar. So it's about time! I've got two different guitar models in the pipeline but I'll begin with one. First out is a Grand Concert or 00 sized guitar which will be followed by a larger guitar, about the size and shape of a Grand Auditorium but with some similarities to a Small Jumbo. The two guitars will share many features and be similar in design. Here is the outline and bracing pattern: 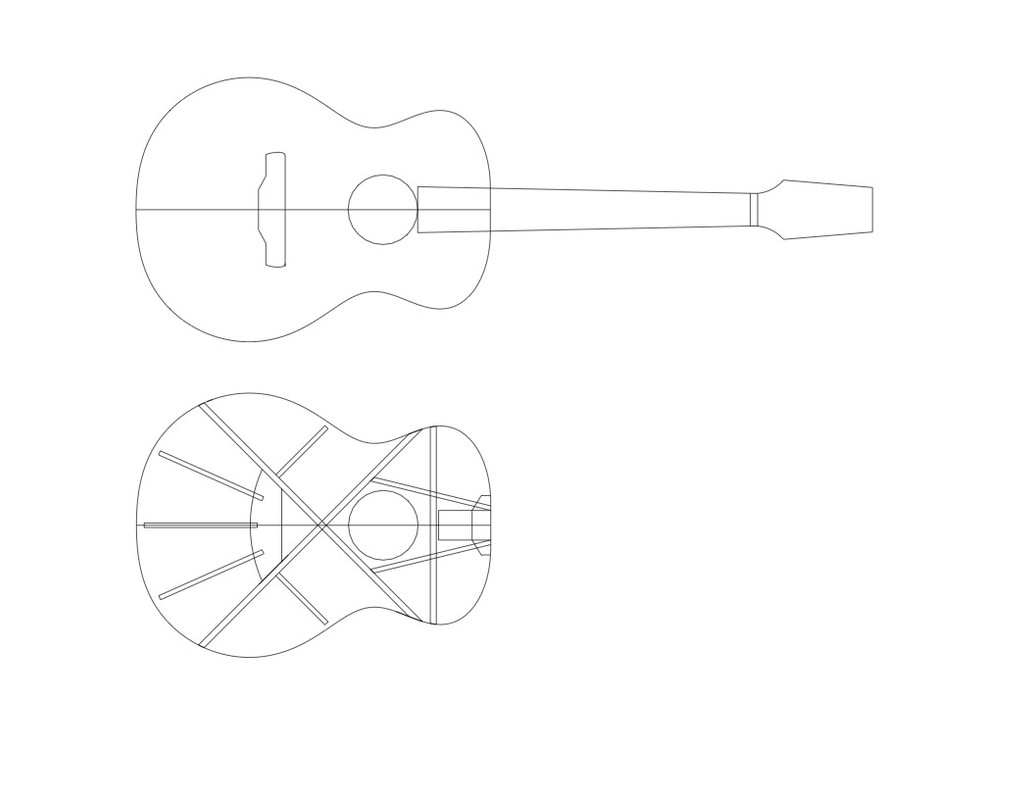 It's kind of funny - I've spent so much time thinking about design and construction and the end result looks like - a rather ordinary guitar! Anyway - here are some of the thoughts behind: The traditional guitar body shape was first made for instruments with necks meeting bodies at twelfth fret. Later 14 fret became more or less standard and as a result, the bridges were put forward closer to the sound hole (though Martin preferred to shorten their bodies). It's a lot of talk among luthiers about "the sweet spot" where the ultimate position for the bridge should be. Many believes that this sweet spot is at the center of the lower bout. My approach is not to move the bridge backward, but instead move the center of the lower bout forward. So the lower half of the lower bout is rounder than usual which put the widest part a bit forward. That also means that the waist is put forward and the upper bout is slightly smaller. Otherwise are the dimensions very close to an ordinary 00-guitar. The lower bout is about 36 cm wide. I've also spent lots of time investigating different bracing patterns. The conventional bracing with two diagonal "sound bars" doesn't make sense for me. Many modern luthiers utilizes hybrid bracings, where X-/lattice and X-/fanbracing seems to be the most common. After a lot of thinking forth and back I've decided to use the latter. I've taken more than one look at Edwinson guitars (like Franglais have done) but I've landed in a slightly simpler design, more like PRS guitars. Other than that, I've decided to stay with the principles I've learnt in the previous builds. I'll keep things simple (but hopefully elegant) and focus on things that are structurally important. So there will be bindings, but no purflings, the rosette will be simple and designed to strengthen the sound hole. I'll stay with carbon fibre rods in the body and a floating fretboard with support from a neck extension, etc. Whith other words - Dave White will continue to be an inspiration. Specifications: Top - European Spruce Back, Sides and Neck - African Mahogany (Khaya) Fretboard and Bridge - not yet decided, either Ebony or Laburnum Bindings - Birch Linings - either Cedrela reversed kerfed linings or laminated Birch Scale length - 632 mm (24.9" Martin short scale) Many details are yet to be decided... ps/This will be a slow build. I hope to be ready before summer, but who knows...
|
|
|
Post by lars on Feb 9, 2020 17:58:08 GMT
The first stepsFirst some of the bits and pieces I will use for this build: 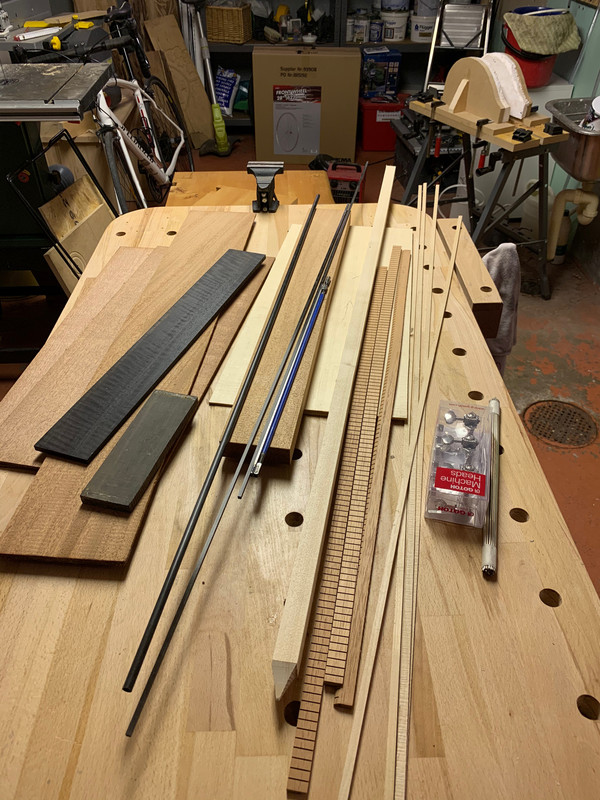 As I mentioned in the previous post I'm not sure if I'll use the ebony fretboard and bridge blanks shown here. I'm actually more inclined to use Laburnum, but have to machine those pieces first. The stick in the middle is for bracing. It's a stick you use to position house foundations and roads during construction work. But some of those sticks where made of extremely tight grained spruce and "quarter sawn", so I bought quite a few. The tuners are open gear Gotoh. I have yet to build a mould for the body and a radius dish for the top radius. But I couldn't help beginning with the top - just to give me a feeling that I'm building a guitar. The wood is bought as B-graded European Spruce. I bought a 10-pack of B-graded tops at Madinter with low expectations. It turned out that many of the pieces were more than alright. None of them were suited for a Dreadnought or Jumbo, but I'll get quite a few good tops for mandolins and other CBOM-s. And two or three tops that are suited for smaller guitars. Like this one. I don't have access to a thickness sander so I hand plane all boards. After initial planing of both sides I glued the two halves with "wedge and rope". As this is my first large instrument I had to make new wedges. Unfortunately the rope was very elastic, so I had to support with extra wedges and clamps: 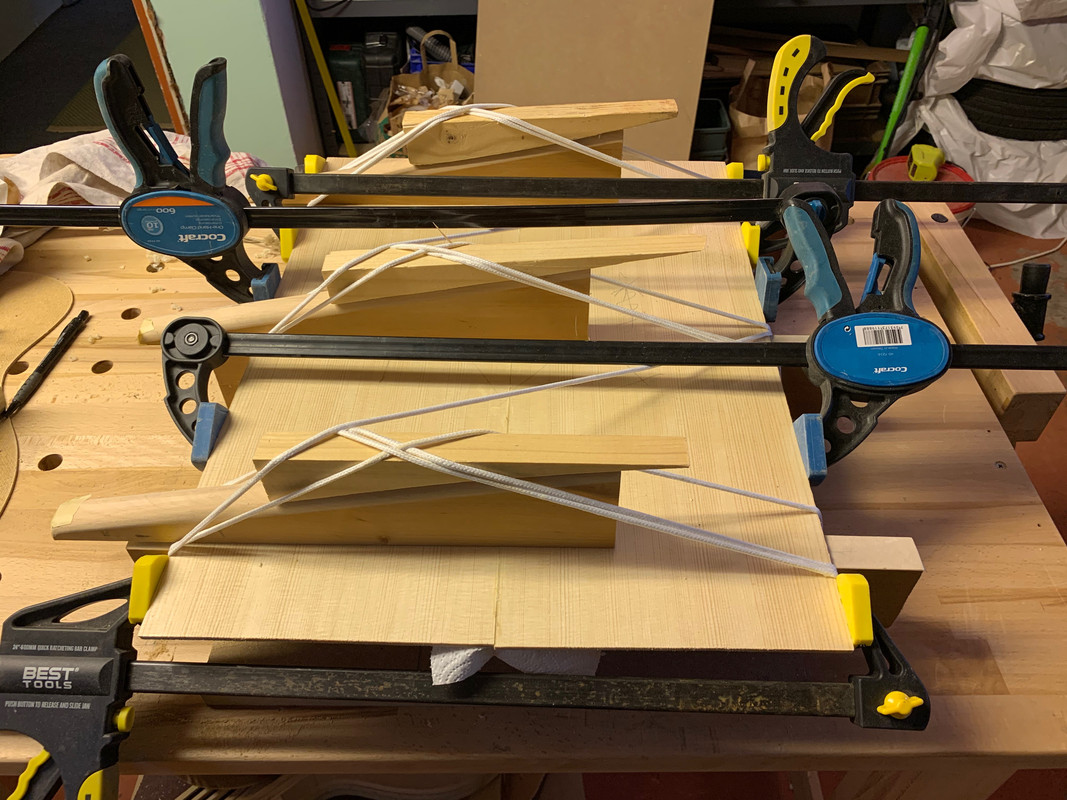 After that I planed first one side and than the other. After some planing I measured the thickness at various parts of the top: 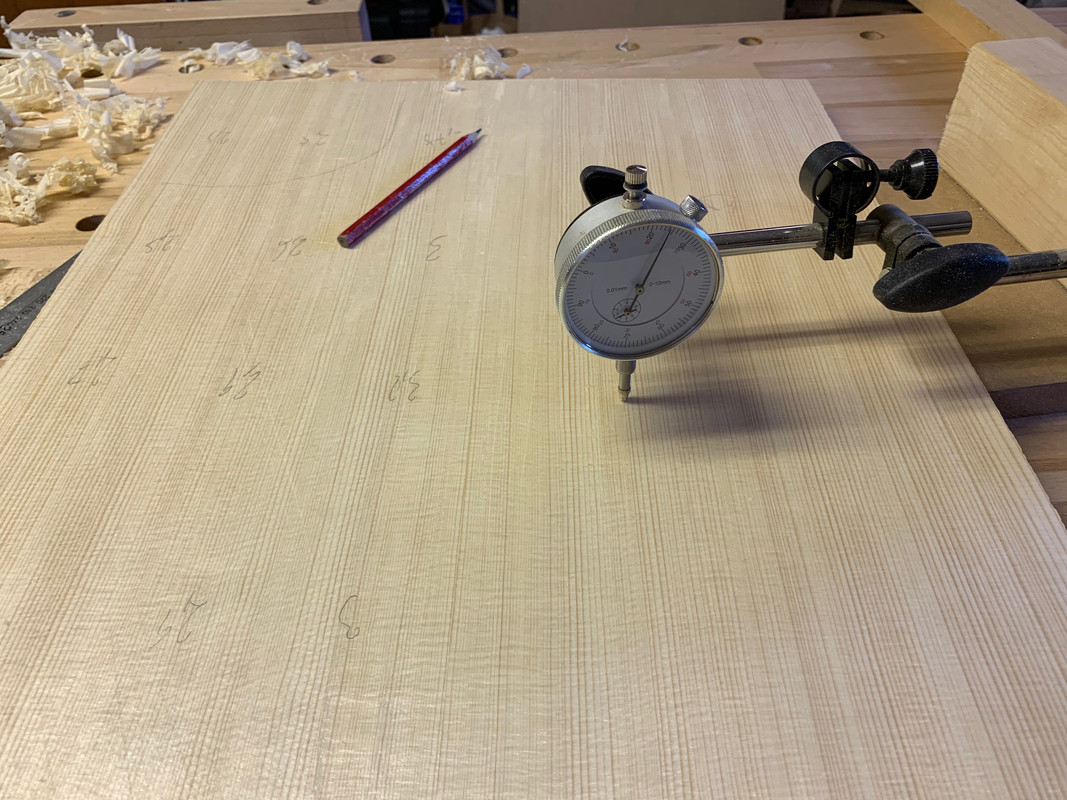 And did it again and again: 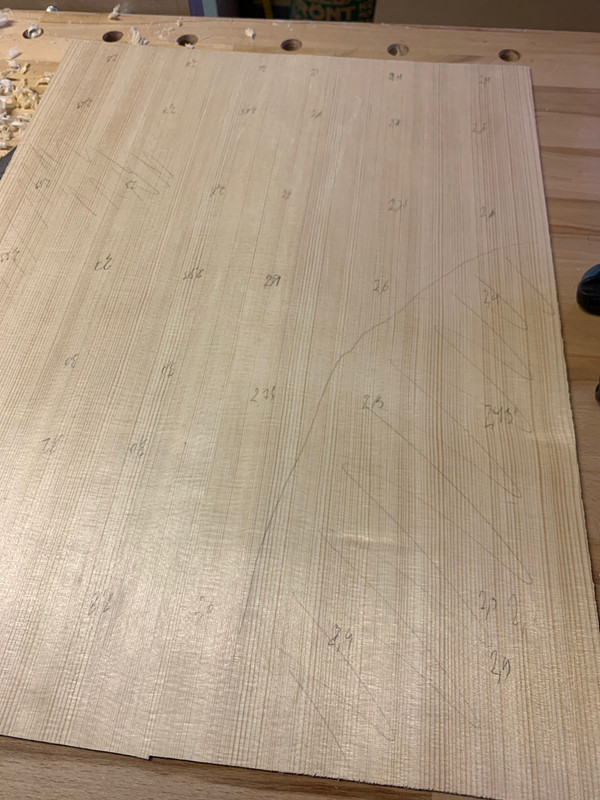 I aimed for 2.5 mm, but before I knew it I was down to 2.4 on many spots. With some sanding I probably ended at a thickness of 2.3. My idea is to have a relatively thin top paired with relatively stiff bracing, but this was a bit thinner than I planned for. And here is the top plate: 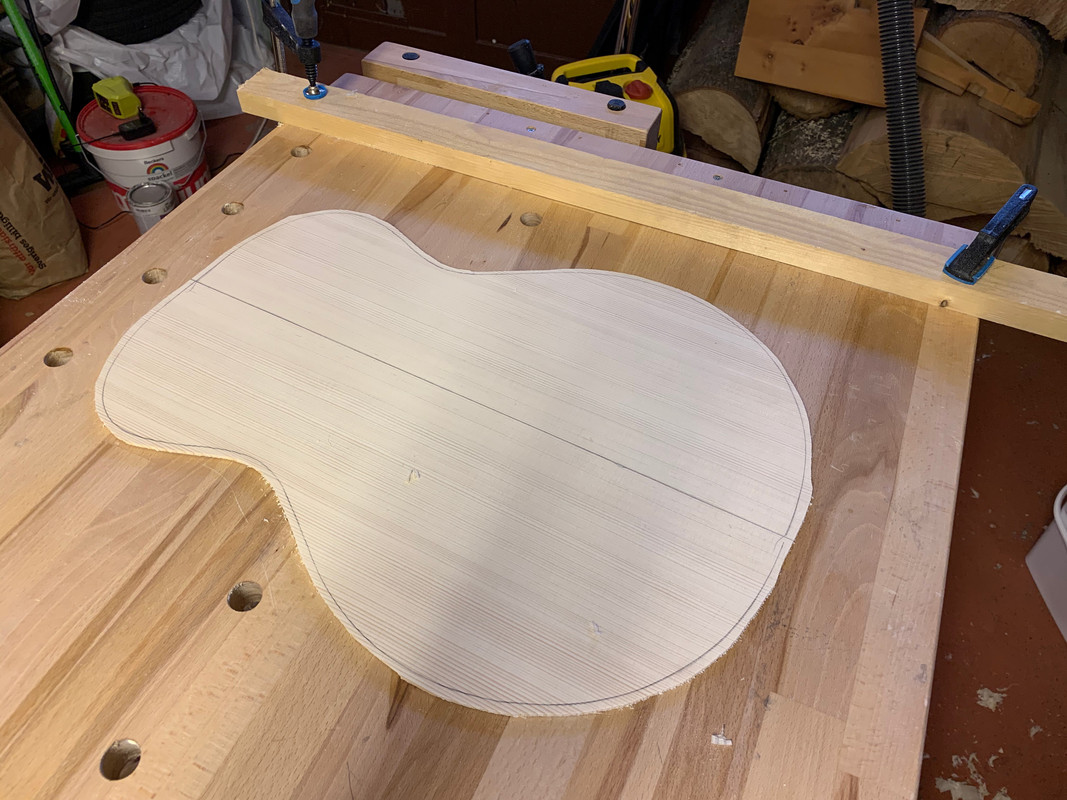
|
|
garynava
Luthier / Guitar Maker
Posts: 461
My main instrument is: Stanley No.5
|
Post by garynava on Feb 10, 2020 15:40:21 GMT
Good luck with your first guitar- look forward to watching this evolve Cheers Gary
|
|
|
Post by lars on Feb 10, 2020 16:18:32 GMT
Good luck with your first guitar- look forward to watching this evolve Cheers Gary Thanks, Gary! I'd love to hear your comments as the build evolves. And I can surely need advice along the way from experienced luthiers like you.
|
|
|
Post by lars on Feb 20, 2020 22:03:33 GMT
Most of the time since the last update has been spent by making a mould for the body and a new radius dish for the top. Here are some shots from the making of the radius dish. It has a radius of about 7.5 m or 25'. 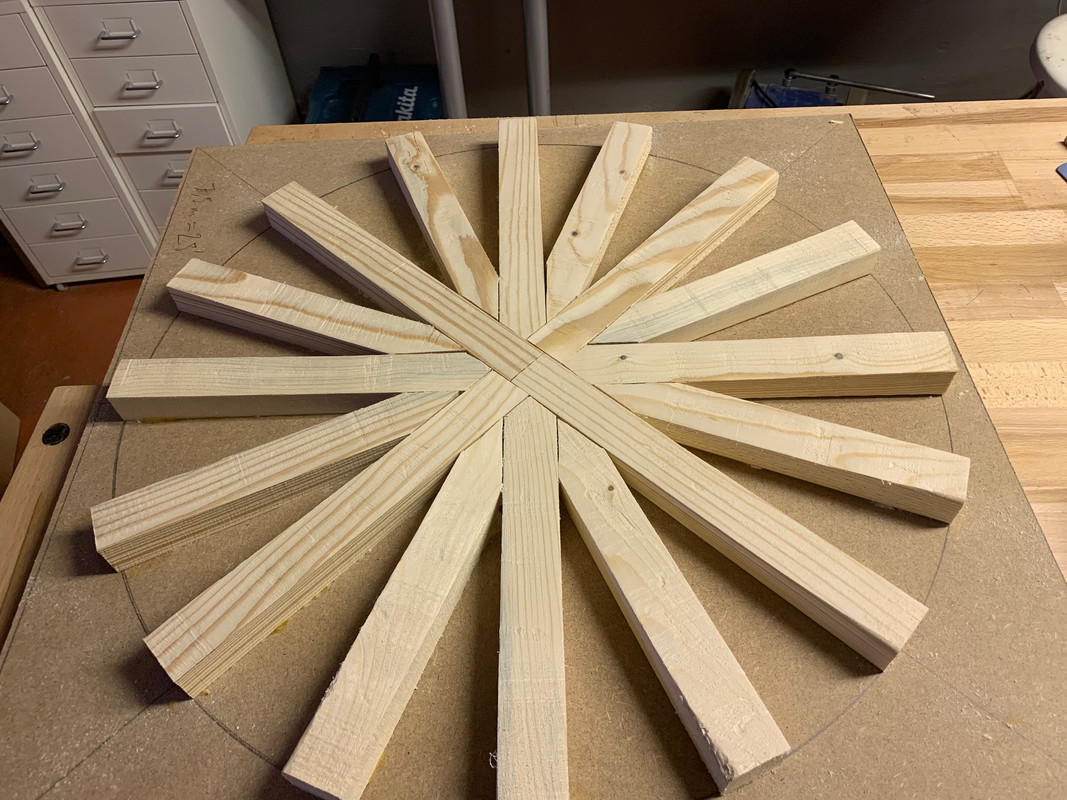 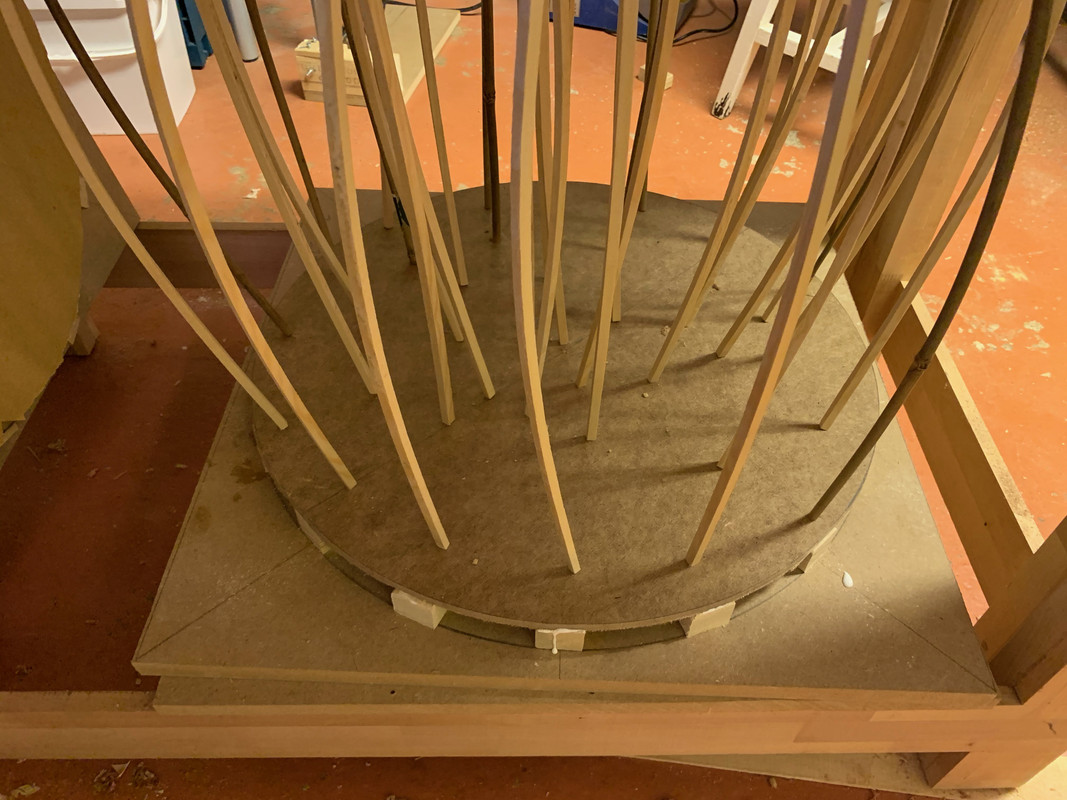 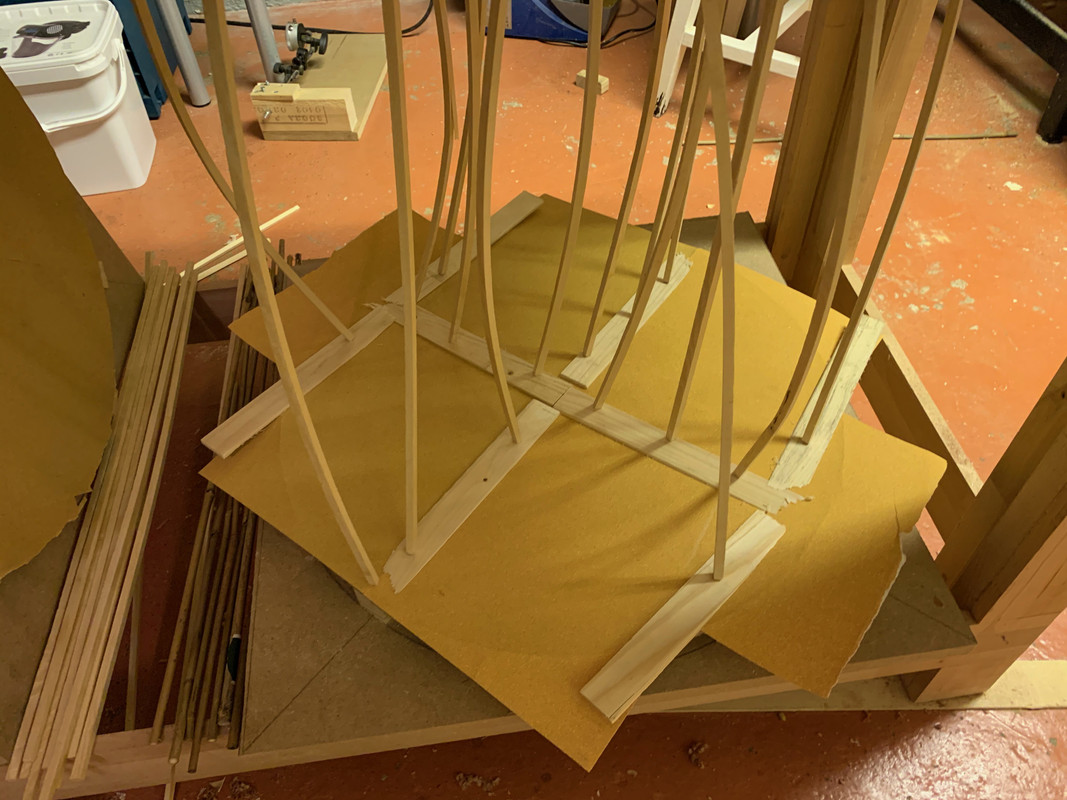 The back plate and the sides were thicknessed with hand planes, the same way as the top. The back was a bliss to plane but the sides were truly pains in the *rse. Too much interlocking wood grain, so there were tear-outs no matter which direction I worked in. A home made high angle plane helped a little with the tear-out, but just a little. 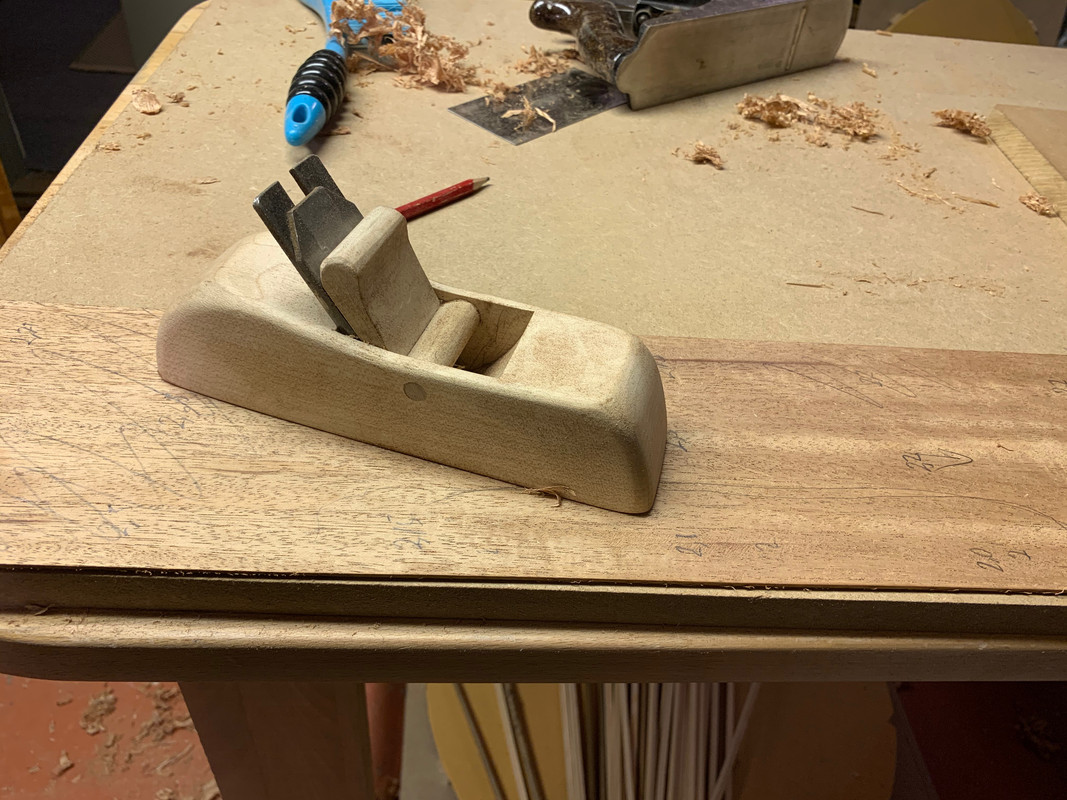 The last thinning was done with a scraper, which dealed with most of the tear-outs. Here are the top and back plates: 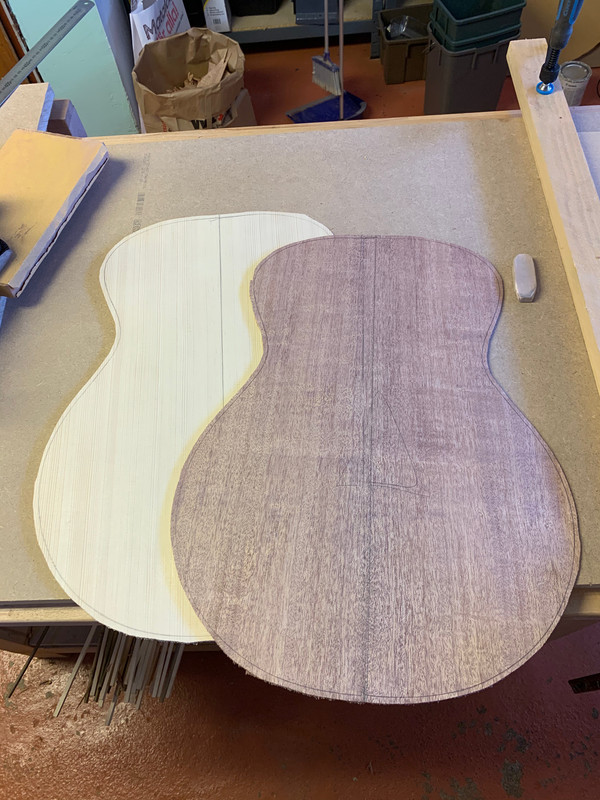 The next step was to make the rosette and sound hole. The rosette is made of an African mahogany called Sipu. ![]() 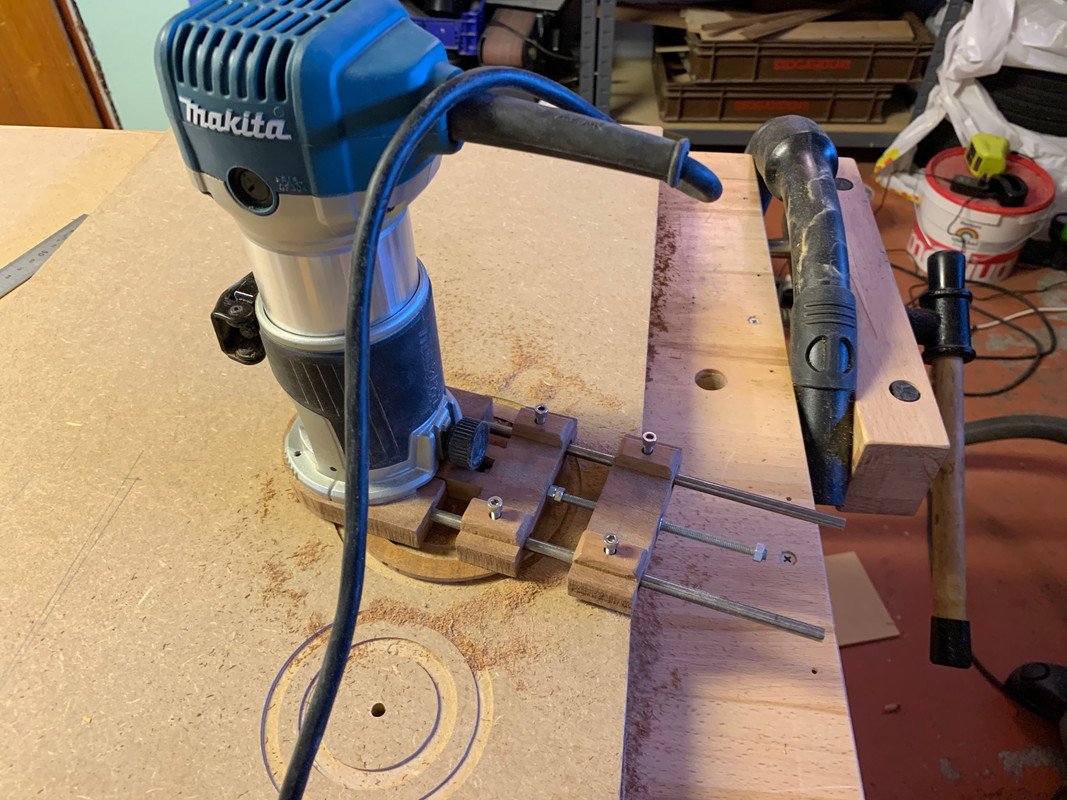 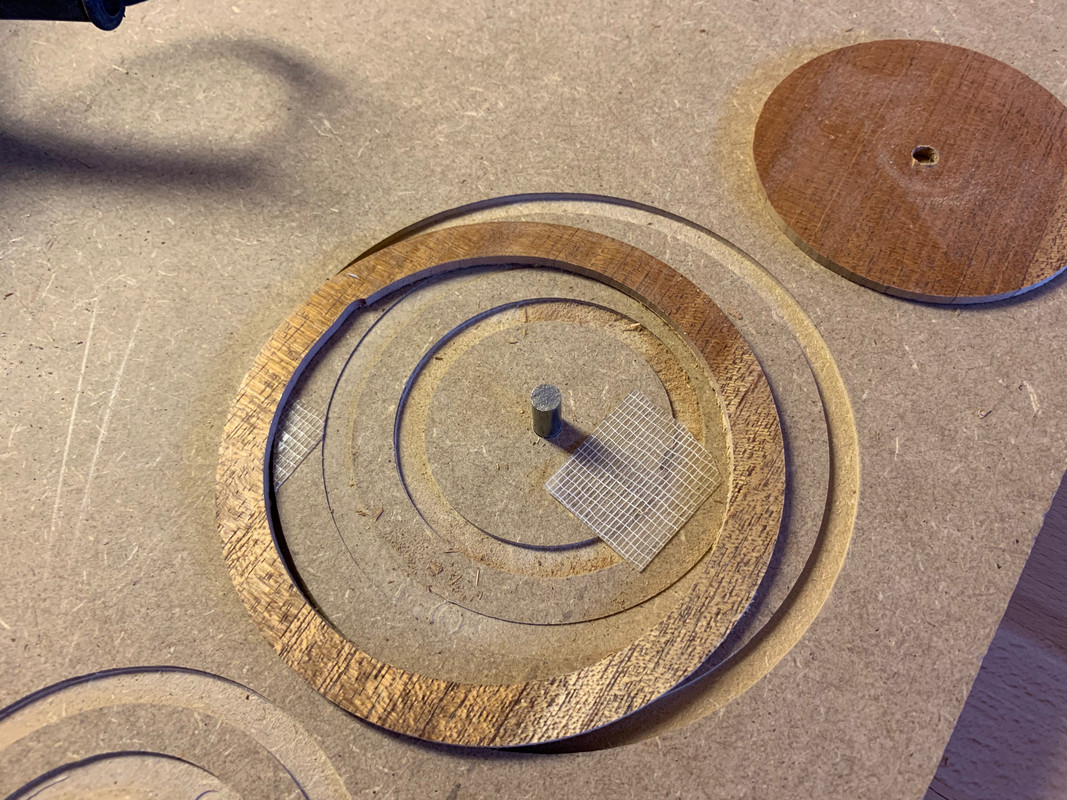 The channel for the rosette is routed in the top: 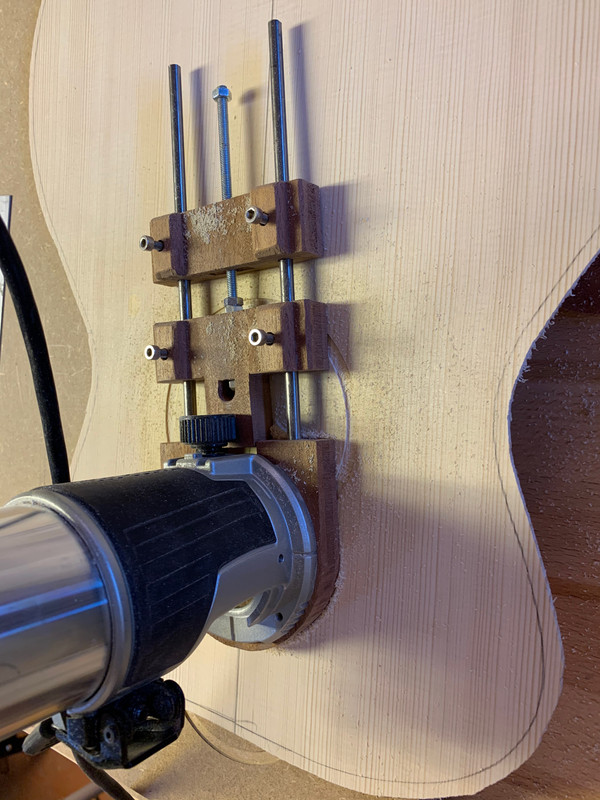 And the rosette is glued with a thin black purfling strip (a strip of black dyed maple veneer). 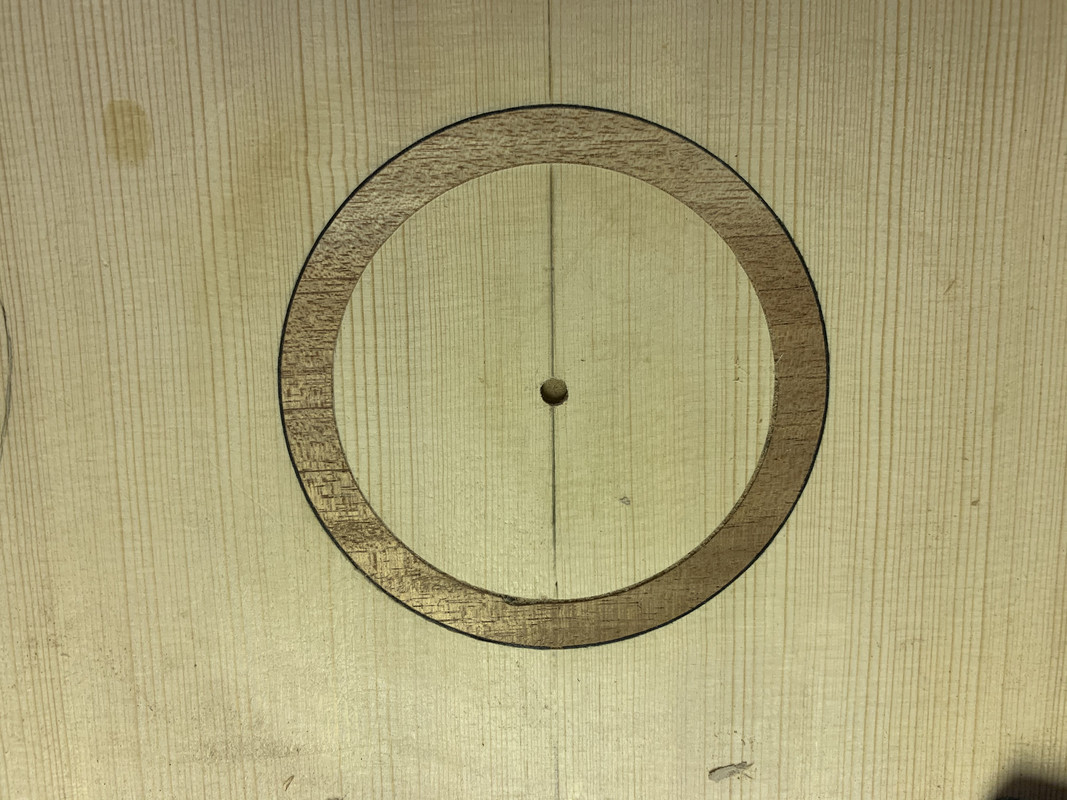 The cross grain back plate of European spruce is glued: 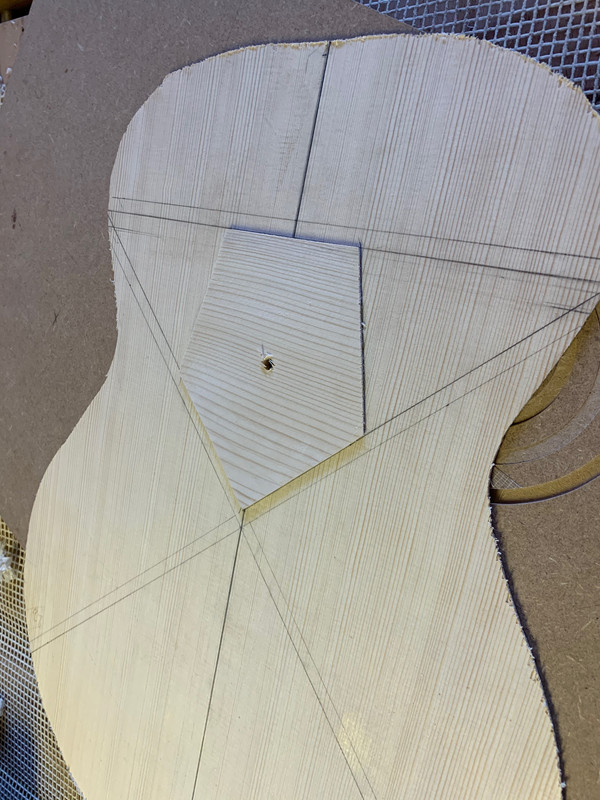 The sound hole is cut with the router: 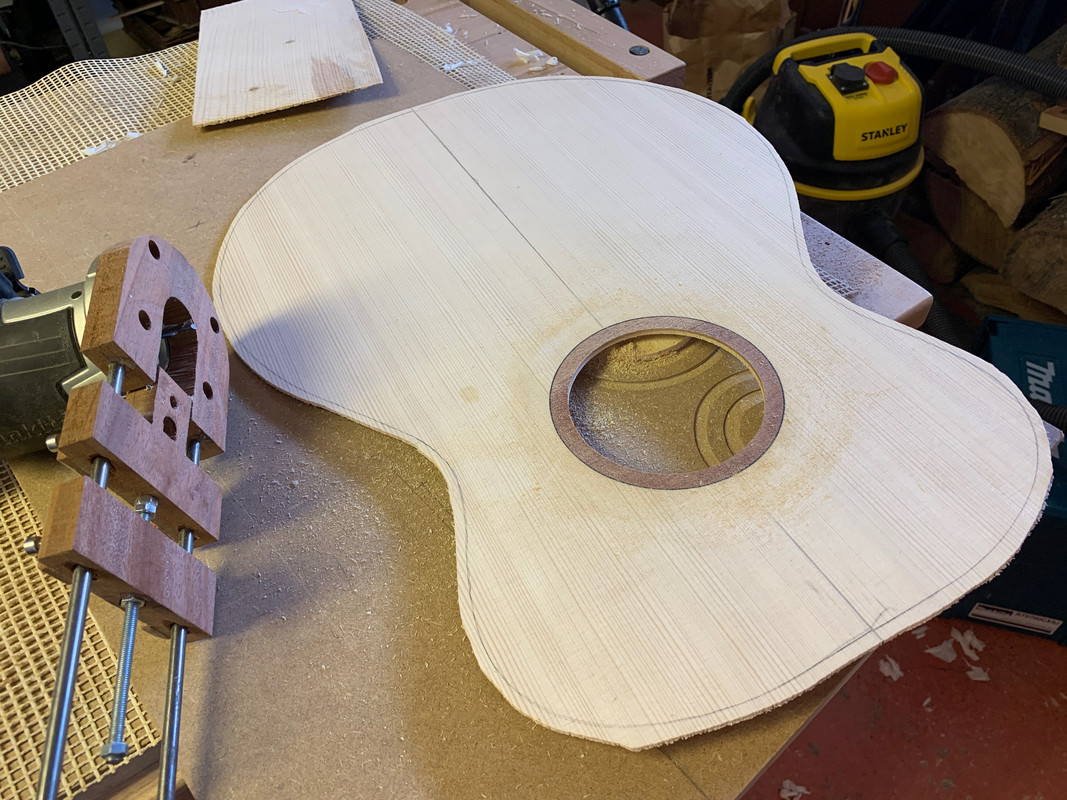 A strip of birch is bent on the hot pipe to bind the sound hole. The finished sound hole looks like this: 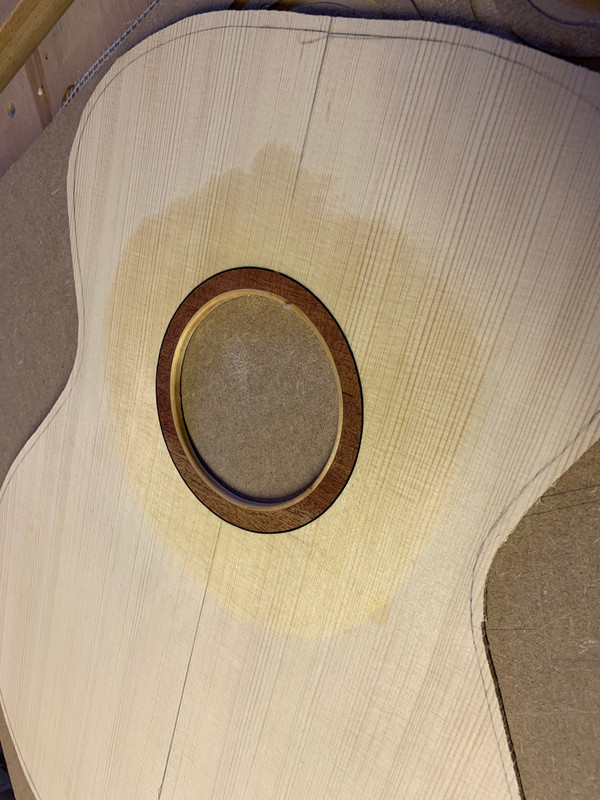 And this is what the top looks like now: 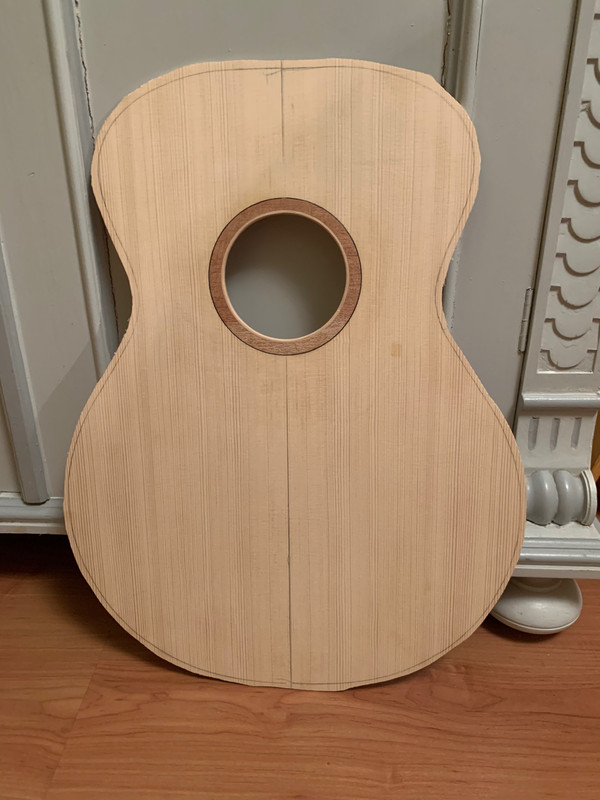
|
|
|
Post by lars on Feb 26, 2020 18:21:08 GMT
Making the rim - part II bend the sides with a hot pipe. I've got a very simple setup consisting of a steel pipe (a piece from a road sign) and a hot air gun. I've used it for all my instruments so far and it's served me well. I was nevertheless nervous before bending these sides, as a guitar side is more complicated than a mandolin. But it turned out very well. For bending the waist I had a damp cloth between the pipe and the wood, as I had to keep the wood in a fixed position during the tight bend, and I didn't want any burned marks. 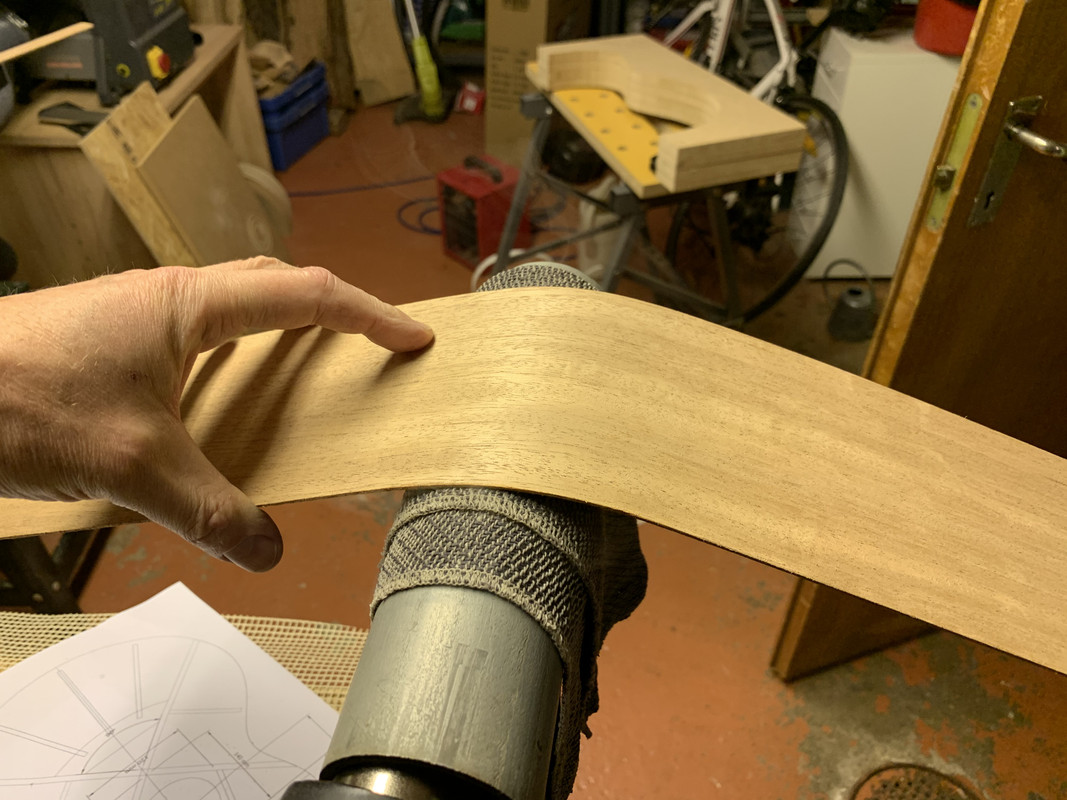 For the rest of the bending I wet the wood and bent it directly with rocking and sliding motions. Here are the bent sides resting in the mould: 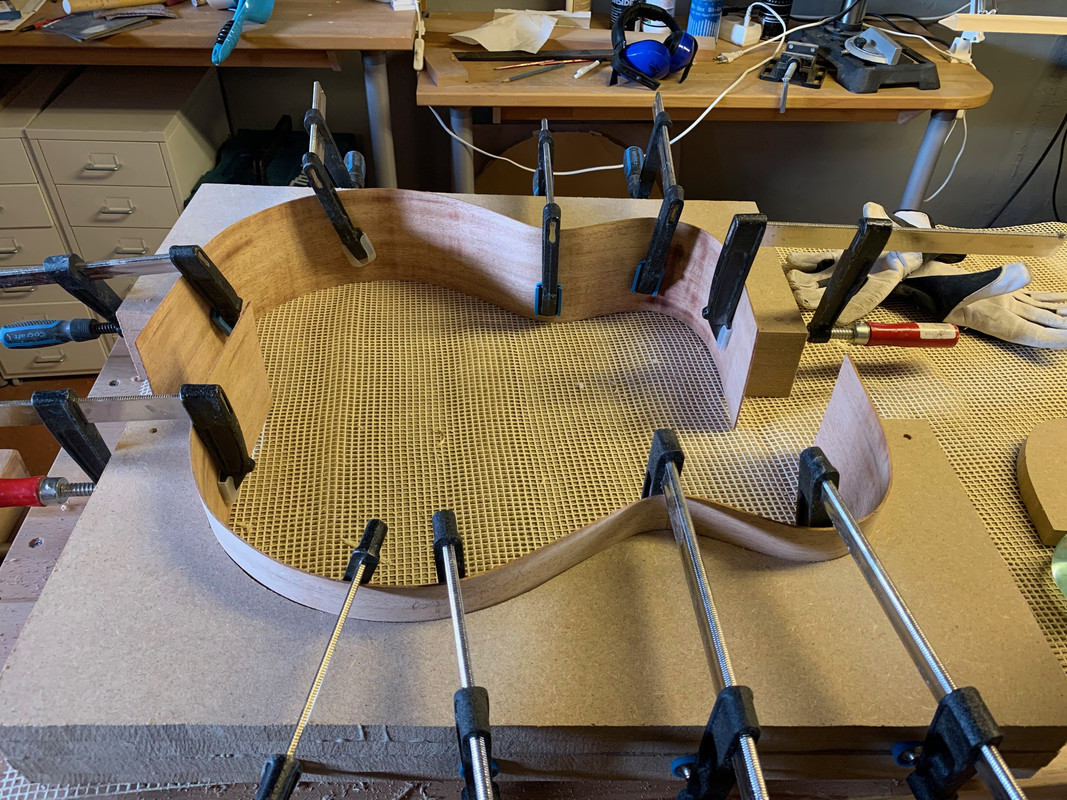 Today I've made the neck piece and the tail piece. Here are a few steps from making the neck piece: 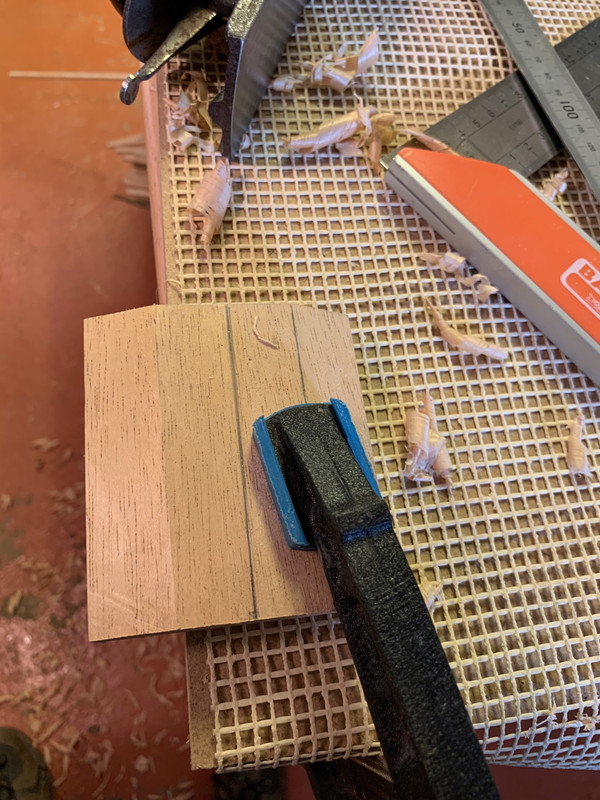 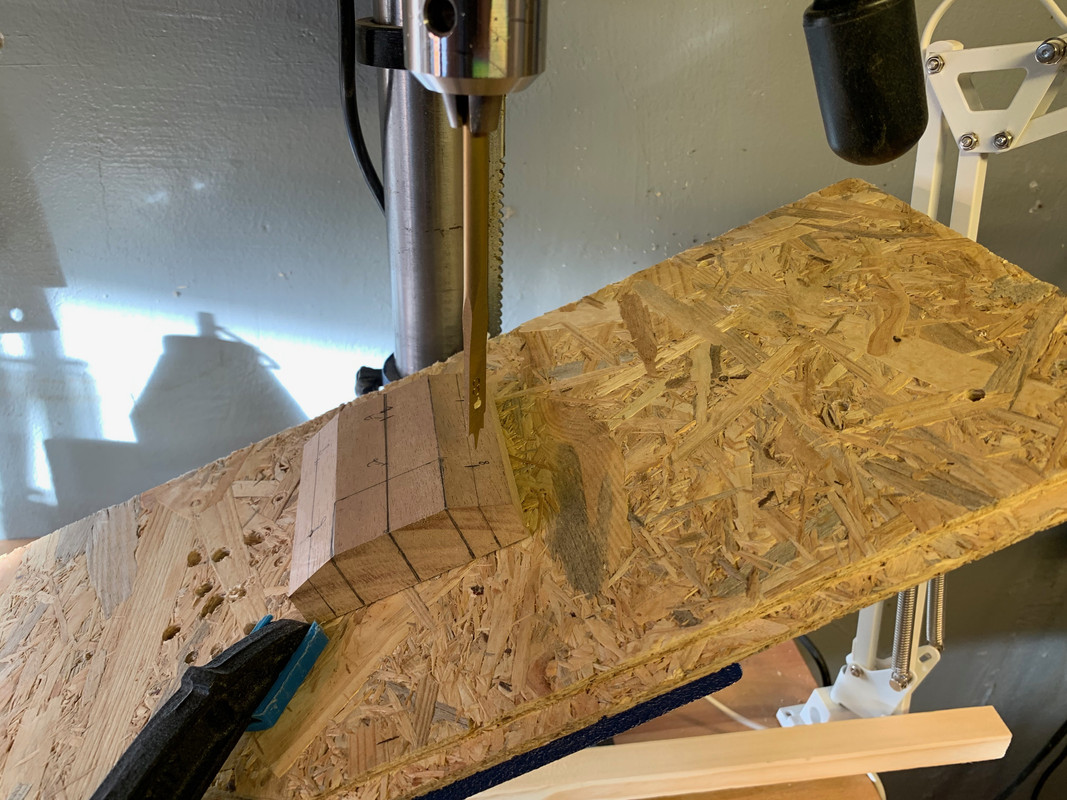 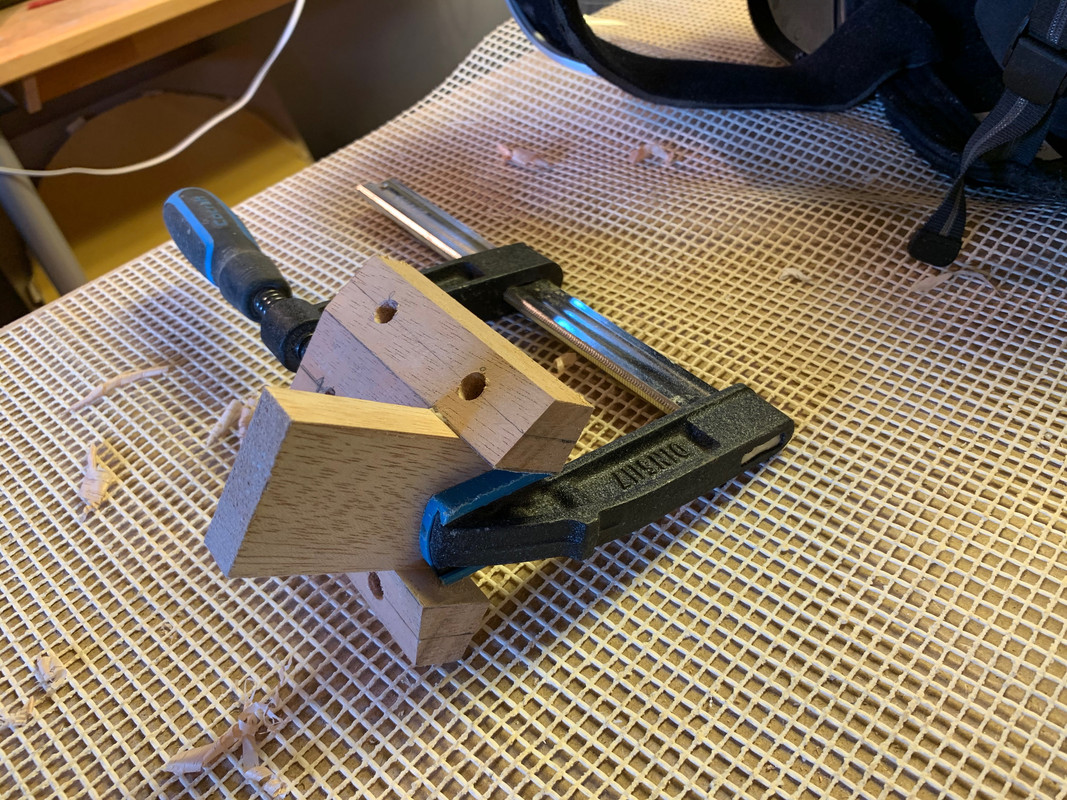 The tail piece was made from three layers of wood were the middle layer was glued cross grain against the other layers (and the sides). This is from preventing cracks if the instrument would fall on the strap pin. Here the tail piece is glued to the sides: 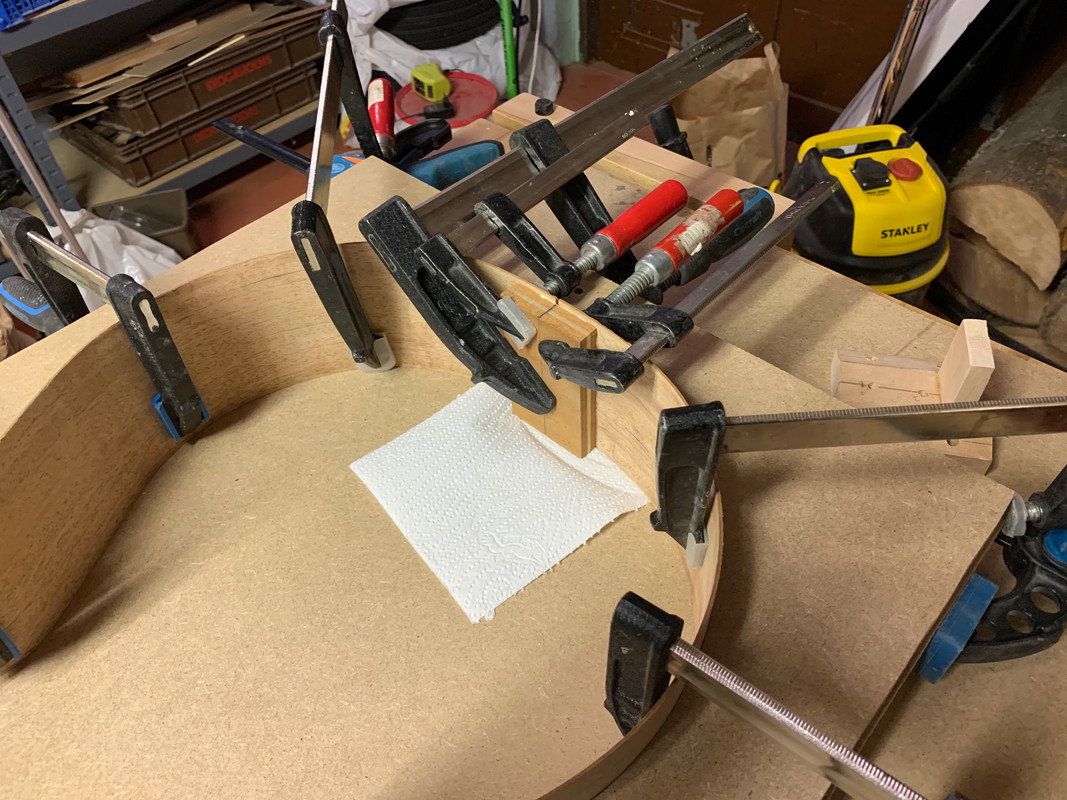 And here the neck block is being glued: 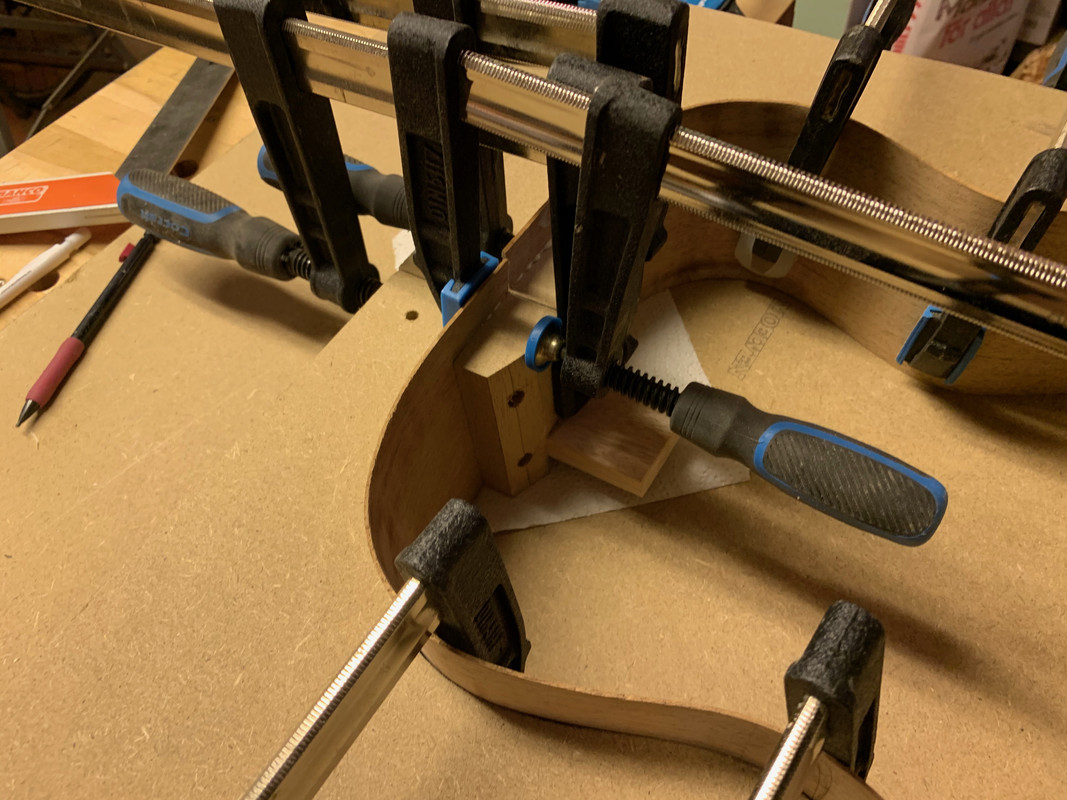 And the rim set in the mould: 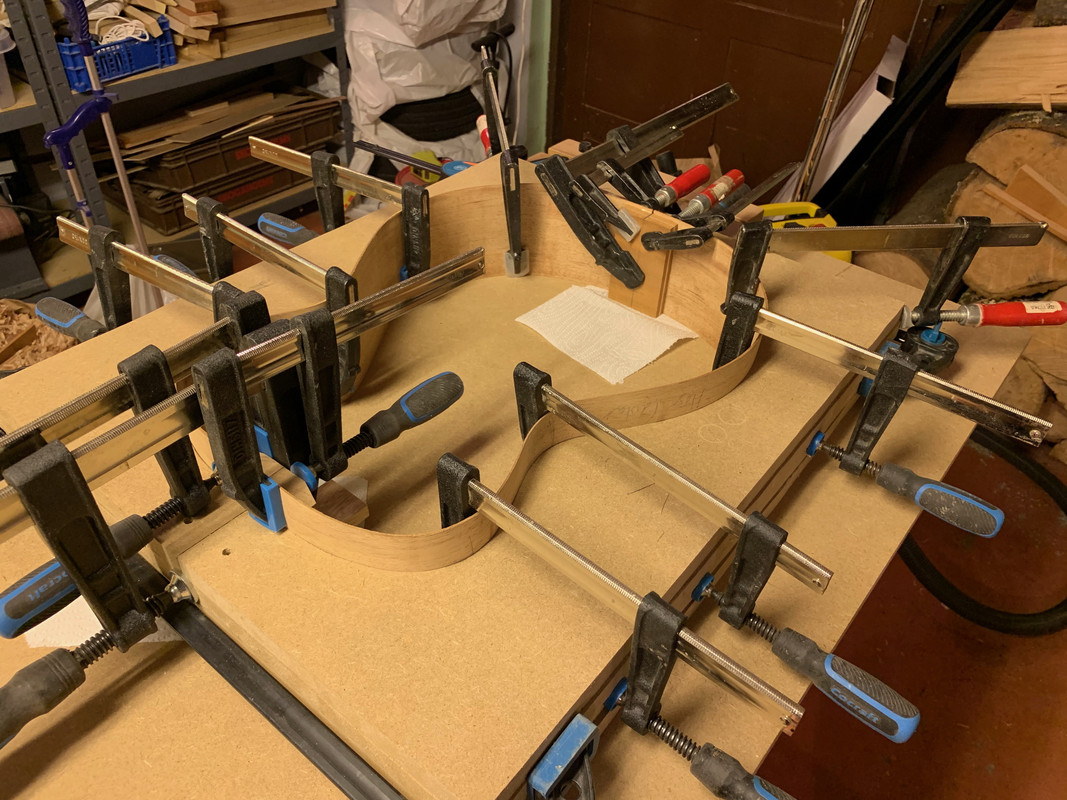 The next steps will be to bend linings for the top and add linings and struts to the rim set.
|
|
|
Post by lefranglais on Feb 27, 2020 9:45:10 GMT
Hi Lars, As I mentioned on my OM thread, I received advice from Steve Sheriff and Steve Fischer (who created the PRS guitar). Before we moved house and I found myself without a workshop, I'd almost finished another OM with a more 'modern' body shape and bracing like Steve Fischer's. You can see what his bracing looks like on his website.
This is what mine looks like.
|
|
|
Post by lars on Feb 27, 2020 20:44:59 GMT
Hi Lars, As I mentioned on my OM thread, I received advice from Steve Sheriff and Steve Fischer (who created the PRS guitar). Before we moved house and I found myself without a workshop, I'd almost finished another OM with a more 'modern' body shape and bracing like Steve Fischer's. You can see what his bracing looks like on his website.
This is what mine looks like.
Thank you! I’ve stumbled upon Fischer’s website before and used him as one of my inspirations. Your guitar looks very similar to what I have in mind. And, of course, it looks very nice.
|
|
|
Post by lars on Mar 7, 2020 20:17:32 GMT
Making the rim - part 2Before I could progress, I had to take one step back. I realized that the neck block had to be set lower to accommodate for the top profile. So I heated the glue joint with a hair dryer and reglued the neck block with a distance, like this:  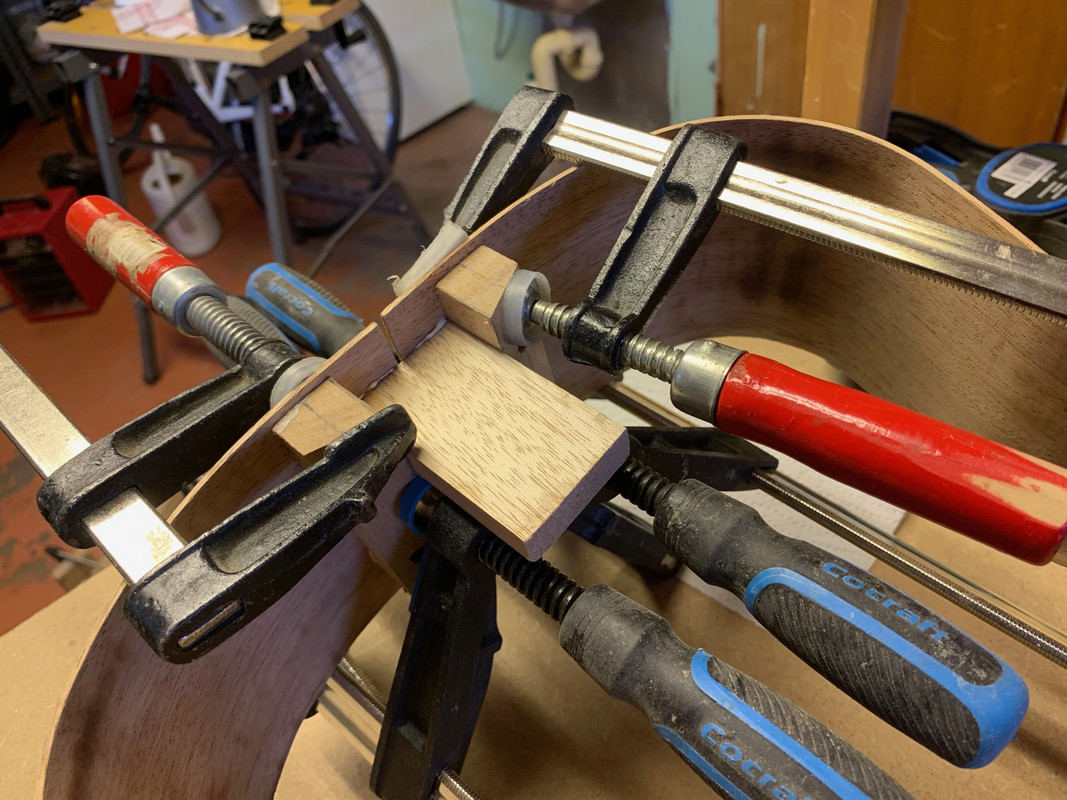 Next I had to calculate the profiles for top and back. I do it in a backward and over complicated way. Here is a view from my cad-model where I mark the radius with 1 mm steps: 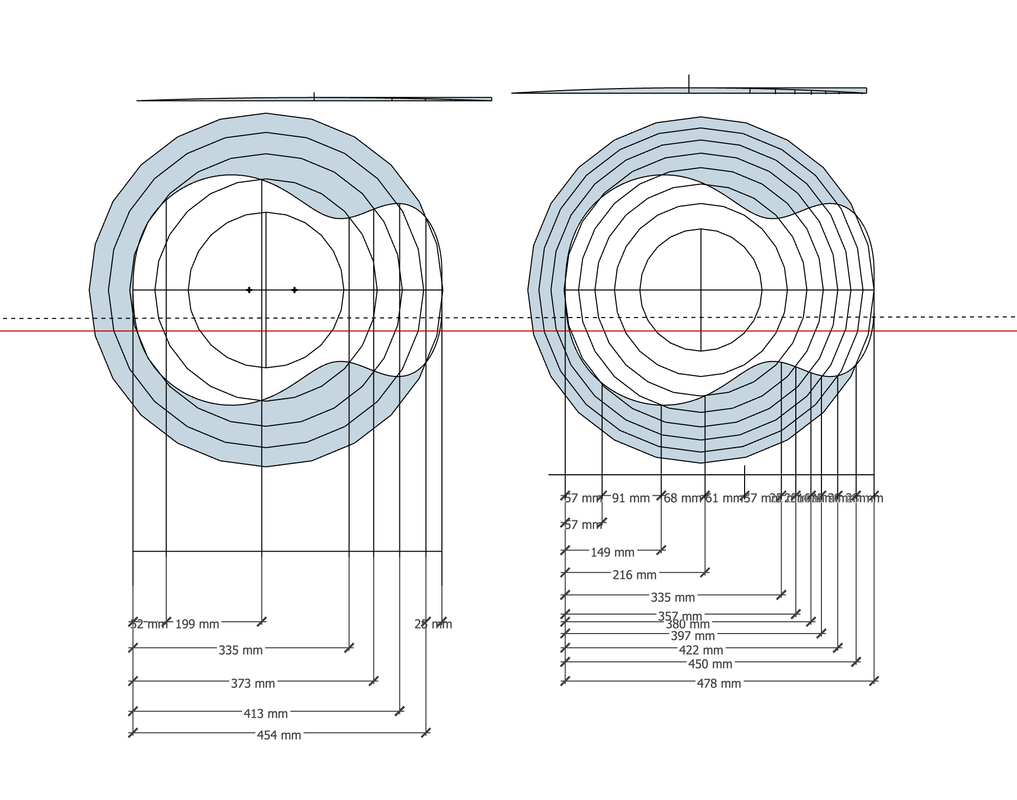 And I transfer it to the rim (I omit a lot of the steps - it's rather complicated :-)): 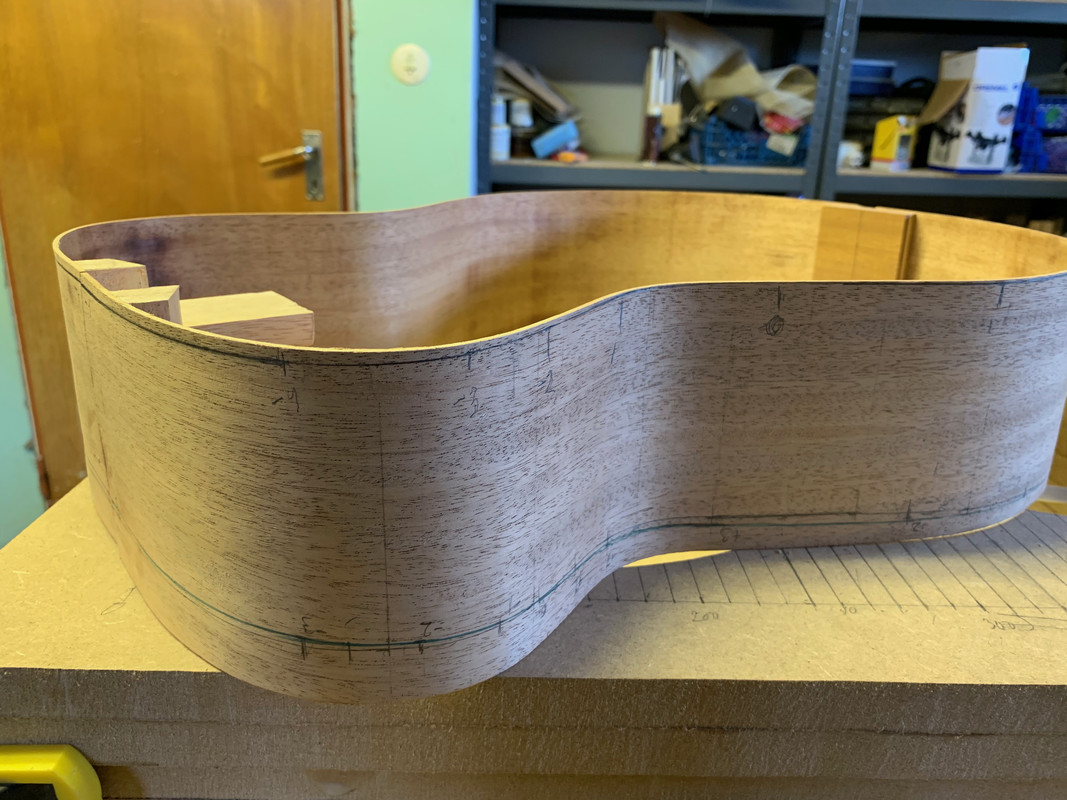 And I carve down almost to the profile with knife, chisel and plane (no photos of that). For the top I use laminated solid linings. Here are the bent linings for one of the sides in the mould: 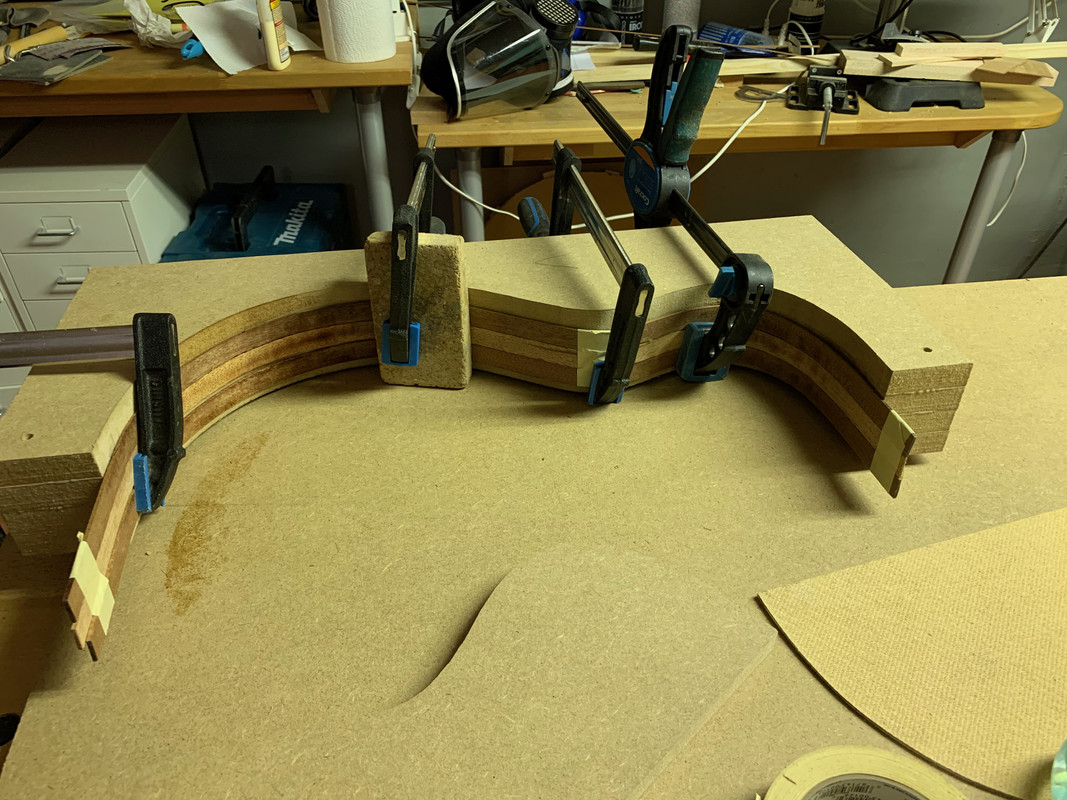 And I glue them one by one: 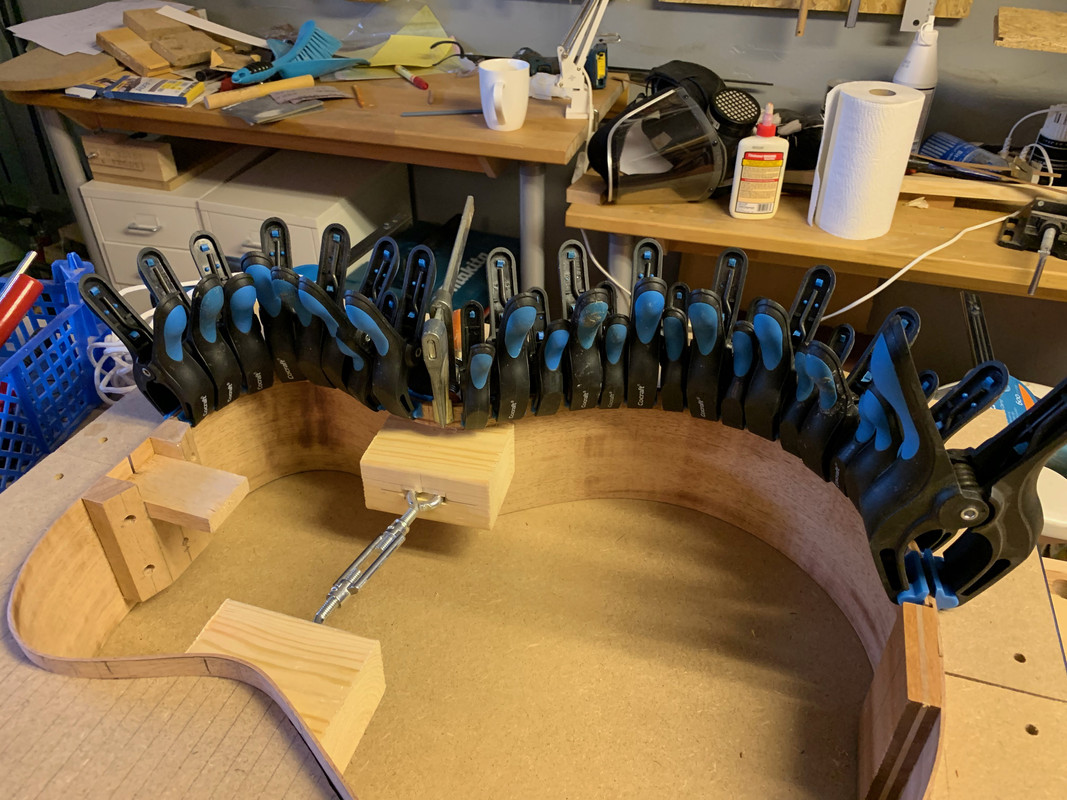 And after six times it looks like this: 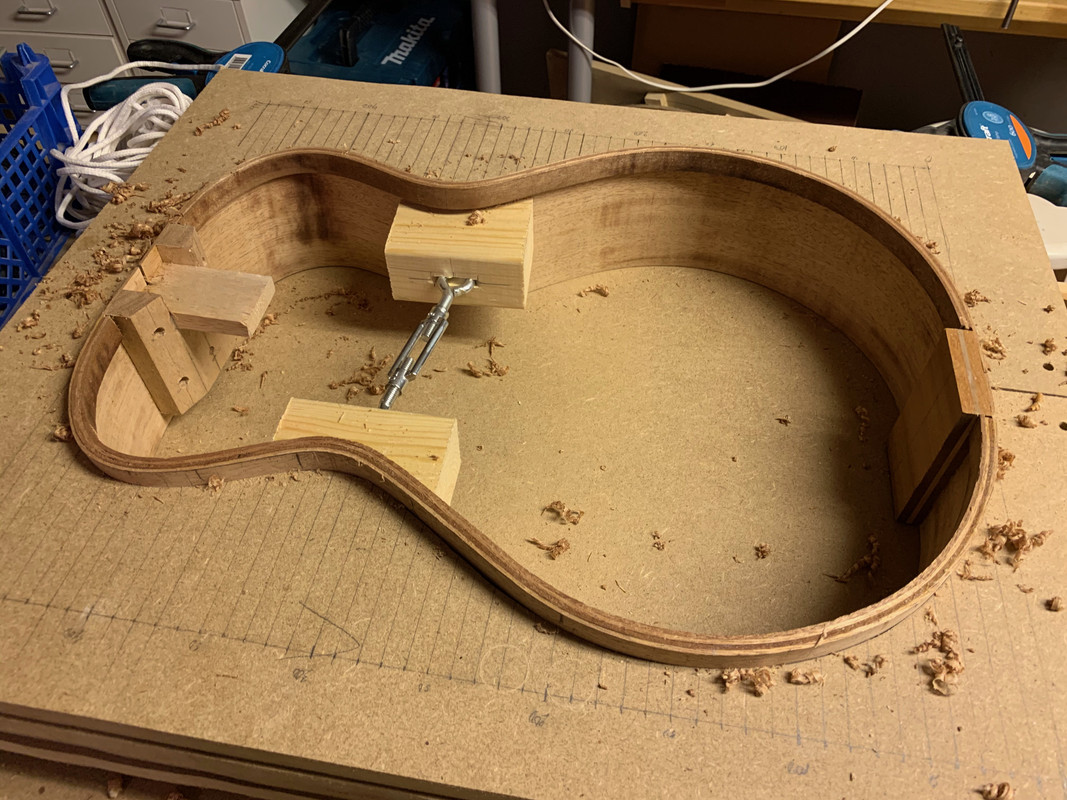 For the back I use reversed kerfed linings. I assume that the needs for stability and rigidity is not as big for the back and installing kerfed linings is a lot easier and quicker: Oops! No pictures taken from this work process... The next step is installing the vertical side struts. They are notched into the linings: 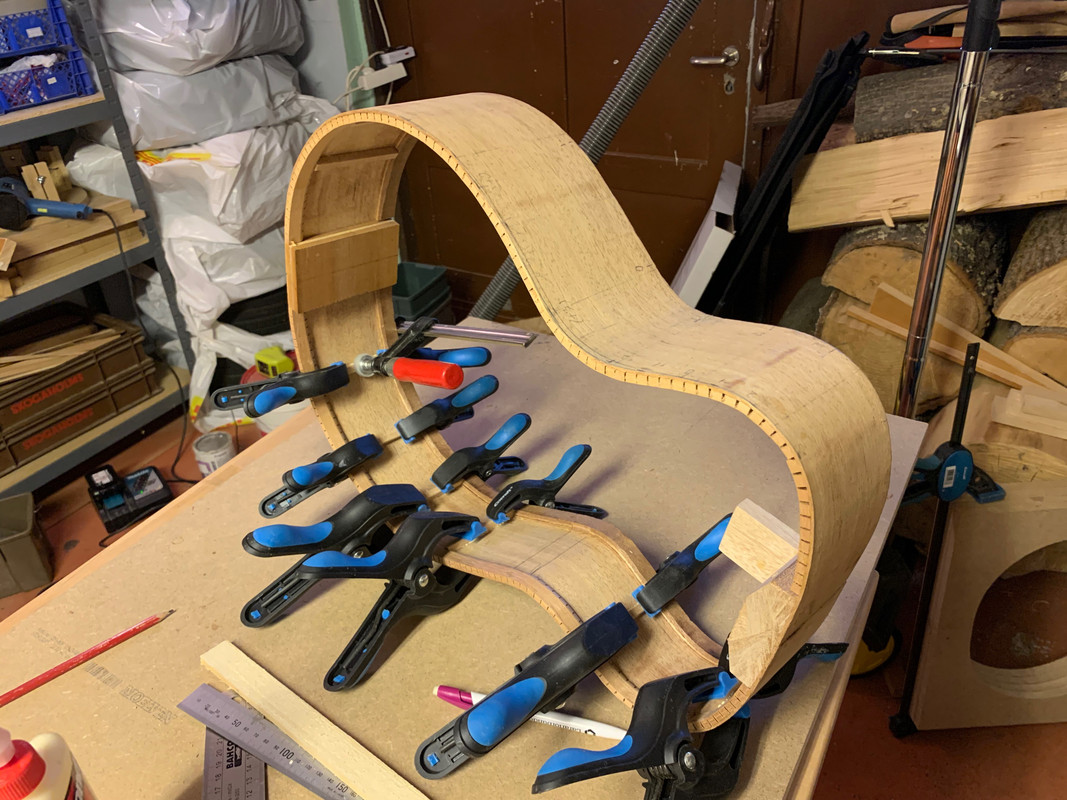 And the next last step is to install the 8 mm carbon fibre tubes: 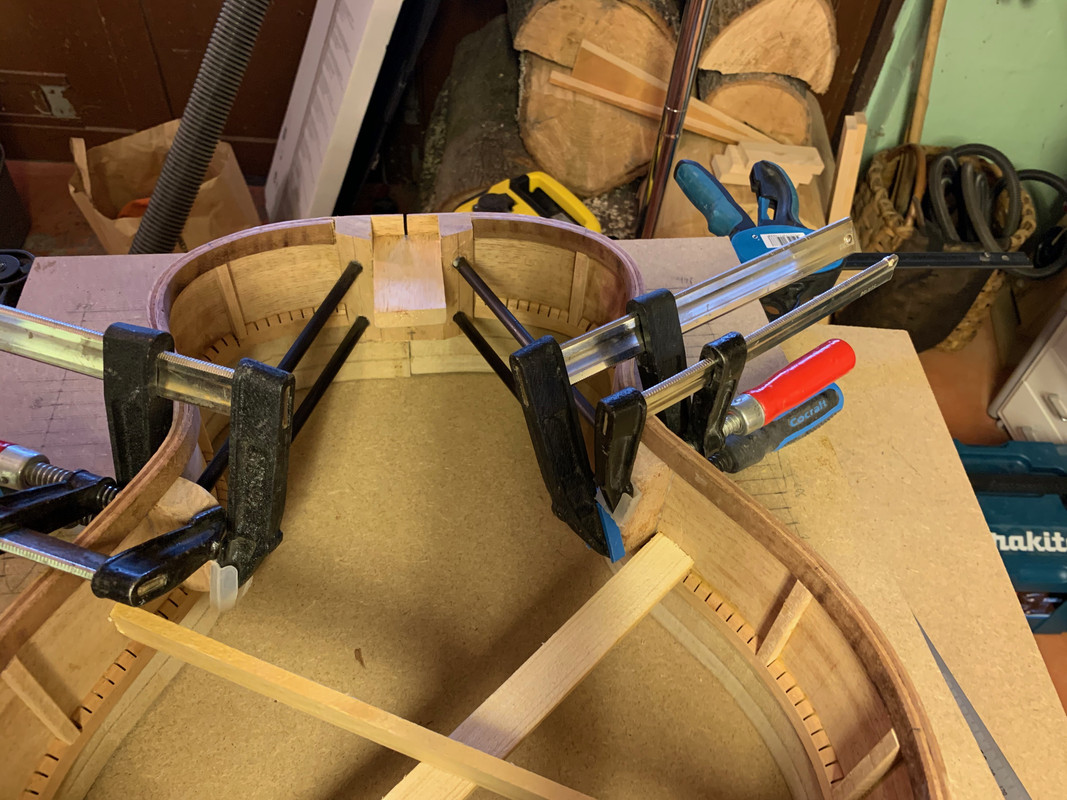 And after some sanding in the radius dishes I've got the completed rim set: 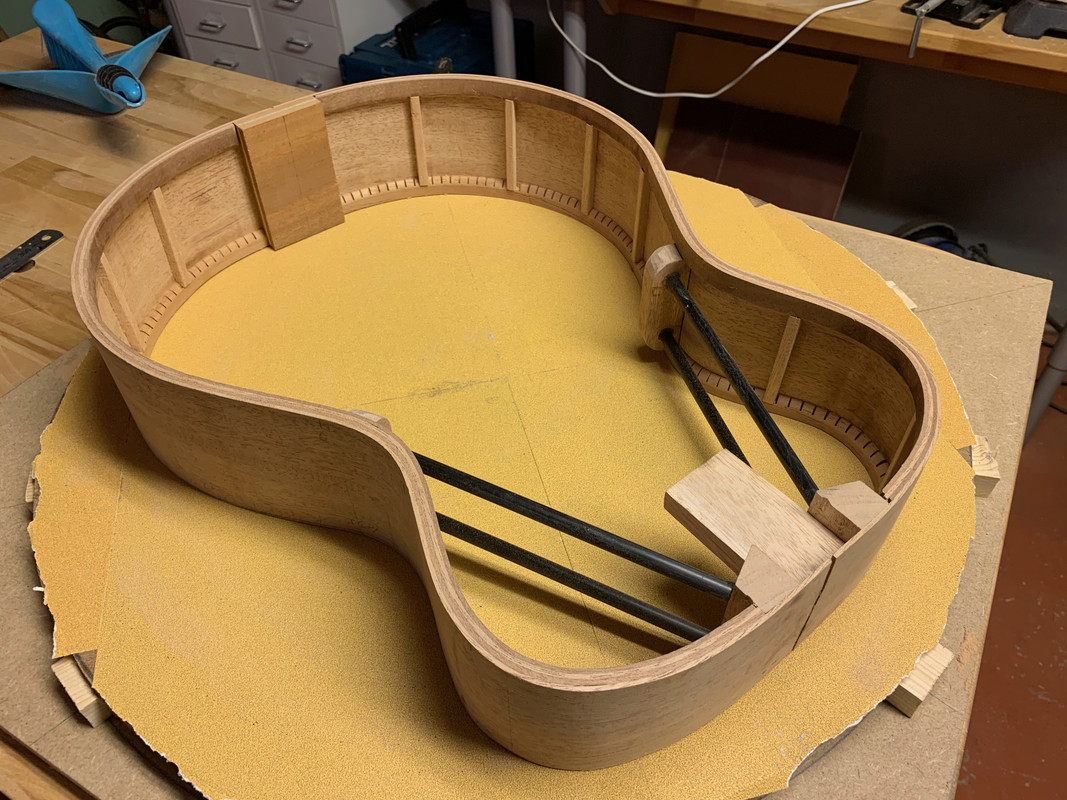 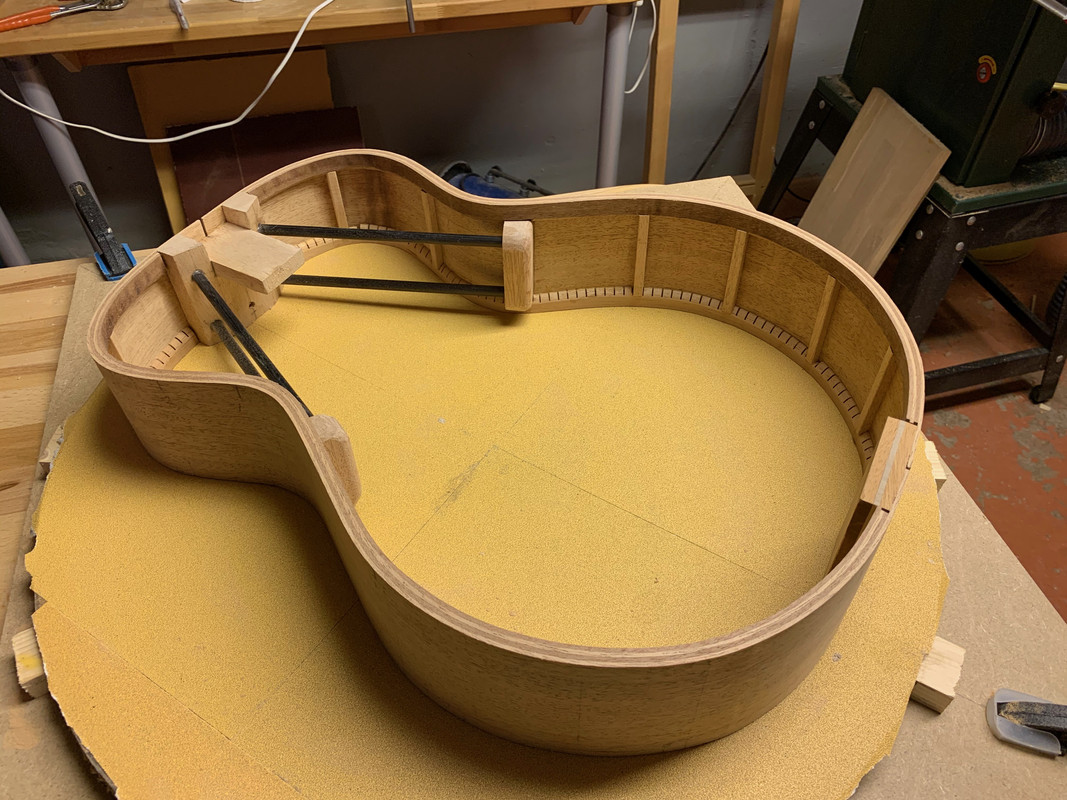 On to the bracing...
|
|
|
Post by lars on Mar 22, 2020 19:30:04 GMT
Adding a sound portA sound port was added to the rim. It was part of the plan all the time, but I nearly forgot about it until it was too late. A small leftover piece from the sides was bent on the hot pipe and glued to the inside of the rim cross grain to the side wood. Then the shape of the sound port was marked and I started to drill many small holes: 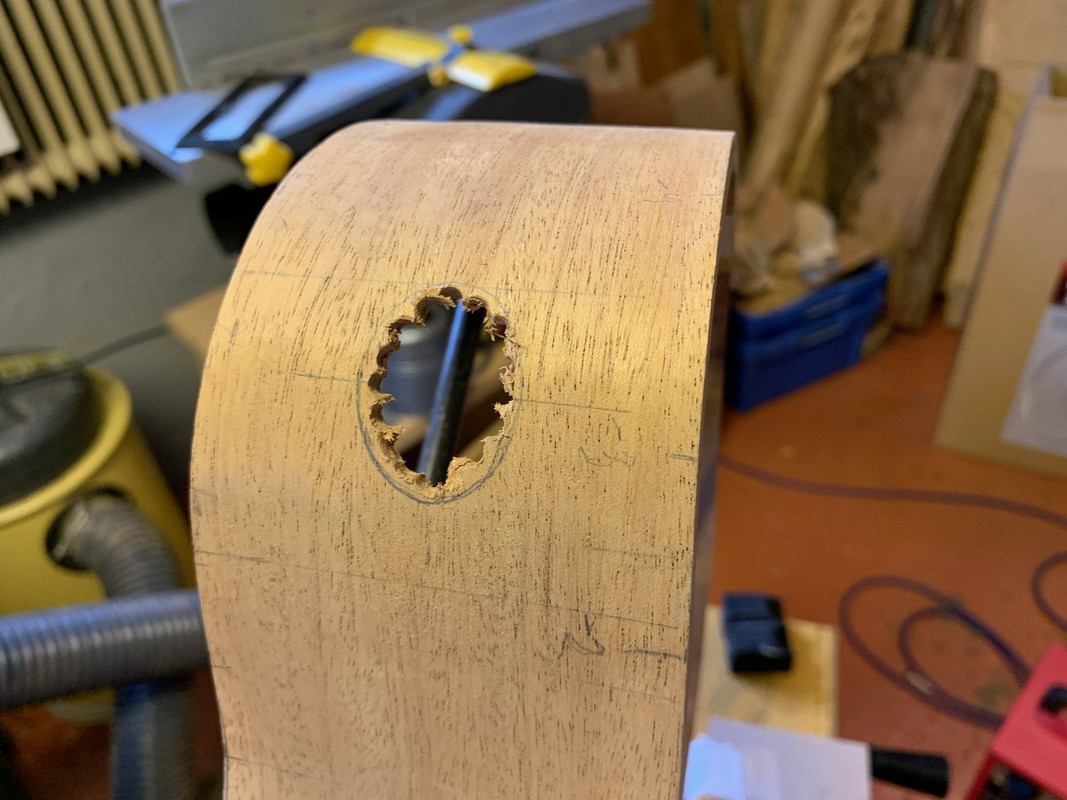 After some work with files the sound port had its final shape: 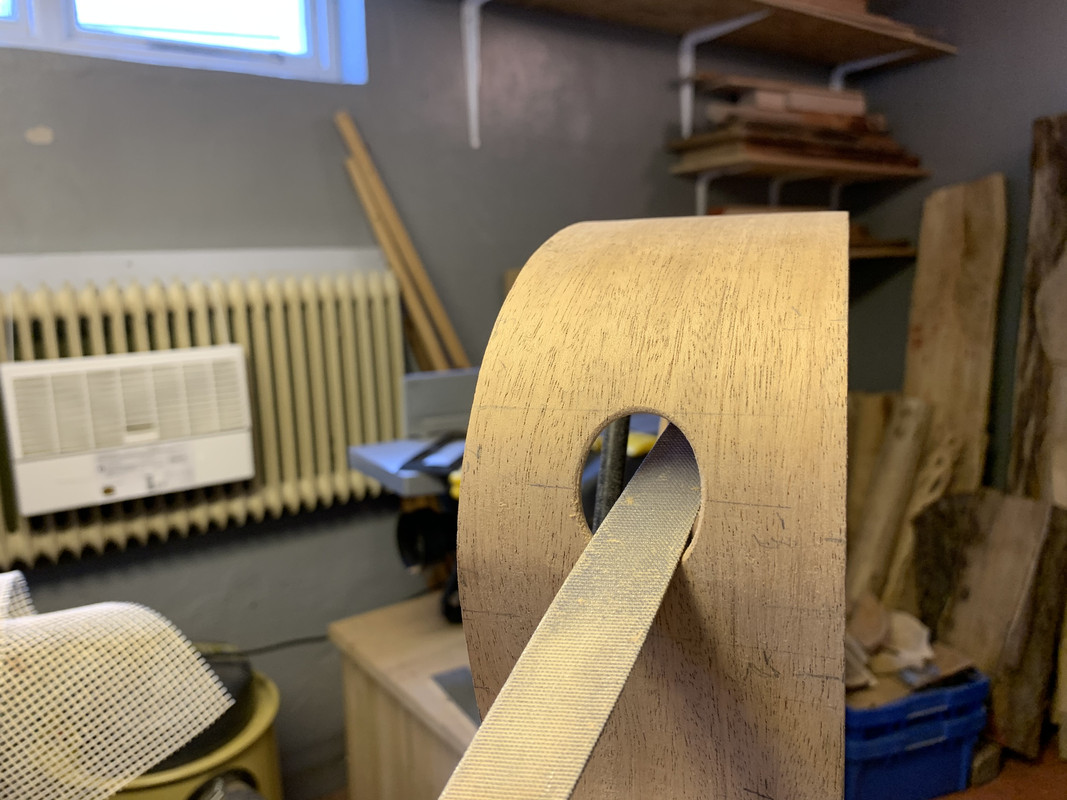 Here is a view from the inside: 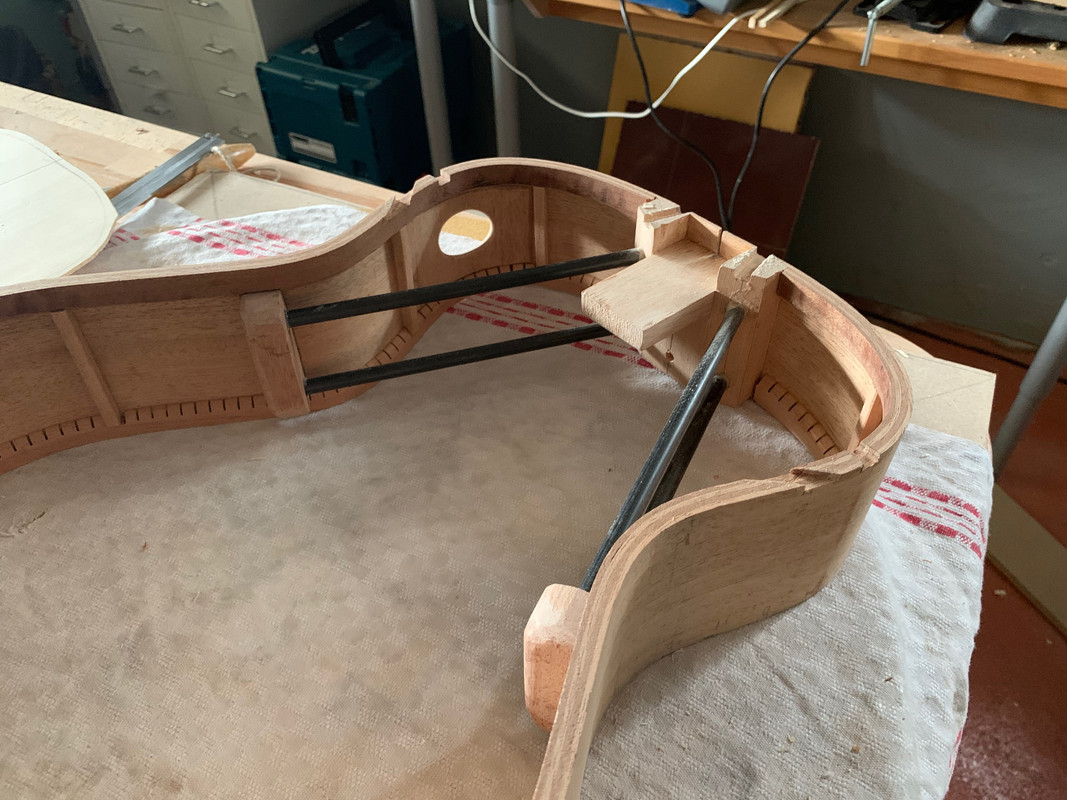
|
|
|
Post by lars on Mar 22, 2020 19:42:47 GMT
Bracing the topAll braces were cut in the band saw and their profiles were shaped/sanded in the radius dish. First I glued on the x-braces: 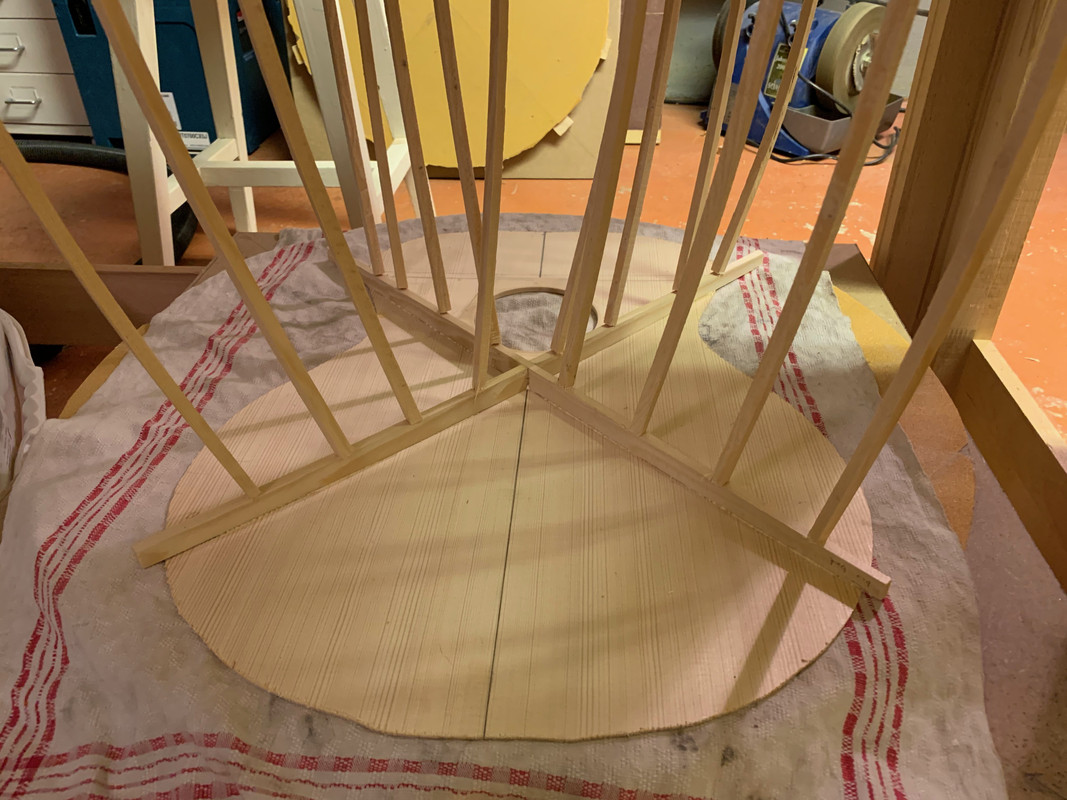 And the laburnum bridge plate was added: 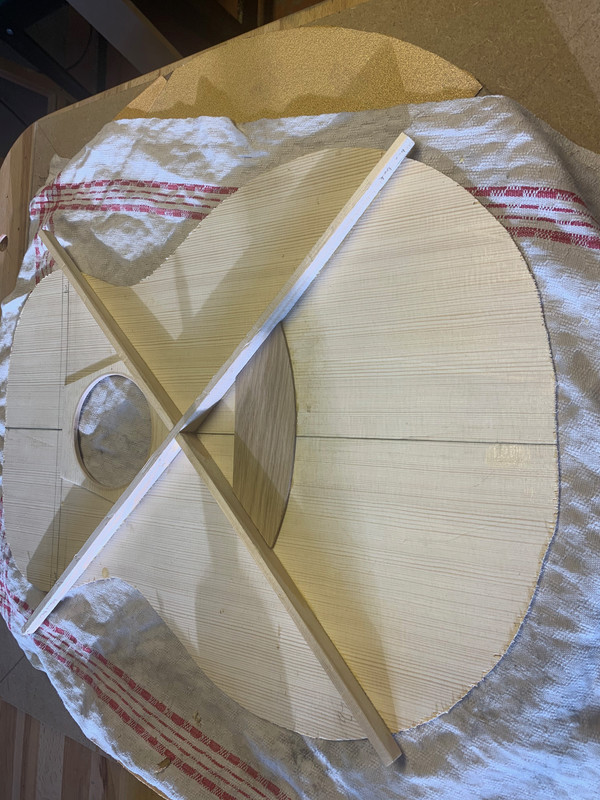 And then the fan braces. In my original plan I had just three of these, but due to the thin top plate I decided to go for four fan braces: 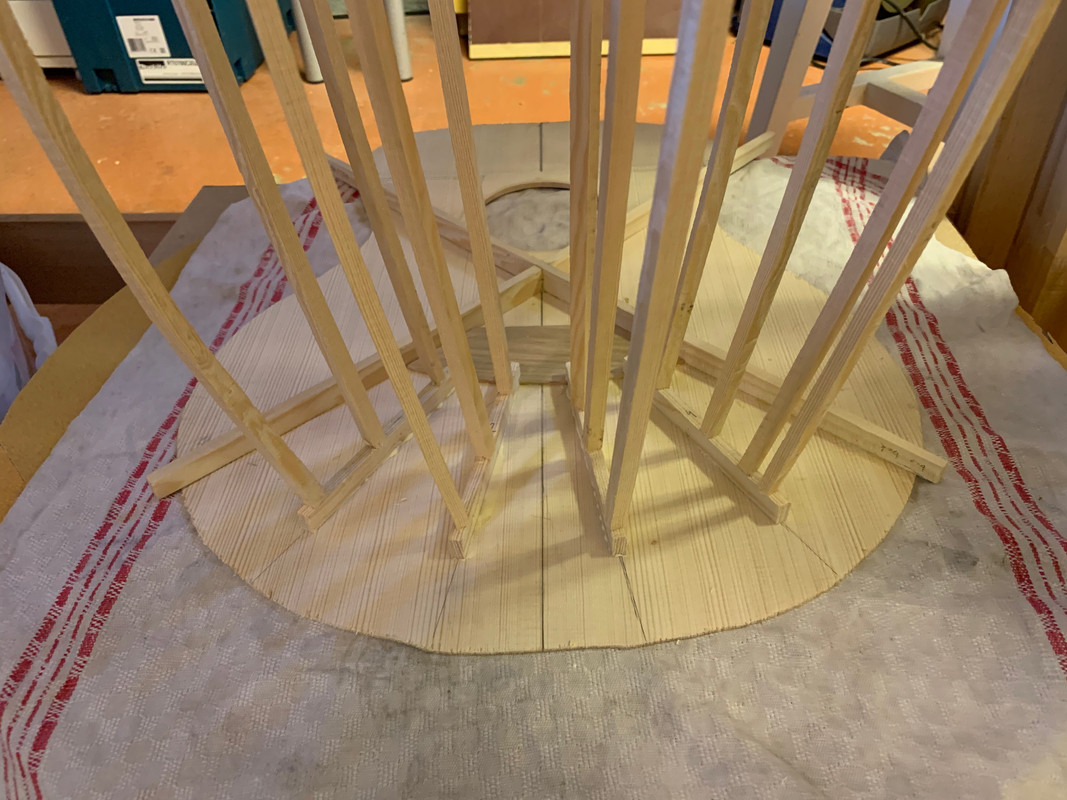 And then the A-braces: 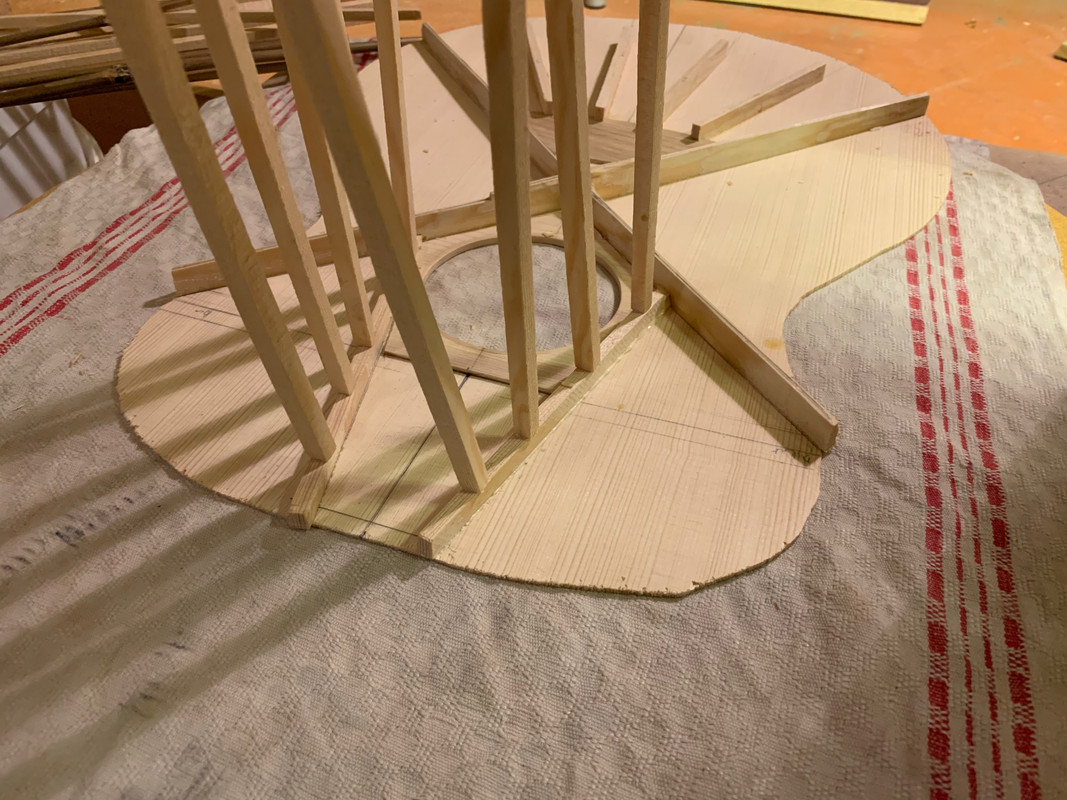 And lastly the UTB (upper traverse brace) and finger braces. I added two finger braces on each side, instead of just one, for increased stability: 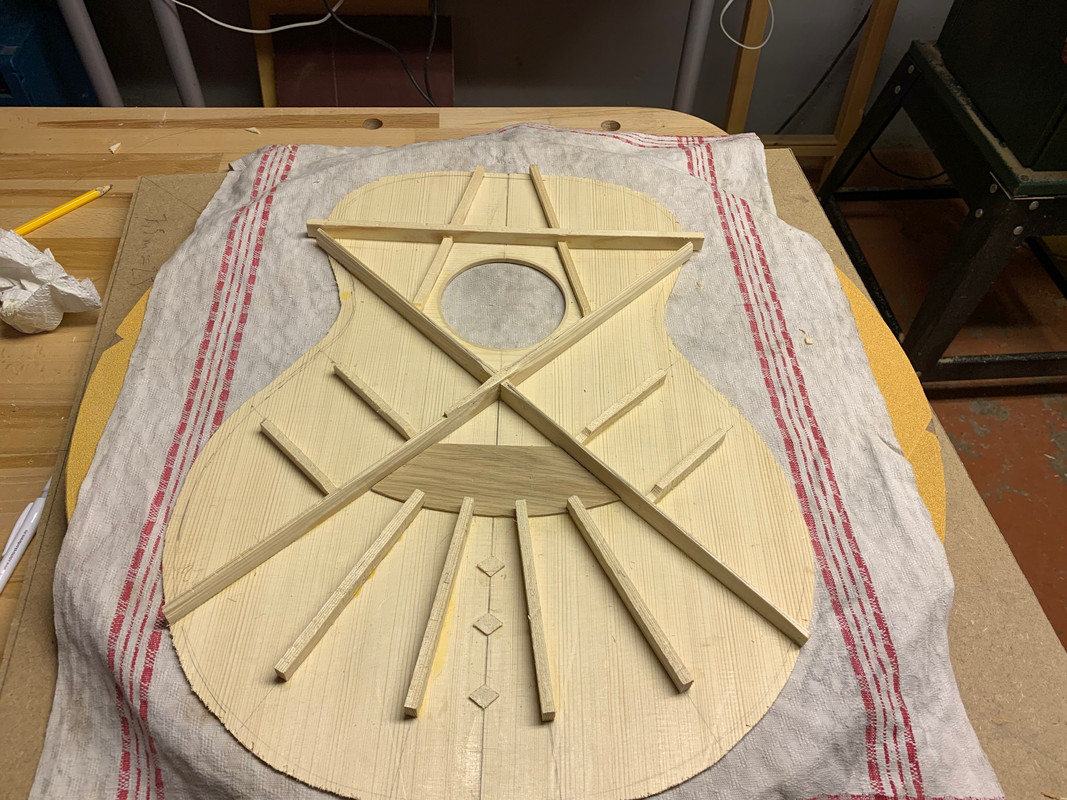 And then came the nervous process of shaping the braces. To "voice" them. Ehrmm, to cut, flex and tap and cut, flex and tap and wonder what I'm supposed to hear and feel. And to hope that you're not stopping far too late - and not too early either. As this is my first guitar and my first instrument with a fixed pin bridge it's really a trial and error process. Anyway - here I'm almost done: 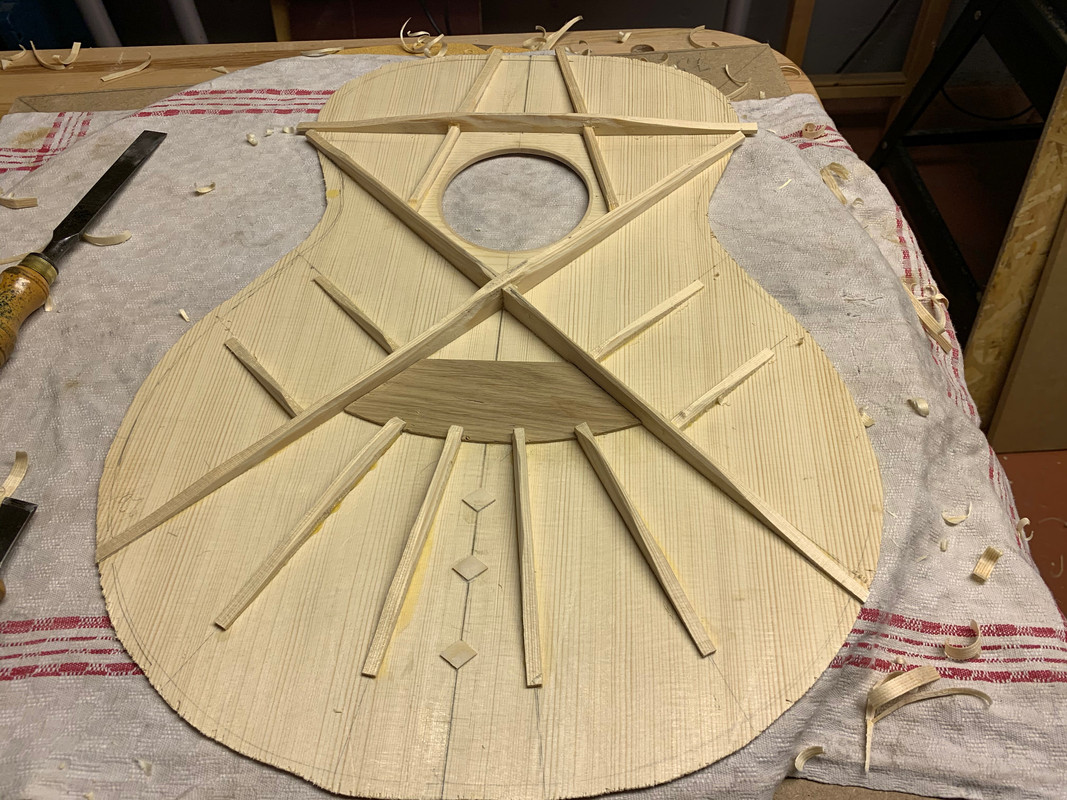 And here I'm completely done: 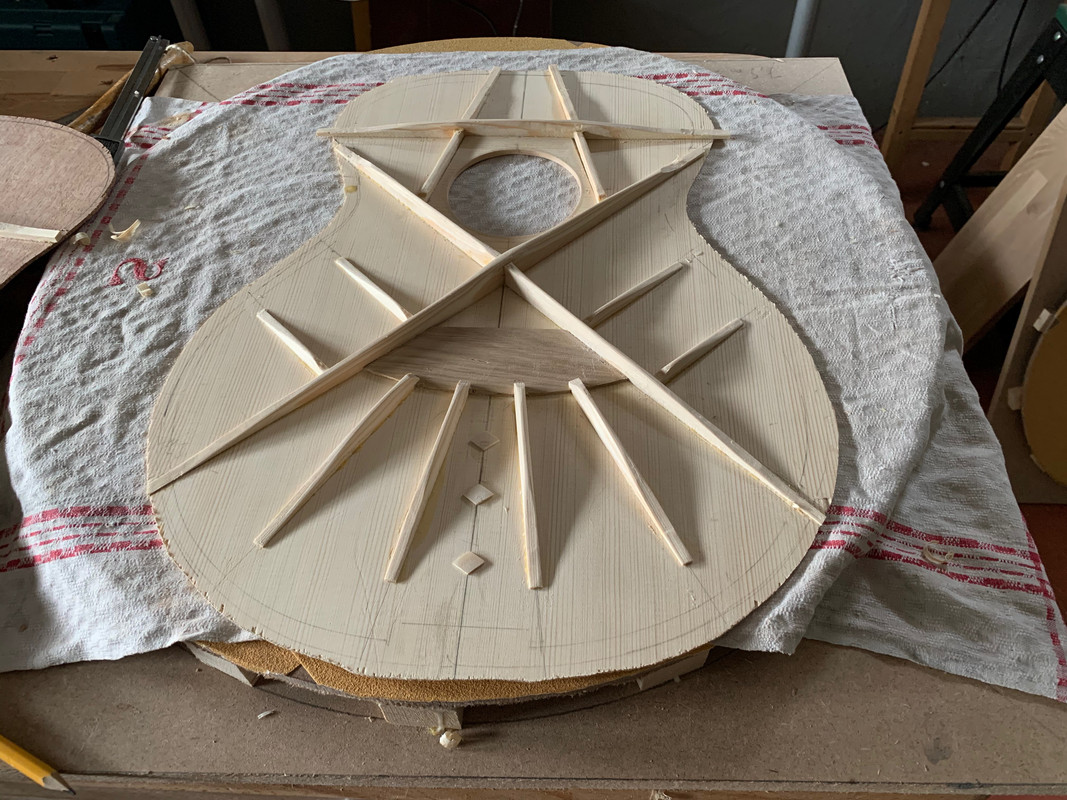 I've deliberately avoided to sand or scrape the surface of the top. I was longing to have a clean inside of the box, but I decided to not take a micrometer extra from the top thickness so pencil marks and everything is left.
|
|
|
Post by lars on Mar 22, 2020 19:49:30 GMT
Bracing the back
First I glued the spruce back strip . 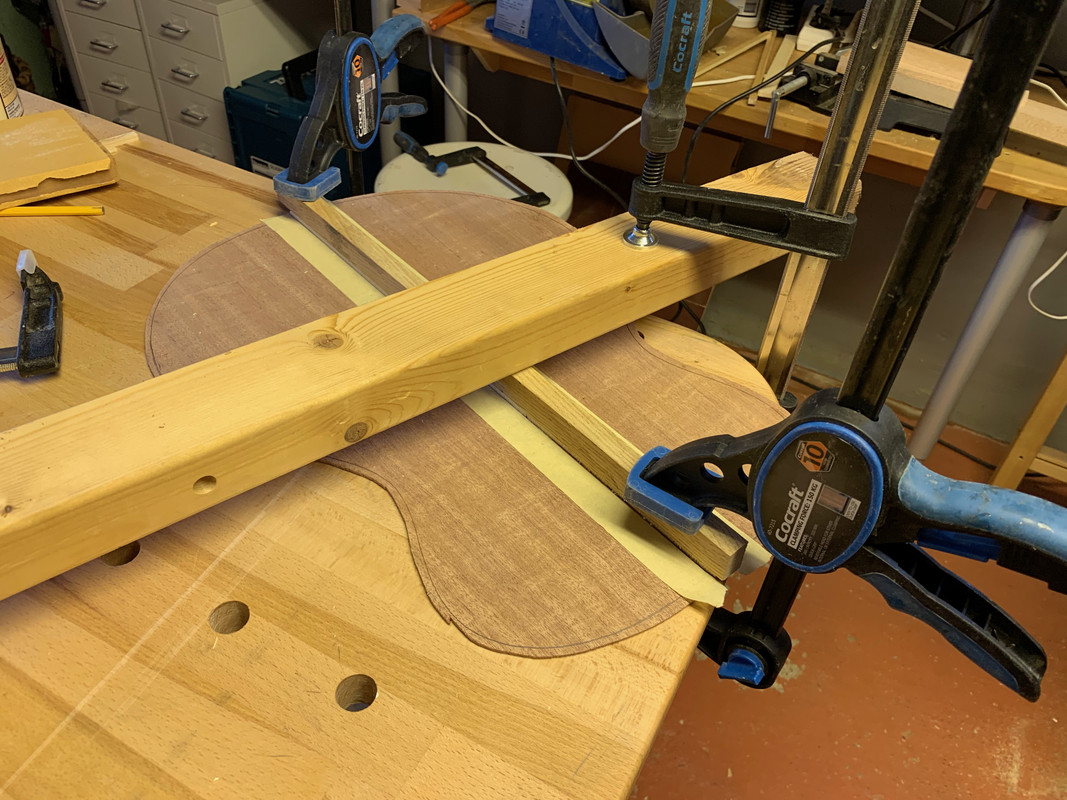 I went for a traditional ladder bracing. 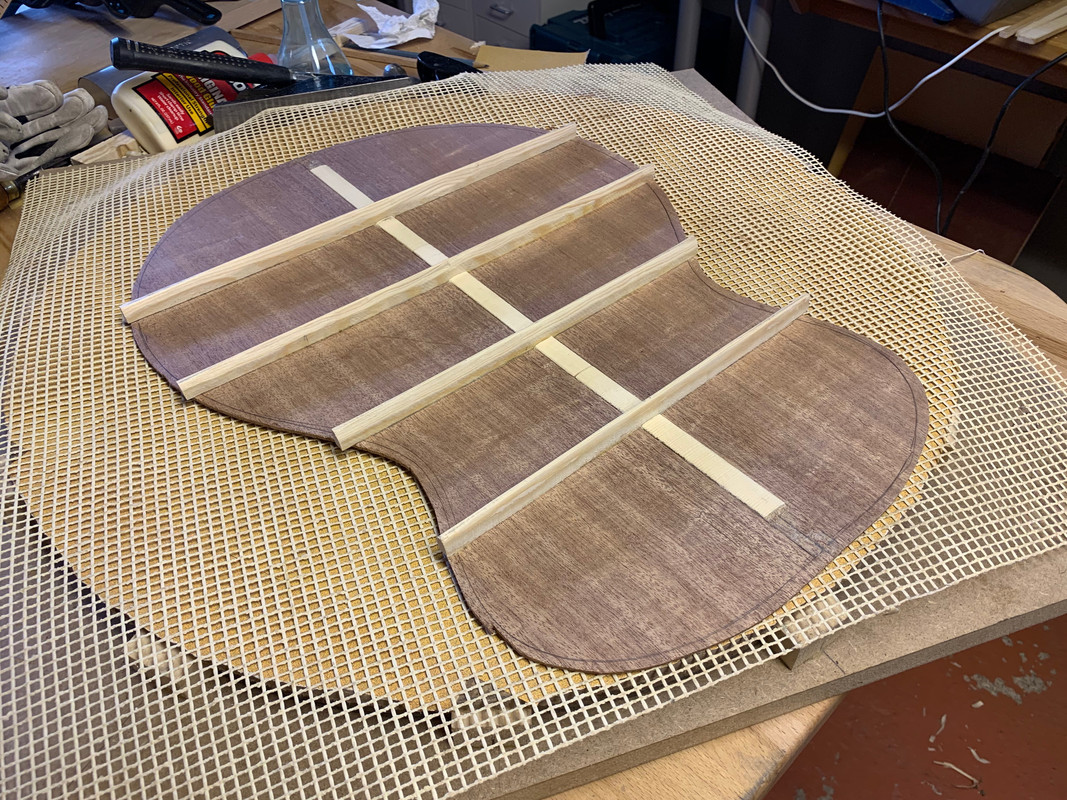 And here I'm in the process of shaping and "tuning" them: 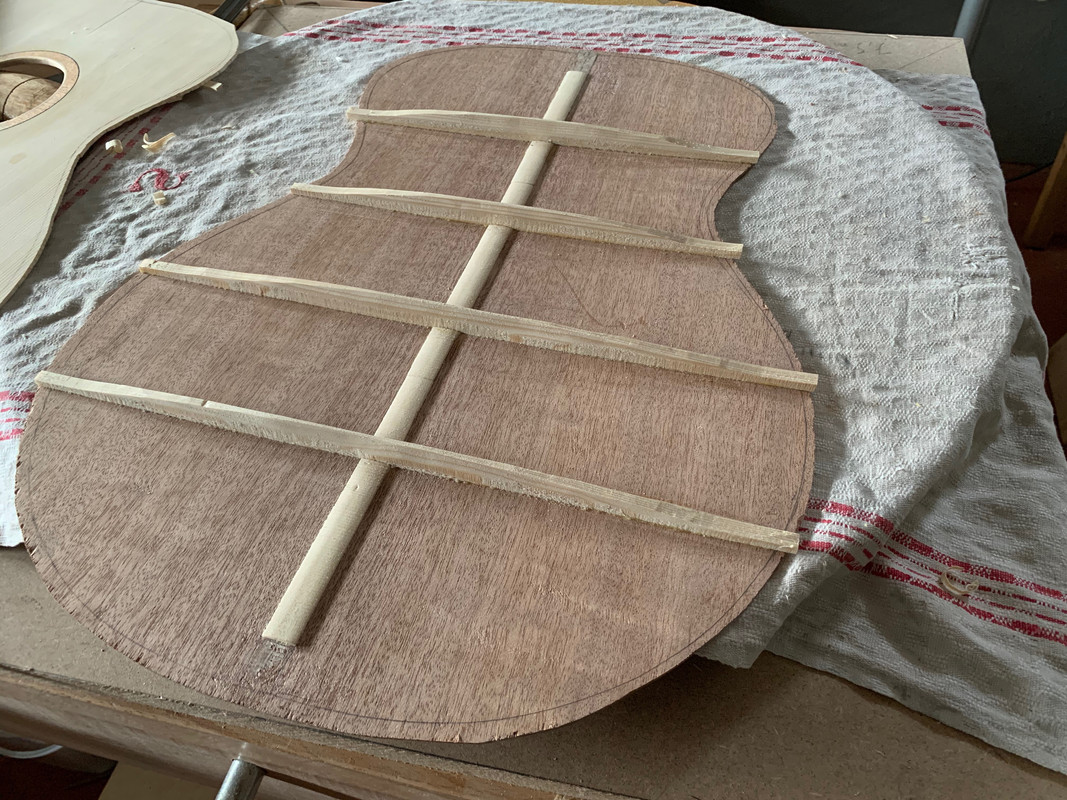
|
|
|
Post by lars on Mar 22, 2020 19:59:42 GMT
Assembling the bodyNotches was cut in the rim to inlet the top and back braces. That is - some of the top braces. The fan and finger braces were not notched into the sides and the lower legs of the x-braces were only about 1-2 mm thick where they were inlet. Before I glue on the top I write some info and put my signature to the inside: 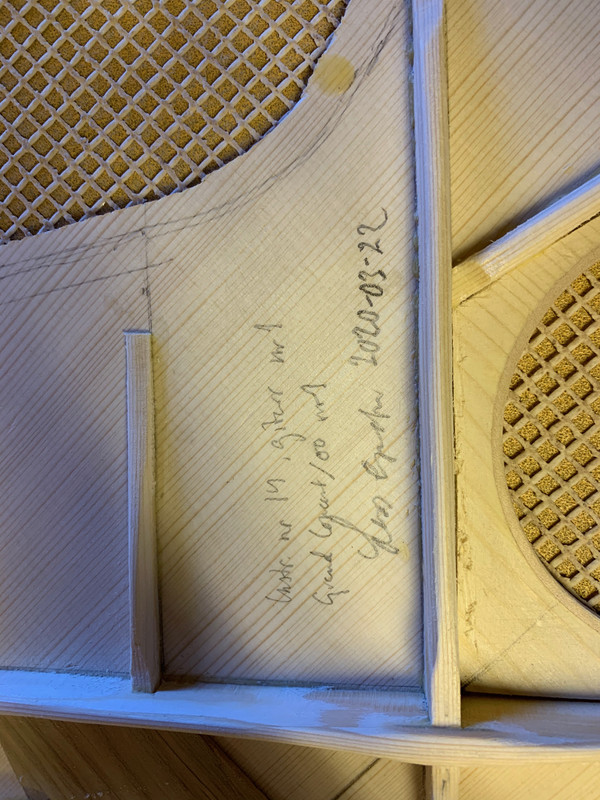 And here the top is glued to the rim: 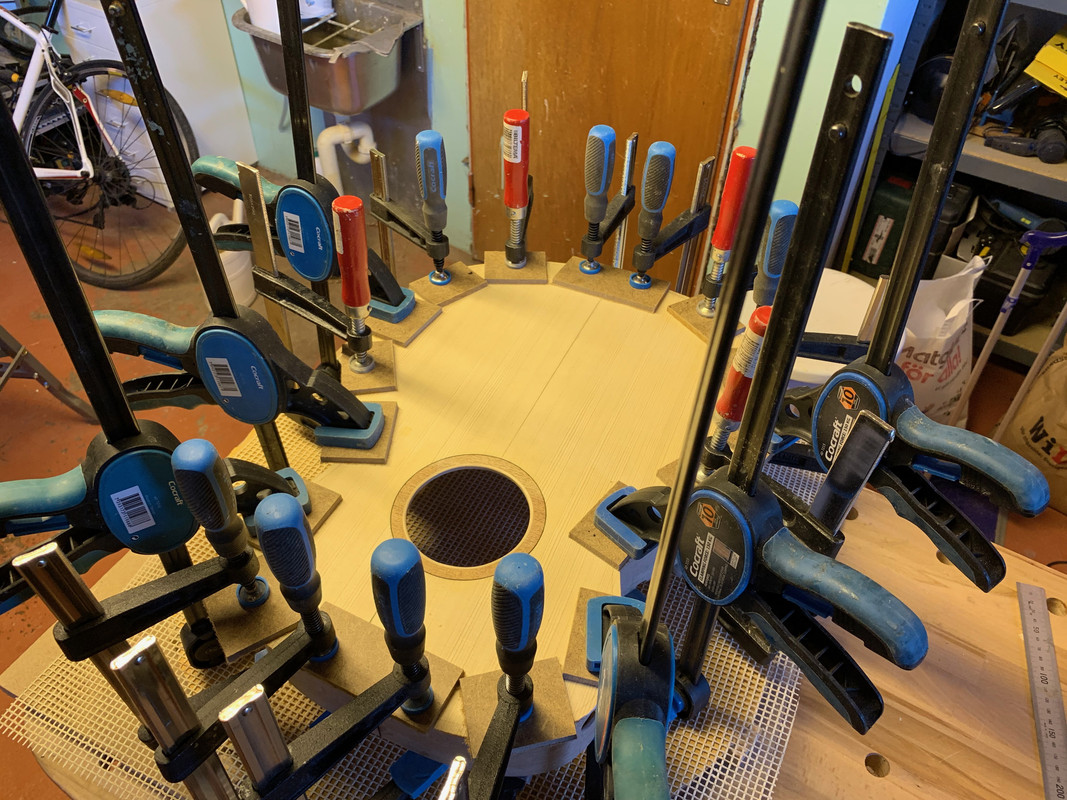 And here is a last view of the inside (after the top is glued but before the back): 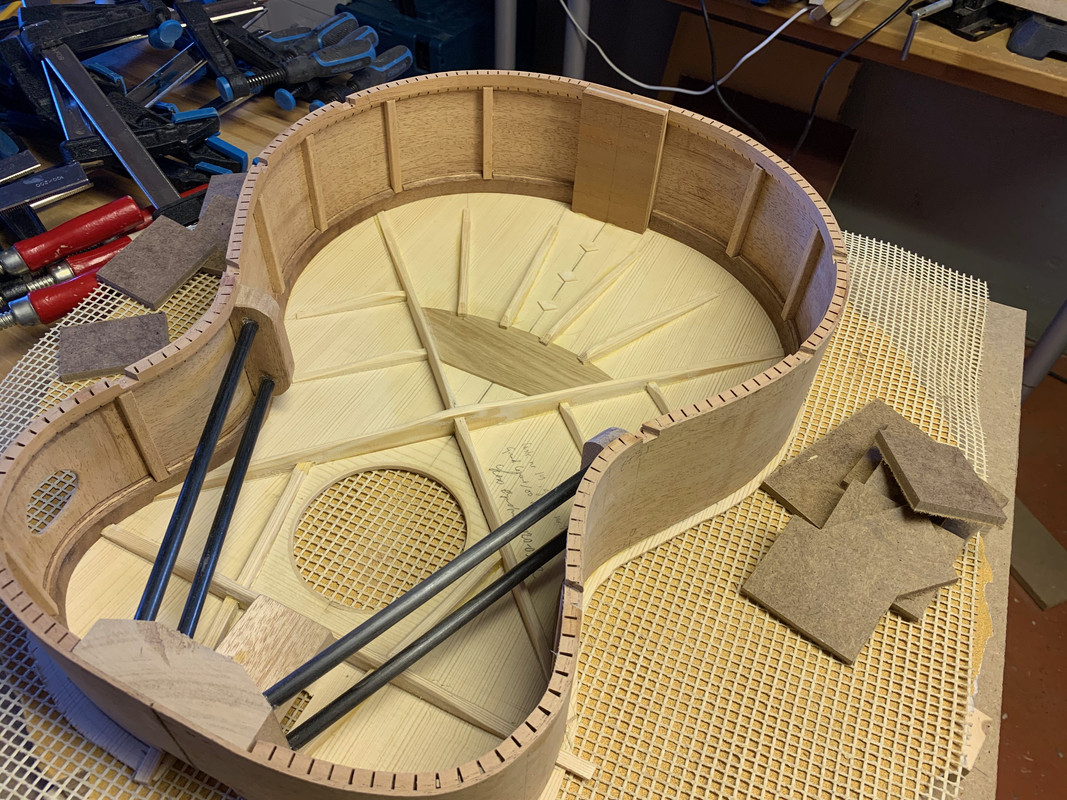 And then it's time to add the back: 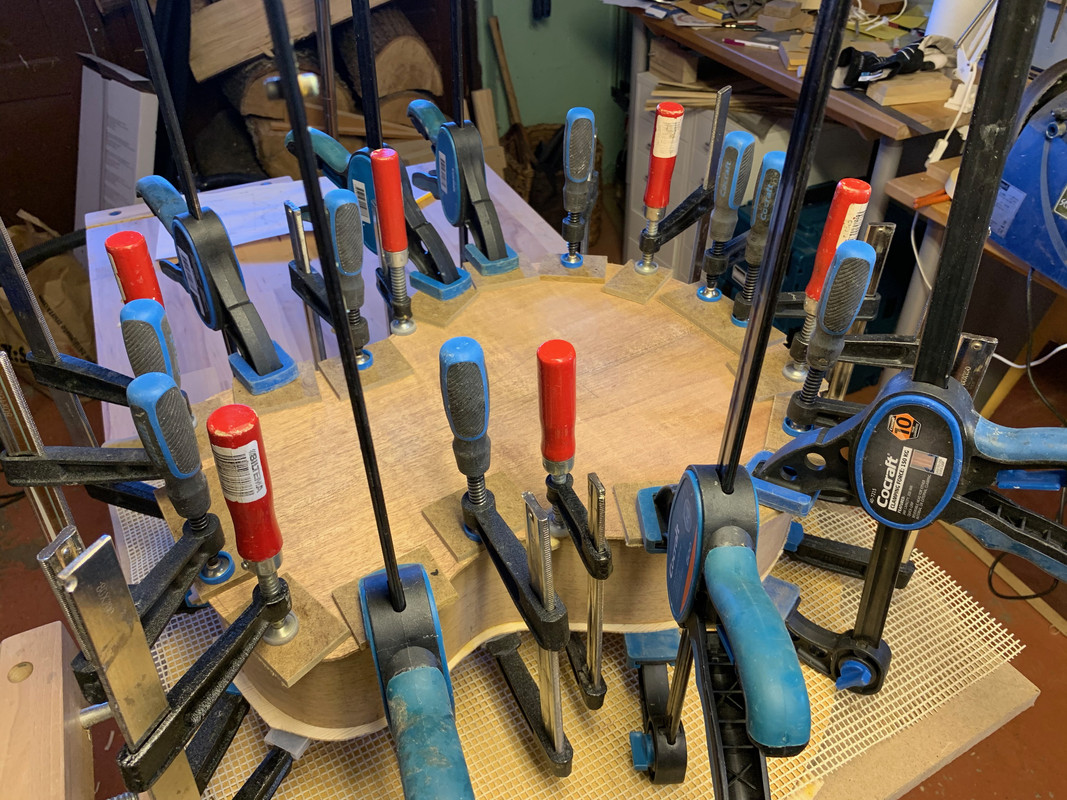 And after some trimming I've got an assembled body! 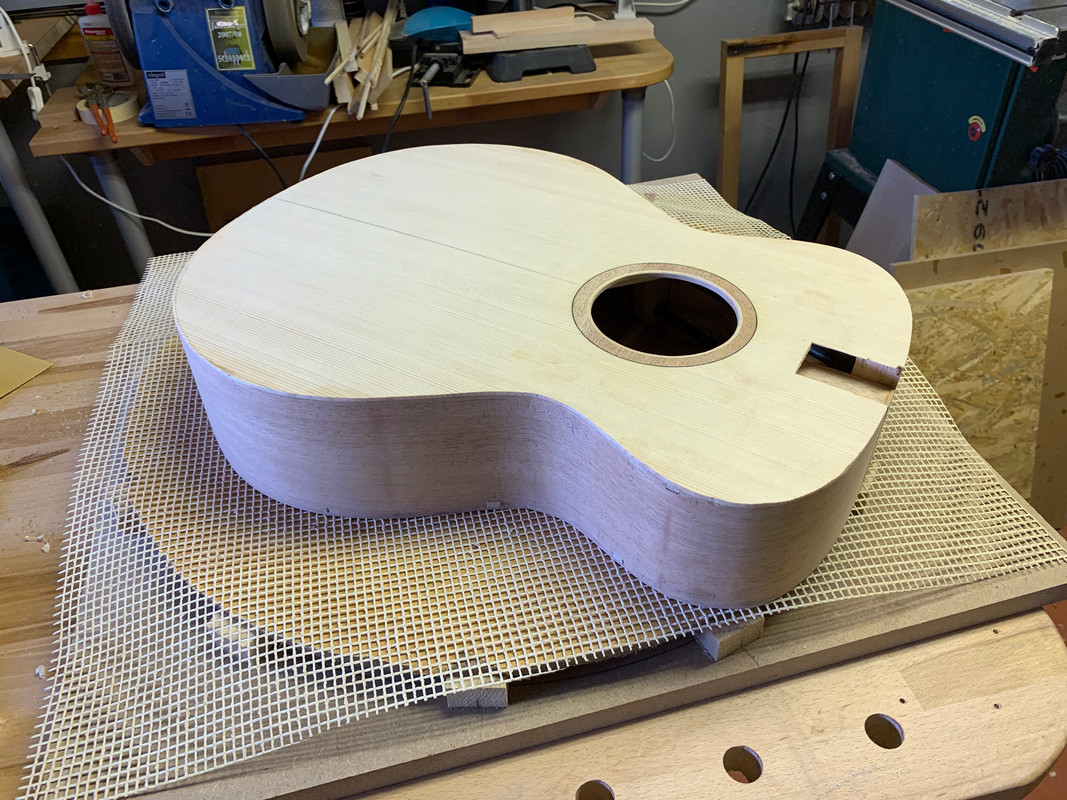 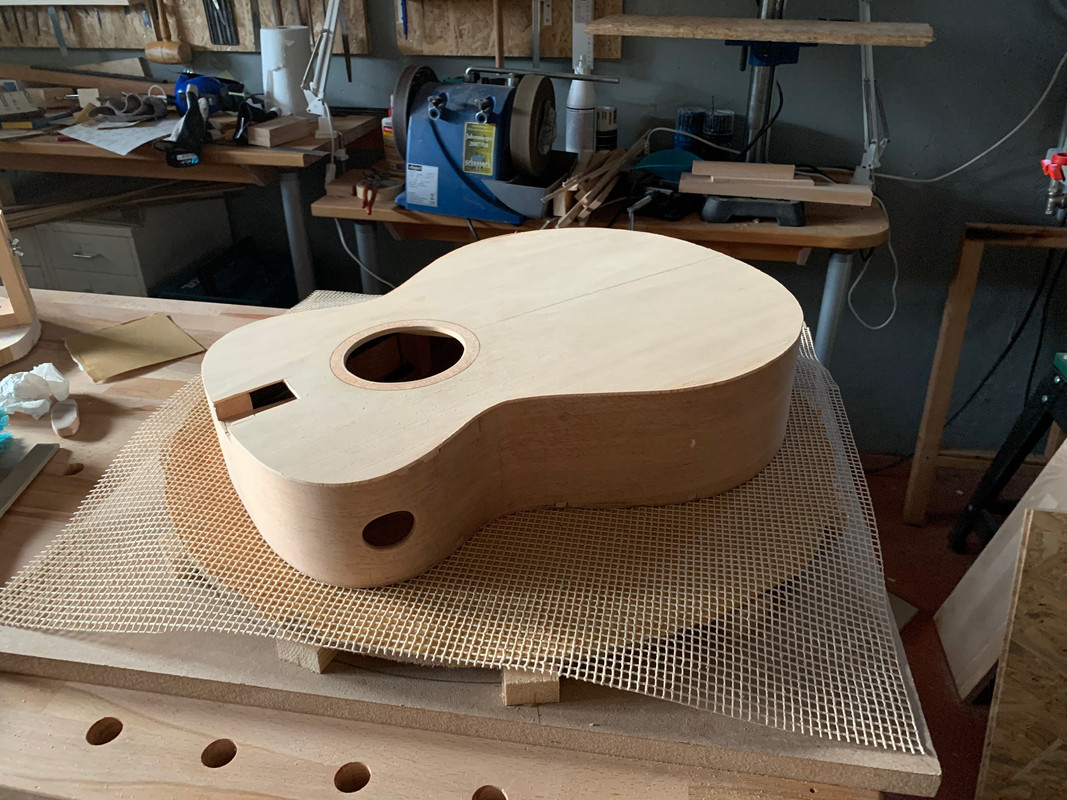 And it feels like I've passed a milestone today!
|
|
ocarolan
Global Moderator
CURMUDGEONLY OLD GIT (leader - to join, just ask!)
Posts: 35,756
Mini-Profile Background: {"image":"","color":"c0cfe1"}
Mini-Profile Name Color: 182a3f
Mini-Profile Text Color: 733a1c
|
Post by ocarolan on Mar 22, 2020 23:27:48 GMT
Box closed! Yay!! Congrats!!! 
|
|
colins
Luthier / Guitar Maker
Posts: 2,397
|
Post by colins on Mar 23, 2020 9:37:09 GMT
|
|